In the industrial sector, float type liquid level gauges play a significant role in achieving these objectives by providing precise and reliable measurements of liquid levels in various industrial applications. This comprehensive guide aims to explore the intricacies of float type liquid level gauges, their importance, working principles, types, advantages, troubleshooting and maintenance etc. By the end of this guide, you will have a thorough understanding of how float type liquid level gauges contribute to enhancing precision and safety in industrial operations.
Understanding Float Type Liquid Level Gauges
Float type liquid level gauges are essential instruments used to measure the level of liquid in a container or a tank. They consist of a float, which rides on the surface of the liquid, connected to a mechanical or electronic indicator that displays the level. These gauges are widely employed in industries such as oil and gas, chemical processing, pharmaceuticals, food and beverage, and water treatment, where accurate monitoring of liquid levels is critical for operational efficiency and safety. The design and construction of float type liquid level gauges may vary based on the specific application requirements, but their fundamental principle remains consistent across different types.
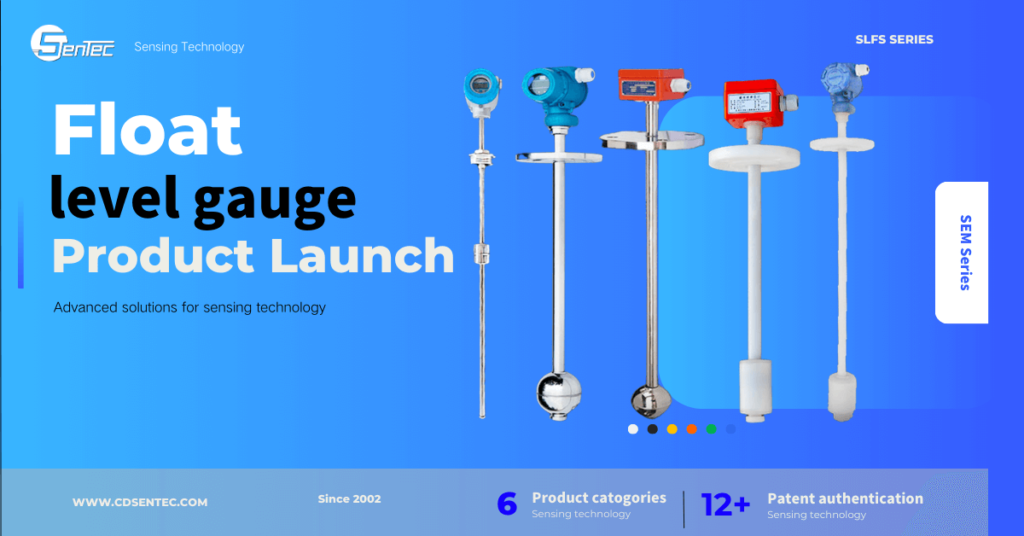
Importance of Float Type Liquid Level Gauges in Industrial Operations
The importance of float type liquid level gauges in industrial operations cannot be overstated. These instruments serve as the eyes of the process, providing real-time information about the liquid levels in tanks and vessels. By accurately measuring and monitoring liquid levels, float type liquid level gauges enable operators to maintain optimal inventory levels, prevent overflows or run-dry situations, and ensure the safe and efficient operation of industrial processes. Moreover, in industries where the stored liquids are hazardous or flammable, the use of reliable level gauges like float type gauges becomes imperative for ensuring the safety of personnel and the surrounding environment.
How Float Type Liquid Level Gauges Work
The working principle of float type liquid level gauges is based on the buoyancy of the float and its movement in response to the liquid level changes. As the liquid level in the tank or vessel fluctuates, the float attached to the gauge rises or falls accordingly. This movement is then transmitted to the indicator, which displays the current liquid level. In some cases, the floats are equipped with magnets that actuate reed switches or magnetically coupled indicators, providing a non-contact and reliable method of level indication. The simplicity and effectiveness of this working principle make float type liquid level gauges a popular choice for a wide range of industrial applications.
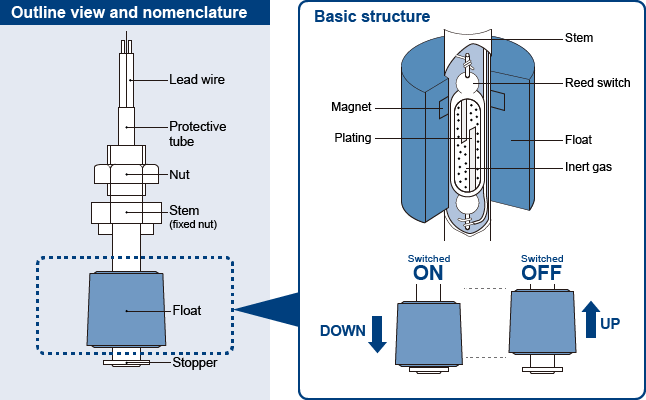
Advantages of Using Float Type Liquid Level Gauges
The utilization of float type liquid level gauges offers several advantages that contribute to their widespread adoption in industrial settings. These gauges provide real-time and continuous level measurement, enabling operators to monitor liquid levels without interrupting the process. Additionally, the simplicity of their design and operation makes float type liquid level gauges reliable and easy to maintain. They are also suitable for a wide range of liquid types, including corrosive, viscous, and high-temperature liquids, making them versatile for diverse industrial applications. Furthermore, the availability of different types and materials allows for customization based on specific process requirements, further enhancing their utility and effectiveness.
