Introduction to Industry 4.0
Welcome to a new era in industrial production, commonly referred to as Industry 4.0. This term describes the ongoing automation of traditional manufacturing and industrial practices, leveraging modern smart technology. Large-scale machine-to-machine communication (M2M) and the internet of things (IoT) are integrated for increased automation, improved communication, and self-monitoring, as well as the production of smart machines capable of analyzing and diagnosing issues without the need for human intervention.
Industry 4.0 represents the fourth industrial revolution, an age marked by a fusion of technologies that blur the lines between the physical, digital, and biological spheres. It is characterized by the advent of cyber-physical systems, the internet of things, cloud computing, and cognitive computing. It is a complex and multifaceted phenomenon, with effects that are seen in many industrial sectors and areas of life.
The transformative power of Industry 4.0 arises from its potential to reshape industries and redefine the boundaries of industrial production. Its central principle is that by connecting machines, systems, and assets, businesses can create intelligent networks along the entire value chain that can control each other autonomously. This connectivity allows for a manufacturing system that is not only interconnected but also capable of autonomous decision-making.
Understanding Smart Sensors
Smart sensors play a critical role in the realization of Industry 4.0. These sensors are sophisticated devices that process data at the sensing level to output fully processed, multi-parameter information. They are designed to respond to physical inputs such as light, heat, motion, moisture, pressure, or any other entity, and convert it into a signal which can be read by an instrument or the user.
Smart sensors are integral to Industry 4.0, as they are the primary data collection points in the IoT network. They provide the raw data that is used by control systems to make decisions. Smart sensors can monitor machine performance, environmental conditions, and even the presence of people and objects, among many other things.
These sensors are often equipped with additional functionality, like wireless communication and on-board analytics, which enhance their usefulness and versatility. They can be used to monitor complex systems in real time, enabling preventative maintenance and minimizing downtime.
The Role of IoT in Industry 4.0
The Internet of Things (IoT) is a network of interconnected devices that collect and exchange data. In the context of Industry 4.0, IoT plays a crucial role in driving efficiency, scalability, and flexibility in industrial operations. It enables the seamless integration of physical and digital worlds, creating a more interconnected and responsive industrial environment.
IoT devices, including smart sensors, collect vast amounts of data from different points in the industrial process. This data is then analyzed and used to optimize operations, predict failures, and initiate corrective actions. The use of IoT in Industry 4.0 is not limited to manufacturing processes alone. It also plays a significant role in other areas such as inventory management, quality control, and supply chain optimization.
Furthermore, IoT brings about a level of interconnectivity that allows machines to communicate with each other and with human operators. This gives rise to industrial systems that can autonomously react to unexpected changes in production, or identify inefficiencies and re-optimize production processes in real time.
The Impact of Smart Sensors in Industry 4.0
Smart sensors have a profound impact on Industry 4.0. They serve as the eyes and ears of the factory, collecting vital data that drives more informed decision-making. By integrating smart sensors into industrial systems, businesses can achieve a higher level of automation and efficiency.
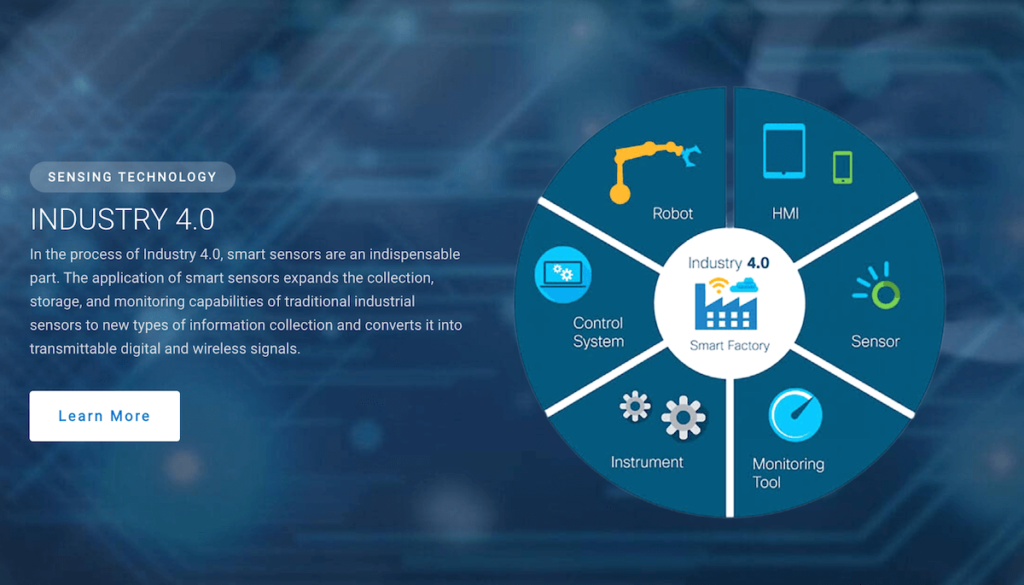
Smart sensors enable a range of new capabilities in Industry 4.0. For example, predictive maintenance becomes possible through sensors that monitor the condition of machinery and predict failures before they occur. This leads to significant cost savings, as businesses can avoid expensive equipment breakdowns and unplanned downtime.
