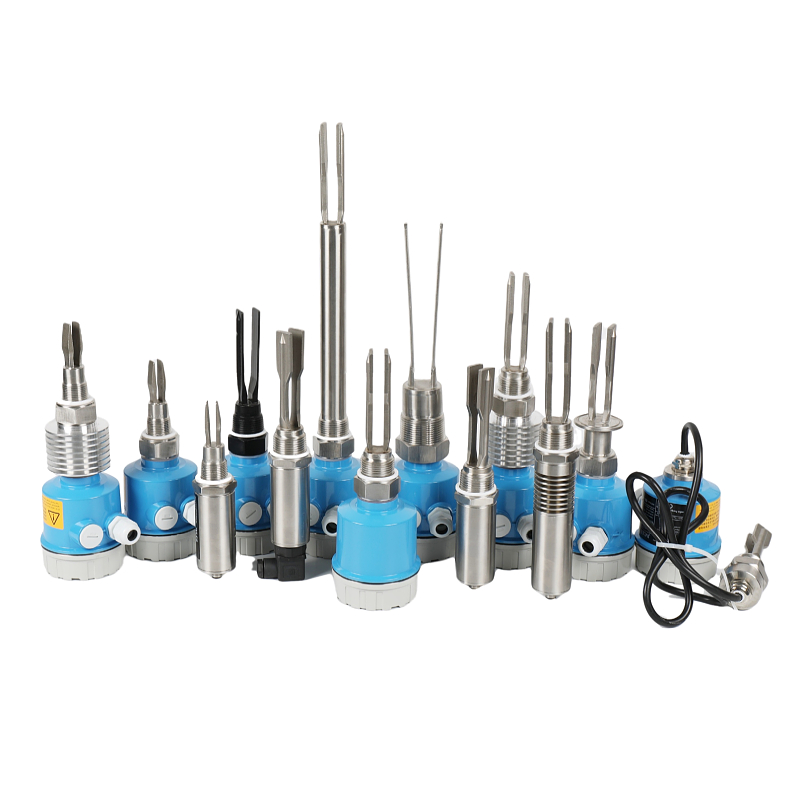
- Tel: +86 28 87436908
- Email: info@cdsentec.com
Chemical process instrumentation refers to the devices and equipment used to monitor and control various parameters in chemical processes. These instruments play a crucial role in ensuring the efficiency, safety, and quality of chemical processes.
Distillation is a widely used chemical industry process that involves the separation of a mixture of liquids based on their different boiling points.
The process temperatures in a distillation column place high demands on the measurement technologies deployed. The boiling point of the distillate frequently exceeds 400 °C. The aim is to achieve the highest possible product throughput for cost-effective operation of the plant. This means the raw material replenishments need to be optimally controlled by level and process pressure measurement in the column.
In the preflash drum, the medium is heated before it is fed into the distillation column. Accurate and reliable level control is a critical factor in ensuring efficient operation of the distillation column. Reliable measurement of the level prevents overfilling of the vessel and also keeps the pumps from running dry.
Accurate level control of the distillation unit ensures product quality of the hydrocarbon at the different cuts, but this is made difficult due to hot liquids flashing, buildup and high temperature. Even through process changes reliable level measurement and point level detection are required.
Evaporators are heat exchangers that are deployed at the bottom of distillation columns. In the evaporator, the residue is boiled up from the sump and fed back into the distillation process. Precise control of the level in the evaporator ensures efficient operation of the plant. A reliable measurement also ensures that the heating coils are always covered with liquid, to prevent any overheating incidents.
Chemical distillation process instrumentation refers to the devices and equipment used to monitor and control various parameters in the distillation process. These instruments play a crucial role in ensuring the efficiency, safety, and quality of the distillation process.
Chemical reaction processes refer to the series of chemical transformations that occur when two or more substances interact to form new substances.
Changing media, as well as process pressures and temperatures, characterize the typical reaction processes in a reaction vessel. This is a big engineering challenge, because any sensors used to control the process need to deliver reliable measurements under these conditions. To meet the diverse conditions found in reaction vessels, level measurement and point level detection instrumentation must cover a broad spectrum of applications.
Storage and surge tanks provide a reliable supply of materials for various ongoing processes. Plant operators need accurate data on levels, densities, etc. of these tanks at all times to ensure timely replenishment and monitor production.
In the ammonia reactor, nitrogen reacts with hydrogen to form ammonia. The temperature in the reactor can be anywhere up to 500 °C at pressures of 200 bar. To monitor the system pressure, the measurement itself does not take place in the interior of the reactor, but in the cooler inlet pipe of the reactor.
Chemical reaction process instrumentation refers to the devices and equipment used to monitor and control various parameters like temperature, pressure, and flow rate in chemical reaction processes. These instruments help maintain optimal conditions, ensure safety, and improve product yields.
Chemical dyes are colored compounds that are used to impart color to various materials such as textiles, paper, leather, and more
In the dye production process, the intermediates need to be dissolved in the dissolving tank first. The dye intermediate used is mainly naphthol, and the solvent is water and sodium hydroxide. The container is equipped with a stirring paddle to ensure that the added raw materials are evenly mixed. Level gauges transmit reliable measured values to the control system.
What happens in the coupling reactor is the core reaction of dye production, that is, the coupling reaction, through which azo dyes (synthetic dyes) are produced and processed into pigments of various colors in the subsequent process. The stirring device in the reactor is used for continuous mixing of the azo dyes. In addition, the process needs to be cooled with ice, otherwise the various substances in the reaction will decompose. Level measurement is critical to the stable operation of this process.
The wet paint is heated on a drying conveyor. At the end of the conveyor belt, the dry and rough paint is fed into a silo. Control the conveyor belt by measuring the fill level in the silo.
The finished dye is put into the hopper of the packaging machine by pneumatic conveying in the last step of the process. The dye powder available for sale in the hopper will be filled into the packaging bag through the lower discharge port. In order to control the discharge process, the level in the hopper needs to be continuously measured. In addition, the limit alarm is used as a safety switch to prevent material overflow.
Chemical dye process instrumentation refers to the use of devices and equipment to monitor and control various parameters during the dyeing process. These instruments play a crucial role in maintaining optimal conditions, ensuring safety, and improving product yields in the dyeing industry.
Chemical storage in laboratory settings involves adhering to legal requirements and recommended practices to ensure safety and minimize risks
Reliable warehousing is not only the basis for safe production, but also helps factories avoid the impact of raw material shortages and price fluctuations. For large storage tanks, in addition to the explosion-proof requirements for level measurement, regulations for overfill protection or SIS safety instrumented systems are often also complied with.
Low-viscosity solvents are able to penetrate many types of plastics, placing higher demands on liquid level measurement technology. To prevent overflow and monitor solvent delivery, process instrumentation increases equipment safety and protects people and the environment.
In the chemical industry, various solids are produced or used as raw materials. Reliable level measurement in silos requires consideration of many factors: different solids densities, abrasive media, heavy dust and explosion protection requirements. Choosing the right level instrument can realize efficient planning of production and ensure reliable transportation of finished products.
Propane is a liquefied petroleum gas (LPG), a colorless, odorless, flammable gas that can be extracted from natural gas or produced by refining crude oil. Propane needs to be stored in high-pressure containers after compression and liquefaction to avoid re-gasification. Reliable level measurement is critical for stable storage.
Chemical storage process instrumentation involves the use of various tools and equipment to ensure the safe and efficient storage of chemicals. By utilizing appropriate process instrumentation, factories can effectively manage and maintain the safety of their chemical storage areas.
SenTec online resource library is a place you can know more knowledge from video, cases study, e-book etc.