Introduction to Mass Flow Meter Measurements
Mass flow meters are essential devices used in various industries to measure the flow rate of fluids, gases, or solids. Understanding the mass flow meter working principle and accurate measurements are crucial for ensuring efficient operations and maintaining quality standards. This article explores the working principle of mass flow meters and the importance of accuracy in their measurements.
Understanding the Mass Flow Meter working principle
Mass flow meters operate on the principle of measuring the mass of a substance passing through a given point per unit time. They utilize various technologies such as thermal, coriolis, ultrasonic, or vortex to achieve accurate measurements. Among these, the coriolis mass flow meter is widely used for its high accuracy and reliability.
Importance of Accuracy in Mass Flow Meter Measurements
Accurate mass flow meter measurements are essential for several reasons. Firstly, they ensure the proper allocation of resources and facilitate efficient process control. Accurate measurements also enable the detection of leaks, losses, or inefficiencies in the system. Moreover, they are vital for maintaining quality standards and complying with regulatory requirements. Therefore, achieving accuracy in mass flow meter measurements is of utmost importance.
Factors Affecting the Accuracy of Mass Flow Meters
There are many factors that affect the measurement accuracy of the mass flow meter, such as the basic error of the instrument, zero point stability, repeatability error, etc. These errors can be corrected from the design and manufacture of the mass flowmeter. In addition, certain errors will also occur during the installation and use of the mass flowmeter, such as excessive process temperature, process pressure much higher than the calibration pressure or strong mechanical vibration in the surrounding environment, etc., which will affect the measurement accuracy of the mass flowmeter.
Introduction to Coriolis Mass Flow Meters
Coriolis mass flow meters are widely used in various industries due to their high accuracy and versatility. They operate based on the Coriolis effect, which causes a tube to twist when a fluid flows through it. This twisting motion is directly proportional to the mass flow rate, allowing for accurate measurements.
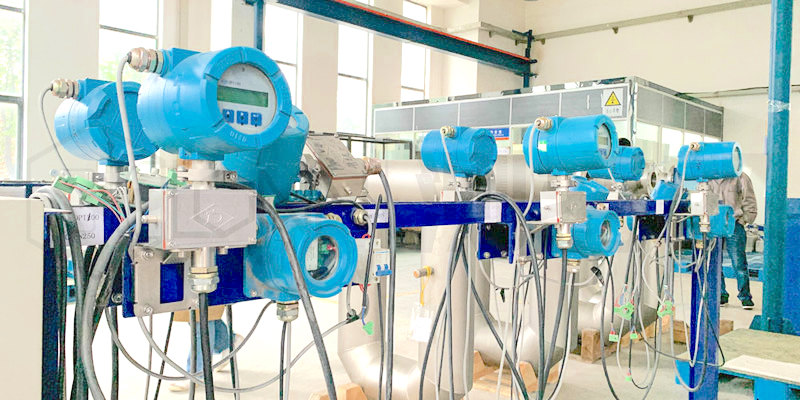
Understanding the Working Principle of Coriolis Mass Flow Meters
Coriolis mass flow meters consist of a vibrating tube through which the fluid flows. When the fluid enters the tube, it causes a phase shift in the vibration, which is measured by sensors. By analyzing this phase shift, the mass flow rate can be determined accurately. The unique working principle of coriolis mass flow meters makes them highly accurate and suitable for a wide range of applications.
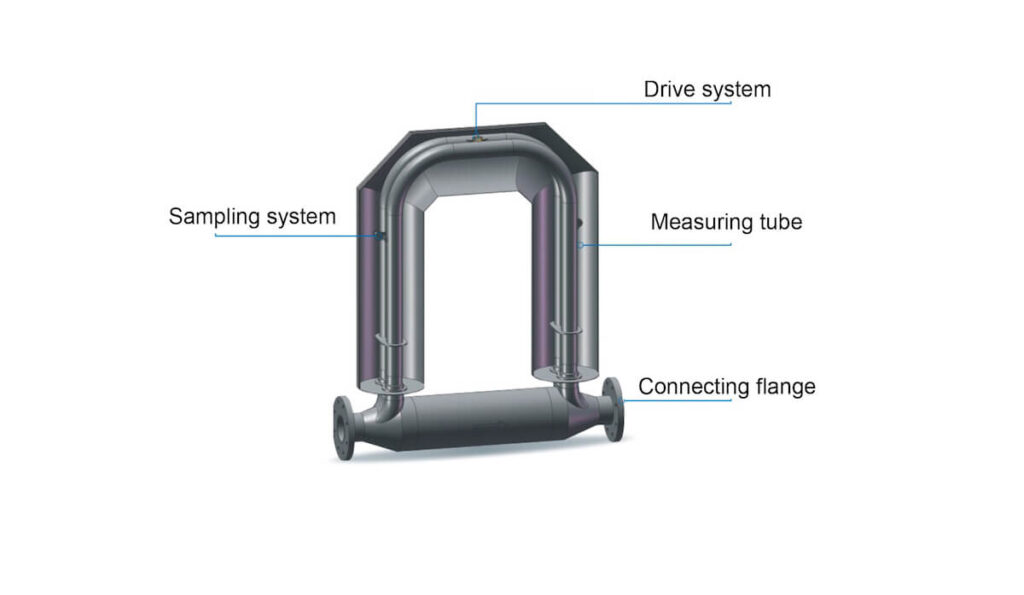
The Measurement Accuracy Affecting factors of Mass Flow Meter
1. The influence and correction of mechanical vibration
We know from the working principle of the mass flowmeter that it is an instrument that measures based on the principle of vibration, and it vibrates at its own frequency. The fluid flowing through the flow tube causes the measurement tube to twist, and the degree of twist is proportional to the amount of mass flow. The resonant wave generated by the external mechanical vibration will inevitably interfere with the instrument’s own vibration amplitude and frequency, affect the measurement accuracy, and even damage the instrument in severe cases. In order to eliminate the impact of mechanical vibration on the accuracy of the instrument, we should pay attention to installation and maintenance.