3 Common Issues and Troubleshooting Tips for Float Type Liquid Level Gauges
While float type liquid level gauges are known for their reliability, they may encounter issues due to factors such as material buildup, mechanical wear, or environmental conditions. Common problems include inaccurate level readings, float malfunction, and visibility obstructions in the gauge. To address these issues, regular inspection and maintenance are essential. Cleaning the gauge components, ensuring proper float movement, and checking for any obstructions can help resolve many common problems. Additionally, understanding the operating conditions and environmental factors that may affect the gauge’s performance is crucial for troubleshooting and maintaining the accuracy of liquid level measurements.
Here you can learn the solutions to common faults of Float Type Liquid Level Gauge:
Fault 1. Float Type Liquid Level Gauge indication is abnormal
The indication of the float level gauge is abnormal, which is a very common fault of the float level gauge. Usually there are the following manifestations:
Phenomenon 1. The floating ball level gauge in the atmospheric workshop has a large indication
Troubleshooting: Through inspection, it is found that the counterweight of the float ball is at a low point, indicating that the liquid level of the instrument is high. The on-site glass plate and the indicator of the instrument do not match, usually the false liquid level phenomenon of high liquid level caused by the falling off of the instrument float. At this time, it can be dealt with by stopping the maintenance and replacing the floating ball.
Phenomenon 2. The floating ball liquid level gauge in the aromatic hydrocarbon tank area does not change with the liquid level in the container, and always indicates a large value.
Troubleshooting: At this time, you should check whether the floating ball falls off, and if it falls off, reinstall it.
Phenomenon 3. The indication of the float level gauge is low
Troubleshooting: The above faults of the float level gauge may be caused by the falling off of the float, the breakage of the float connecting rod, the damage to the float conversion mechanism, the damage to the float pointer or the meter head, etc. If the instrument conversion mechanism is pressed, the float link rotates flexibly, and the pointer and the meter head are unobstructed, the float link should be replaced at this time.
Phenomenon 4. The float level transmitter suddenly has no indication
Troubleshooting: If the circuit voltage is measured, there is no signal, the polarity of the primary element power supply is not reversed, and the current conversion part has no current output, it means that the meter head is damaged, and the meter head of the float level gauge should be replaced.
Fault 2. Float Type Liquid Level Gauge Interference by magnetic field
If the float level gauge appears to malfunction, according to the analysis of the working principle of the float level gauge, it is mostly due to the interference of the magnetic field. Because the float ball and guide rod of the float level gauge contain magnetic objects, if they are interfered by other magnetic fields in the application environment, it will affect the normal operation of the instrument, and even lead to the appearance of demagnetization of instrument components.
Troubleshooting: Please check whether there is a strong magnetic field around the instrument and the container in time, and confirm that there are no magnetic impurities in the measured liquid. Abnormal.
Fault 3. Float Type Liquid Level Gauge float is stuck
The float is stuck, usually because the liquid to be tested contains impurities and dirt. Over time, the guide rod will gradually become fouled. If the floating ball is stuck, it will cause no signal output from the instrument.
Troubleshooting: If the floating ball is stuck, the instrument personnel should check the status of the floating ball in time, check whether there is scale condensation on the surface of the guide rod, and clean it as soon as possible. Especially for the measured liquid containing impurities, the instrument personnel should clean the instrument guide rod regularly.
Choosing the Right Float Type Liquid Level Gauge for Specific Applications
Selecting the most suitable float type liquid level gauge for a specific application requires careful consideration of several factors. The type of liquid being measured, operating temperature and pressure, tank or vessel size, and environmental conditions all play a significant role in determining the appropriate gauge. For example, in applications where the liquid is corrosive or under high pressure, selecting a gauge with compatible materials and robust construction is essential. Similarly, applications with limited space or visibility may benefit from the use of magnetic float level gauges that offer remote level indication. By thoroughly evaluating these factors, operators can ensure the optimal performance and longevity of the selected float type liquid level gauge.
Installation and Maintenance of Float Type Liquid Level Gauges
Proper installation and regular maintenance are critical for the reliable performance of float type liquid level gauges. During installation, it is important to ensure that the gauge is mounted securely and aligned with the liquid level to provide accurate readings. Any obstructions or interferences that may affect the movement of the float should be addressed to prevent measurement inaccuracies. Routine maintenance activities, such as cleaning the gauge components, inspecting for wear or damage, and calibrating the indicator, should be carried out as per the manufacturer’s guidelines. By adhering to a structured maintenance schedule, operators can prolong the operational life of the gauge and minimize the risk of unexpected failures.
Innovative Applications of Float Type Liquid Level Gauges
The versatility and adaptability of float type liquid level gauges have led to their innovative applications in various industrial sectors. Beyond traditional liquid level monitoring in storage tanks and vessels, these gauges are now being integrated into advanced process control systems, where they play a crucial role in regulating liquid flow, managing inventory, and ensuring the efficiency of production processes. In industries such as pharmaceuticals and biotechnology, float type liquid level gauges are utilized in critical applications where precise liquid level control is essential for maintaining product quality and process integrity. Furthermore, advancements in sensor technologies have enabled the integration of float type gauges with digital monitoring and control systems, enhancing the automation and accuracy of liquid level management.
Conclusion: Enhancing Precision and Safety with Float Type Liquid Level Gauges
In conclusion, float type liquid level gauges are indispensable instruments for achieving precision and safety in industrial operations. Their ability to provide accurate and reliable measurements of liquid levels, coupled with their versatility and adaptability to diverse applications, makes them a cornerstone of liquid level monitoring in various industries. By understanding the working principles, types, advantages, troubleshooting, selection criteria, installation, maintenance, and innovative applications of float type liquid level gauges, operators and decision-makers can make informed choices that contribute to the efficiency, safety, and sustainability of industrial processes. Embracing the capabilities of float type liquid level gauges is not only a strategic investment in operational excellence but also a commitment to ensuring the highest standards of precision and safety in industrial operations.