Pressure transmitter calibration is a critical process that ensures accurate pressure measurements in various industrial applications. Whether it is monitoring pressure in a manufacturing plant or controlling pressure in a chemical process, precise measurements are vital for maintaining efficiency and safety. In this article, we will explore the importance of accurate pressure measurements and delve into the step-by-step approach to pressure transmitter calibration.
Importance of accurate pressure measurements
Accurate pressure measurements play a crucial role in numerous industries, including oil and gas, pharmaceuticals, and food processing. These measurements provide valuable information for process control, equipment performance, and safety. For example, in a refinery, precise pressure readings are essential for maintaining optimal operating conditions and preventing accidents. In the medical field, accurate pressure measurements are vital for monitoring patients’ blood pressure and ensuring proper diagnosis and treatment. Without reliable pressure measurements, industries would face significant challenges in maintaining efficiency, quality, and safety standards.
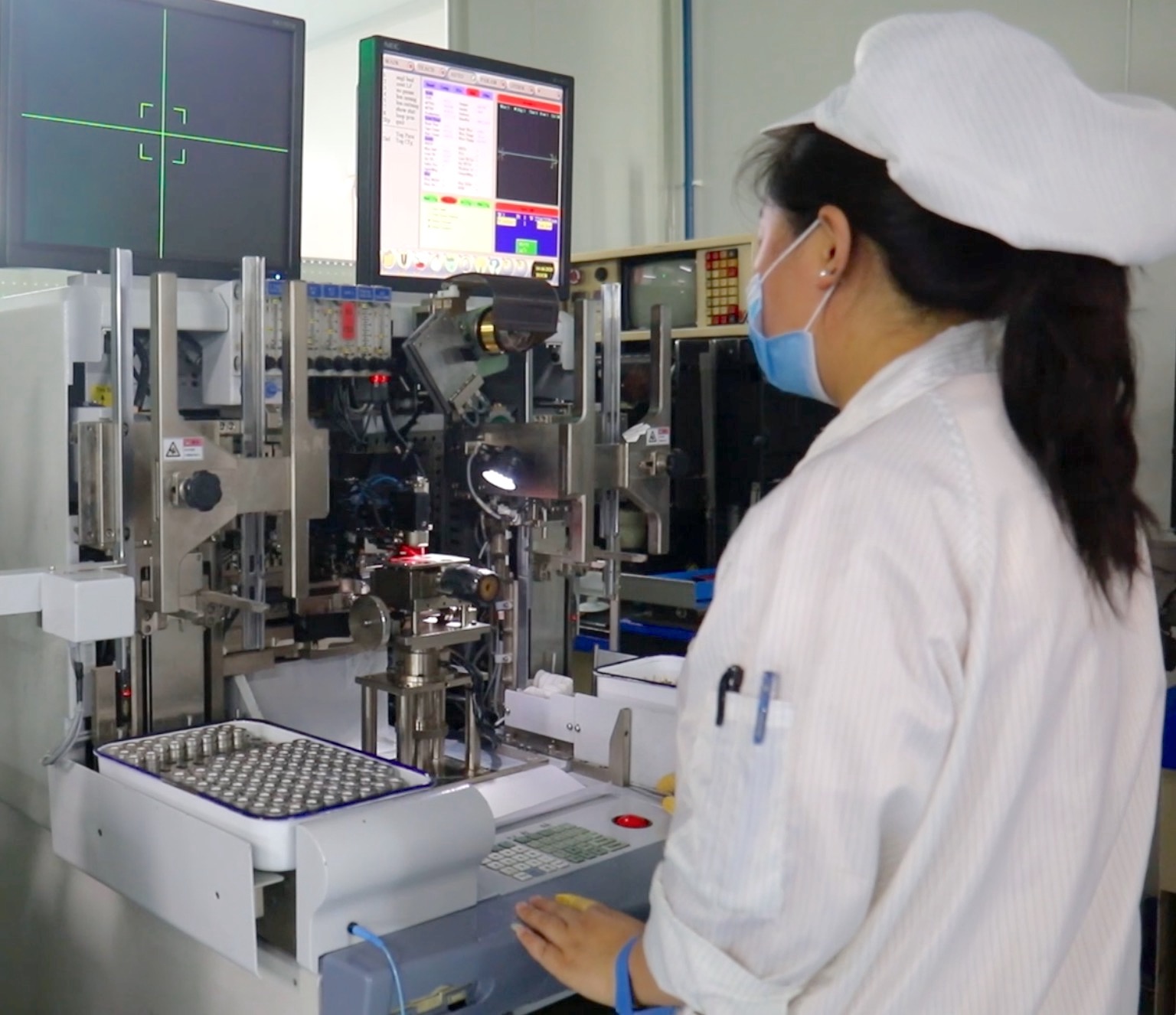
Understanding pressure transmitters and their calibration process
Before diving into the calibration process, it is essential to understand the basics of pressure transmitters. A pressure transmitter is a device that converts the physical pressure applied to it into an electrical signal. This signal is then transmitted to a control system or data acquisition device for further analysis and control. Pressure transmitters consist of various components, including a sensing element, an electronic circuit, and a communication interface.
