Differential pressure liquid level gauge is also called differential pressure low position liquid level gauge. Differential pressure level gauge is a reliable measurement method that avoids the direct contact of the measured medium with the isolation diaphragm of the transmitter.
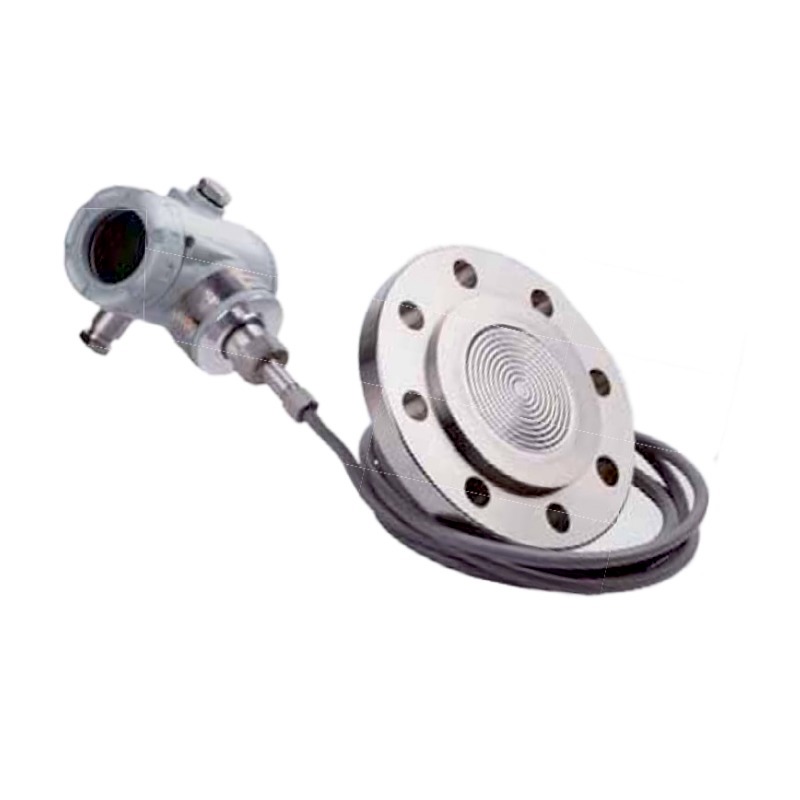
When you need a differential pressure liquid level gauge?
Differential Pressure Liquid Level Gauge is suitable for the following situations:
1. When the measured medium has a corrosive effect on the transmitter connector and sensitive components;
2. When the high temperature measured medium needs to be isolated from the transmitter;
3. When there is solid suspended matter or high viscosity in the measured medium, it is easy to block the transmitter joint and pressure chamber;
4. When the measured medium is easy to solidify or crystallize when it is drawn out by a pressure tube;
5. When replacing the measured medium, it is necessary to rinse and not mix;
6. Sanitary conditions must be maintained to prevent contamination.
The differential pressure liquid level gauge low-level liquid level measurement transmitter adopts advanced micro-processing intelligent control, which is suitable for displaying and controlling various physical quantities and detection signals such as temperature, humidity, pressure, liquid level, instantaneous flow, speed, etc. Perform high-accuracy linear correction measurements on a variety of nonlinear input signals. However, in the measurement process, due to the influence of various factors, the low-level liquid level measurement transmitter system of differential pressure type liquid level gauge sometimes has various failures, which affects the measurement of the system.
What are the common faults of the differential pressure liquid level gauge ?
(1) If the indication value of the low-level liquid level measurement transmitter system of the differential pressure liquid level gauge becomes the maximum or minimum, first check whether the instrument is normal. If the indication is normal, change the liquid level control to manual remote control, and you can see the liquid level change. If the liquid level can stabilize within a certain range, the liquid level control system is faulty. If the liquid level is unstable, it is usually a fault caused by the process system, and the cause should be found from the process.
(2) If the low-level liquid level measurement transmitter and the on-site direct reading indicator of the differential pressure type differential pressure liquid level gauge are incorrectly indicated, first check whether the on-site direct reading indicator is normal; if the indication is normal, check the differential pressure liquid level indicator. Check whether the sealing fluid of the negative pressure conduit of the level gauge leaks; if there is leakage, refill the sealing fluid and adjust the zero leakage.
(3) When the indication value of the low-level liquid level measurement transmitter system of the differential pressure liquid level gauge changes frequently, the capacity of the liquid level control object should be analyzed first, and the cause of the failure should be analyzed. Large capacity is generally the cause of instrument failure. If the capacity is small, it is necessary to analyze whether the operating state of the technology has changed. Technological changes, if any, are likely to be frequent. No change may be the cause of instrument failure.