In addition, smart sensors can be used to monitor the quality of products in real-time during the manufacturing process. This allows for immediate adjustments to be made if quality standards are not being met, reducing waste and improving overall product quality.
The Role of IoT Sensors Manufacturers in Industry 4.0
IoT sensors manufacturers play a pivotal role in the transition towards Industry 4.0. They are responsible for producing the smart sensors that power the IoT, and by extension, Industry 4.0. These manufacturers not only produce sensors, but they also develop the software and provide industrial IOT solutions that allow these sensors to process and interpret the data they collect.
Manufacturers of IoT sensors are constantly innovating to produce more advanced sensors that can collect more data, process it more quickly, and do so in a more energy-efficient manner. These advancements are critical to the continued growth and development of Industry 4.0.
In addition to producing the sensors themselves, IoT sensors manufacturers also play a role in shaping the standards and protocols for sensor communication. This involves working with other stakeholders to ensure that sensors can communicate effectively with each other and with other devices in the IoT network.
Internet of Things and Digital and Wireless Signals in Industry 4.0
The use of digital and wireless signals in Industry 4.0 is a game changer. These technologies enable the seamless communication and data transfer between devices in the industrial IoT network. Digital and wireless signals allow for real-time data collection and analysis, enabling immediate adjustments to be made to industrial processes.
Digital signals, unlike their analog counterparts, can maintain their integrity over long distances, ensuring that the data collected is accurate and reliable. Furthermore, digital signals can be encrypted, enhancing the security of the data being transferred.
Wireless technology, on the other hand, eliminates the need for physical connections between devices. This not only reduces the complexity and cost of installing and maintaining wired networks, but also allows for more flexibility in the positioning of devices.
The Transformation of Industrial Landscape through Industry 4.0 and Smart Sensors
Industry 4.0 and smart sensors are transforming the industrial landscape in many ways. The integration of these technologies into the manufacturing process has resulted in significant improvements in efficiency, productivity, and quality.
Industry 4.0 technologies enable the creation of “smart factories”, where machinery and equipment can improve processes through automation and self-optimization. The benefits of this include improved quality, reduced waste, and increased production speed.
Smart sensors, on the other hand, provide the data necessary for these improvements. They monitor various aspects of the manufacturing process, collecting data that is used to optimize operations, predict equipment failures, and ensure product quality.
Future Prospects of Industry 4.0 and Smart Sensors
The future prospects of Industry 4.0 and smart sensors are vast. As these technologies continue to evolve, they are expected to drive further improvements in industrial operations.
One area of potential growth is in the use of artificial intelligence (AI) and machine learning in Industry 4.0. These technologies can be used to analyze the data collected by smart sensors, making predictions and decisions that further optimize industrial processes.
Another promising area is the development of more advanced and versatile smart sensors. Future sensors could be capable of detecting a wider range of parameters, processing data more quickly, and operating with greater energy efficiency. These advancements could enable new applications and further improve the efficiency and effectiveness of industrial operations.
Challenges and Solutions in Implementing Industry 4.0 and Smart Sensors
Despite the many benefits of Industry 4.0 and smart sensors, there are also challenges that must be overcome in their implementation. These include technological challenges, such as the need for high-speed, reliable internet connectivity and the integration of legacy systems with new technologies.
There are also organizational challenges, such as the need for new skills and the management of change within the organization. In addition, there are regulatory and security issues to consider, as the increased connectivity and use of data in Industry 4.0 can raise concerns about data privacy and cyber security.
However, these challenges can be overcome with careful planning and the right approach. This includes investing in the necessary infrastructure, training staff, and establishing clear policies and procedures for data management and security.
Conclusion: The Future of Industrial Landscape with Industry 4.0 and Smart Sensors
In conclusion, Industry 4.0 and smart sensors are at the heart of the transformation that is reshaping the industrial landscape. They are driving significant improvements in efficiency, productivity, and quality, while opening up new opportunities for innovation.
While there are challenges to be overcome in the transition to Industry 4.0, the benefits are clear. Businesses that embrace these technologies can expect to gain a competitive edge, as they are able to produce higher quality products, more efficiently, and at a lower cost.
The future of the industrial landscape is one that is interconnected, intelligent, and highly efficient. And at the heart of this future are Industry 4.0 and smart sensors.