A differential pressure level gauge is a device used to measure the difference in pressure between two points in a system. It is commonly used to measure the level of liquid or gas in a tank or vessel. The gauge consists of two pressure sensing elements, one placed at the bottom of the tank and the other at the top. The difference in pressure between the two points is then converted into a level measurement.
How do you measure differential pressure?
To measure differential pressure, a differential pressure level gauge is connected to the tank or vessel being monitored. The gauge is equipped with two pressure sensing elements that are placed at different heights in the tank. These sensing elements are connected to the gauge through pressure lines. As the level of the liquid or gas in the tank changes, the pressure at each sensing element also changes. The difference in pressure between the two sensing elements is then measured by the gauge and displayed as a level reading.
There are different types of differential pressure level gauges available, including mechanical, electronic, and digital gauges. Each type has its own advantages and can be used in different applications. Mechanical gauges are simple and reliable, while electronic and digital gauges offer more advanced features such as remote monitoring and data logging.
How does DP level work?
Differential pressure level gauges work based on the principle of hydrostatic pressure. The pressure at the bottom of a liquid or gas column is higher than at the top due to the weight of the column. This pressure difference can be measured and converted into a level reading using a differential pressure level gauge.
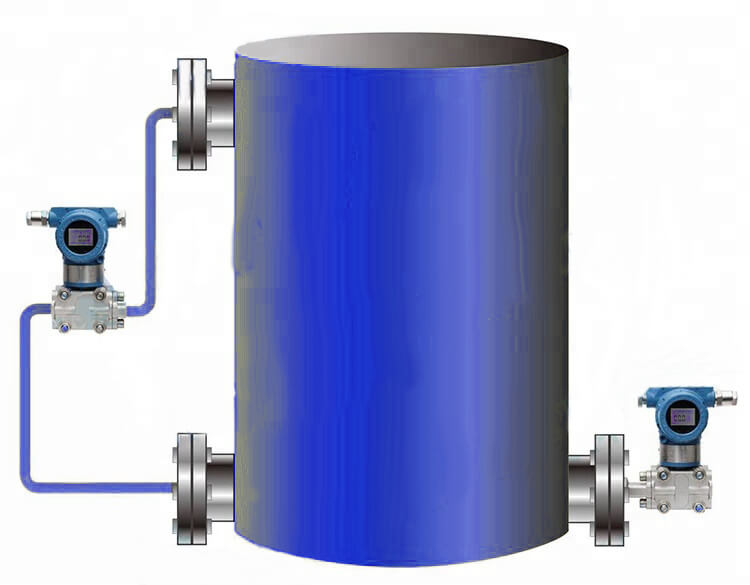
The gauge is equipped with two pressure sensing elements, one placed at the bottom of the tank and the other at the top. These sensing elements are connected to the gauge through pressure lines. As the level of the liquid or gas in the tank changes, the pressure at each sensing element also changes. The difference in pressure between the two sensing elements is then measured by the gauge and displayed as a level reading.
Differential pressure transmitter for level measurement and its drift
The differential pressure liquid level gauge is a device that uses the pressure generated by the liquid column to measure the liquid level height. After the water level changes, the pressure difference measured by the differential pressure transmitter will also change, and there is a linear relationship between them. relation.
When using the differential pressure transmitter to measure the liquid level, due to the different installation positions of the differential pressure transmitter, the positive and negative pressure guide pipes are filled with liquid, which will make the differential pressure transmitter have a fixed differential pressure. When the liquid level is zero, the differential pressure gauge indicates that it is not at zero, but indicates a positive or negative indication deviation. In order to indicate correctness and eliminate this fixed deviation, move the zero point down or up, that is, carry out ‘zero point migration’. This differential pressure value is called the migration amount. If this value is positive, the system is called positive migration; if it is negative, the system is negative migration; if this value is zero, it is no migration.
Drift: Positive migration and negative migration
Usually, when the measurement range after migration is changed to the positive (or large) direction, it is called positive migration, and vice versa. For example: a transmitter with a range of 100 and a measurement range of 0 to 100. After 100% positive migration, the range is still 100, and the measurement range is 100~200; after 100% negative migration, the range is still 100, and the measurement range is -100~0.
The purpose of the transmitter’s positive and negative migration is to eliminate the additional error brought by the transmitter’s usage to the measurement system. For example: when the 3051 differential pressure liquid level gauge is installed far below the measurement position, the liquid column formed by the medium entering the pressure pipe will always give the transmitter a pressure, so that the measurement result of the transmitter becomes the measured value plus The liquid column value, at this time, the transmitter is positively shifted to make the measurement initial value equal to the liquid column value, and this effect can be eliminated.