The calibration process involves comparing the output of the pressure transmitter with a reference standard to ensure accuracy. This is typically done by applying known pressure values to the transmitter and comparing the measured output with the expected values. Calibration can be performed using different methods, such as static or dynamic calibration. Static calibration involves applying a constant pressure, while dynamic calibration involves applying varying pressures to simulate real-world conditions. The choice of calibration method depends on the specific application and accuracy requirements.
Tools and equipment required for pressure transmitter calibration
To perform pressure transmitter calibration, several tools and equipment are necessary. Here is a list of the essential items:
- Pressure source: A reliable pressure source capable of generating the desired pressure range with sufficient accuracy.
- Reference standard: A calibrated reference standard that provides accurate pressure values for comparison.
- Multimeter: A digital multimeter capable of measuring voltage and current for verifying the output signal of the pressure transmitter.
- Calibration software: Optional software for automated data acquisition, analysis, and documentation of the calibration process.
- Connecting cables: Suitable cables for connecting the pressure transmitter to the pressure source and other measurement devices.
- Sealing materials: Various sealing materials, such as Teflon tape or sealant, to ensure leak-free connections.
- Calibration certificates: Calibration certificates for the reference standard and any other equipment used in the calibration process.
Step-by-step guide to pressure transmitter calibration
- Gather necessary equipment: Start by gathering all the tools and equipment required for the calibration process. This may include a pressure source, a reference standard, a multimeter, a calibration software, and appropriate connecting cables.
- Prepare the pressure source: Set up the pressure source according to the specifications of the pressure transmitter. Ensure that the pressure source is capable of generating the desired pressure range with sufficient accuracy.
- Connect the pressure transmitter: Connect the pressure transmitter to the pressure source using suitable connecting cables. Ensure that the connections are secure and free from any leaks.
- Configure the calibration software: If using calibration software, configure it to communicate with the pressure transmitter and record the calibration data. Follow the software instructions for setting up the calibration parameters, such as pressure range and measurement intervals.
- Perform zero calibration: Start the calibration process by performing a zero calibration. This involves applying zero pressure to the transmitter and adjusting the zero point to eliminate any offset or bias.
- Perform span calibration: After the zero calibration, apply a known pressure to the transmitter within its operating range. Record the output signal and compare it with the expected value. Adjust the span calibration to minimize any errors and ensure accurate readings throughout the pressure range.
- Verify calibration: Once the calibration process is complete, verify the accuracy of the pressure transmitter by applying different pressures and comparing the measured values with the expected values. This will help identify any remaining errors or drifts in the calibration.
- Document the calibration results: Record all the calibration data, including the pressure values, measured output, and any adjustments made during calibration. This documentation is essential for traceability and future reference.
Pressure Transmitter Calibration methods
One-point pressure transmitter calibration method
This one-point calibration method can compensate the offset error by eliminating the drift at the zero point of the transfer function. This type of calibration method is usually called automatic zeroing. Offset calibration is usually performed at zero pressure, especially in differential transmitter, because the differential pressure is usually zero under nominal conditions.
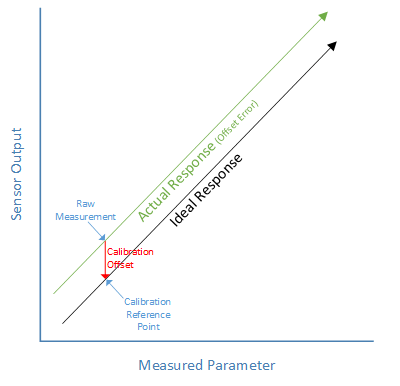
Select the calibration pressure
The selection of the calibration pressure determines the pressure range to obtain better accuracy. The calibration point must be selected according to the target pressure range, and the pressure range may not be consistent with the working range. The sensitivity calibration is usually performed by a single-point calibration method in the mathematical model.
Three-point calibration method
Linear error usually has a consistent form. It can be obtained by calculating the average linear error of a typical example and determining the parameters of the polynomial function (a×2+bx+c). The models obtained after determining a, b, and c are all valid for the same type of sensor. This method can effectively compensate the linearity error without the third calibration point.