Another example: when the differential pressure transmitter measures the liquid level, if there is a liquid column in the pressure pipe on the negative pressure side, always give the transmitter a pressure, so that the measurement result of the transmitter becomes the measured value minus the liquid column value. This effect can be eliminated by negatively shifting the transmitter to make the measurement start value equal to the liquid column value.
3051 differential pressure level gauge drift fault maintenance method
- The most commonly used output signal of 3051 differential pressure level gauge is two-wire system 4-20mA. When the 3051 differential pressure level gauge is in the case of serious interference, the frequency output method or mA level output is generally used in the selection of output signals. Methods. In addition, for the 3051 differential pressure level gauge used under special conditions, in addition to considering the factor of the output signal, it is also necessary to install a filter or take special protection measures for the 3151 differential pressure level gauge, so as to improve the 3051 Anti-interference ability of differential pressure level gauge.
- When choosing the 3051 differential pressure level meter, it should be comprehensively considered according to the working environment of the 3051 differential pressure level meter, the contact medium and other conditions. In the process of use, in order to reduce the use of the 3051 differential pressure level meter, it should be regularly used. Check the 3051 differential pressure level gauge and its environmental requirements have not changed.
- For the 3051 differential pressure level gauge, the connection method and distance between it and other equipment will affect the performance of its anti-interference performance, thereby affecting the accuracy of the measurement.
- Many 3051 differential pressure level gauges will appear “drift” when they are used excessively, which means that the stability of the 3051 differential pressure level gauge itself is not very good, so the solution to this method is to initially purchase the 3051 differential pressure level gauge. At this time, it is necessary to comprehensively consider whether all aspects of the 3051 differential pressure level gauge are qualified.
Applications of differential pressure level gauges for differential pressure level measurement
Differential pressure level gauges are widely used in various industries for level measurement of liquids and gases. They are particularly useful in applications where the level of the substance being measured is under high pressure or temperature conditions. Some common applications of differential pressure level gauges include:
- Oil and gas industry: Differential pressure level gauges are used to measure the level of oil, gas, and other fluids in storage tanks, pipelines, and process vessels. They are crucial in maintaining accurate inventory and ensuring safe operation of the equipment.
- Chemical industry: Differential pressure level gauges are used in chemical processing plants to measure the level of corrosive and hazardous liquids. They are designed to withstand aggressive chemicals and high temperatures, providing accurate and reliable level measurements.
- Power generation: Differential pressure level gauges are used in power plants to measure the level of water in boilers and steam drums. Accurate level measurement is essential for the safe and efficient operation of boilers and steam turbines.
- Water and wastewater treatment: Differential pressure level gauges are used in water and wastewater treatment plants to measure the level of liquids in tanks and basins. They help in monitoring and controlling the treatment process, ensuring optimal efficiency and compliance with regulations.
Choosing the right differential pressure level gauge for your needs
When choosing a differential pressure level gauge, there are several factors to consider to ensure it meets your specific needs. These factors include:
- Pressure and temperature range: Determine the maximum pressure and temperature at which the gauge will operate. Ensure that the selected gauge can withstand these conditions without any performance issues.
- Material compatibility: Consider the type of liquid or gas being measured and select a gauge that is compatible with the material. Different materials have different resistance to corrosion and chemical attack, so choose the one that suits your application.
- Accuracy requirements: Determine the level of accuracy required for your application. Some gauges offer higher accuracy than others, but they may come at a higher cost. Consider the trade-off between accuracy and cost to find the right balance.
- Environmental conditions: Consider the environmental conditions in which the gauge will be installed. Factors such as vibration, humidity, and exposure to harsh elements can affect the performance and lifespan of the gauge. Choose a gauge that is designed to withstand these conditions.
- Maintenance and calibration: Consider the ease of maintenance and calibration of the gauge. Some gauges require regular calibration and adjustment to maintain accuracy. Choose a gauge that is easy to maintain and calibrate to minimize downtime and ensure accurate measurements.
Conclusion: The importance of understanding and using differential pressure level gauges
Differential pressure level gauges are essential tools for accurate and reliable level measurement in various industries. They provide vital information for process control, inventory management, and safety. Understanding how differential pressure level gauges work and choosing the right gauge for your needs is crucial to ensure accurate measurements and efficient operation of your system.
Whether you are in the oil and gas industry, chemical processing, power generation, or water treatment, a differential pressure level gauge can greatly enhance your level measurement capabilities. By considering the factors mentioned above and selecting a gauge that meets your specific requirements, you can ensure accurate and reliable level measurements, leading to improved process efficiency and safety.
So, next time you are in need of level measurement, consider the benefits of using a differential pressure level gauge and make an informed choice.