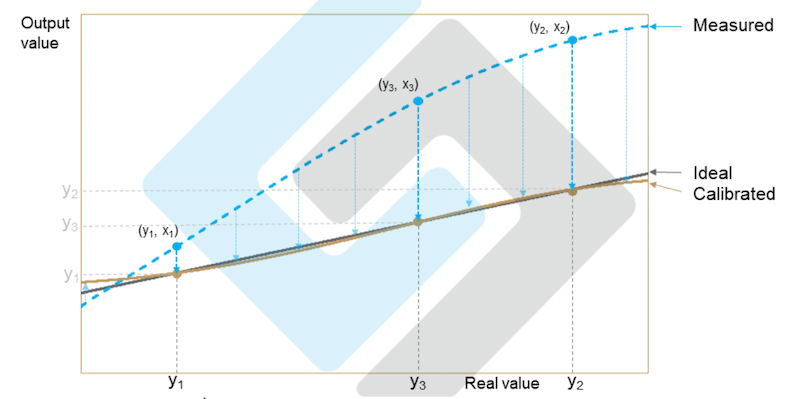
Common challenges in pressure transmitter calibration and how to overcome them
While pressure transmitter calibration is a straightforward process, it can present some challenges. Here are a few common challenges and tips to overcome them:
- Leakage: Ensure that all connections are tight and free from leaks. Use appropriate sealing materials if necessary.
- Environmental factors: Take into account environmental factors, such as temperature and humidity, which can affect the calibration process. Perform the calibration in a controlled environment whenever possible.
- Pressure source accuracy: Use a reliable and accurate pressure source to ensure precise calibration. Regularly verify the accuracy of the pressure source using traceable standards.
- Electrical interference: Minimize electrical interference by keeping the calibration setup away from sources of electromagnetic interference. Shielding the cables and using grounded connections can also help reduce interference.
- Measurement uncertainty: Understand the concept of measurement uncertainty and consider its impact on the calibration results. Make sure to calculate and report the uncertainty associated with the calibration.
Best practices for ensuring precise measurements during calibration
To achieve accurate pressure measurements during calibration, it is important to follow best practices. Here are some tips to ensure precise measurements:
- Allow sufficient stabilization time: Give the pressure transmitter and other equipment enough time to stabilize before starting the calibration. This helps minimize errors caused by temperature changes and other transient effects.
- Perform multiple calibration runs: To increase confidence in the calibration results, perform multiple calibration runs and calculate the average values. This helps mitigate any random errors or fluctuations.
- Follow proper handling procedures: Handle the pressure transmitter and other equipment with care to prevent damage or misalignment. Ensure that the pressure source is properly calibrated and maintained.
- Regularly calibrate the reference standard: The accuracy of the reference standard deteriorates over time. Regularly calibrate the reference standard using a traceable calibration service to ensure reliable calibration results.
- Maintain a calibration schedule: Develop a calibration schedule based on the manufacturer’s recommendations and industry standards. Regularly calibrate the pressure transmitters to maintain accuracy and prevent drift.
Benefits of regular pressure transmitter calibration
Regular calibration of pressure transmitters offers several benefits:
- Accuracy: Calibration ensures that pressure measurements are accurate, providing reliable data for process control and equipment performance evaluation.
- Safety: Accurate pressure measurements are crucial for maintaining safe operating conditions and preventing accidents in various industries.
- Compliance: Many industries have regulatory requirements for calibration. Regular calibration ensures compliance with these standards, avoiding potential penalties or legal issues.
- Efficiency: Precise pressure measurements help optimize process efficiency, reducing energy consumption and improving overall productivity.
- Longevity: Proper calibration and maintenance can extend the lifespan of pressure transmitters, reducing the need for frequent replacements and associated costs.
Common mistakes to avoid during pressure transmitter calibration
To ensure accurate pressure measurements, it is important to avoid common mistakes during the calibration process. Here are a few mistakes to watch out for:
- Skipping zero calibration: Neglecting the zero calibration can introduce significant errors in pressure measurements. Always perform the zero calibration before the span calibration.
- Neglecting environmental factors: Environmental factors, such as temperature and humidity, can affect the calibration process. Take these factors into account and perform the calibration in a controlled environment whenever possible.
- Using an inaccurate pressure source: Using an inaccurate pressure source can lead to incorrect calibration results. Regularly verify the accuracy of the pressure source using traceable standards.
- Neglecting measurement uncertainty: Measurement uncertainty is an inherent part of any calibration process. Ignoring measurement uncertainty can lead to misleading calibration results. Always calculate and report the uncertainty associated with the calibration.
- Lack of documentation: Failing to document the calibration process and results can lead to traceability issues and make it difficult to troubleshoot any problems. Keep thorough records of all calibration activities.
Conclusion: How pressure transmitter calibration ensures accurate measurements
Pressure transmitter calibration is a crucial process for achieving accurate pressure measurements in various industrial applications. Accurate pressure measurements are essential for maintaining efficiency, safety, and regulatory compliance. By following a step-by-step approach to pressure transmitter calibration and adhering to best practices, industries can ensure precise measurements and reap the benefits of improved process control, safety, and efficiency. Regular calibration, accompanied by proper documentation and avoidance of common mistakes, guarantees accurate measurements and extends the lifespan of pressure transmitters. So, invest in pressure transmitter calibration to achieve reliable and precise pressure measurements.