First of all, the installation location should be selected as far as possible in a place without mechanical vibration, away from vibration sources such as pump room and unit. Try to avoid installing two or more sensors on the same pipeline, because the vibration of the measuring tube will affect each mass flowmeter, causing interference and causing abnormal vibration and affecting the work of the instrument.
Secondly, it is necessary to standardize the installation of the instrument. Stress-free installation is adopted. During installation, the straight pipe is directly fixed on the support frame first, the connecting piece of the flowmeter is installed, the straight pipe is cut according to the required length, and the flowmeter is welded and hoisted without pressure; Flanges are properly aligned, coaxial to reduce stress, and fixed supports are provided to avoid instrument oscillation on long pipelines. However, the support frame should be installed on the pipeline outside the flanges at both ends of the instrument, otherwise, if it is directly supported on the instrument itself, it will affect its free oscillation, and the phase difference generated during oscillation will deviate, thus affecting the measurement results, especially for large-diameter flow. meter, because of its large vibration amplitude, the consequences are more serious.
When it is unavoidable that the sensors are used in series in the same pipeline, the manufacturer should propose to the manufacturer to stagger the resonant frequency value close to the instrument, or to widen the installation distance of the sensor, and set up independent support brackets respectively.
When there is a valve or pump on the process line near the sensor, it needs its own support and cannot be supported by the sensor’s mounting base or the process connection. For shorter or weaker vibrations, it can be corrected by increasing the damping coefficient. The damping coefficient can be modified through the 275 communicator, generally set to 5~30 seconds.
2. Influence of process temperature and correction
The change of process temperature will cause the change of the volume of the medium, but it will not affect the measurement result, because the mass is always conserved no matter how the temperature changes. However, the change of temperature will affect the rigidity and zero point stability of the measuring tube, thus affecting the measurement accuracy of the mass flowmeter. The change of temperature on the stiffness of the measuring tube is that when the temperature rises, the material of the measuring tube will become soft, and vice versa, and the amount of distortion generated by the Coriolis force will also be affected. But flow tube rigidity is repeatable and repairable. Generally, an RTD temperature sensor is installed in the sensor of the mass flowmeter, which can measure and compensate the temperature. Such as Emerson’s mass flowmeter, the change of the rigidity of the measuring tube with temperature can be corrected by the temperature coefficient T.
However, the effect of temperature change on zero stability will create an additional error that is non-repeatable. This is due to an imbalance in the material and geometry of the sensor. The zero point instability of the sensor is due to the large deviation that may occur when the medium temperature is inconsistent with the zero adjustment temperature, which is expressed as the percentage of flow change when the medium temperature changes by 1°C from the zero adjustment temperature. When the process temperature is quite different from the zero temperature, the error will be more significant.
Therefore, in order to reduce the influence of temperature on the zero point stability, the instrument can be adjusted to zero at the process temperature.
Accuracy Correction Techniques for Mass Flow Meters
To achieve and maintain accuracy in mass flow meter measurements, various correction techniques can be employed. One commonly used method is calibration, where the mass flow meter is compared against a reference standard. This helps identify any deviations or errors and allows for adjustments to be made. Another technique is temperature compensation, which accounts for the effect of temperature on the fluid properties. Additionally, advanced signal processing algorithms can be utilized to correct for any inherent limitations or nonlinearities in the measurement system.
Common Challenges in Achieving Accuracy in Mass Flow Meter Measurements
Despite the advancements in mass flow meter technology, several challenges still exist in achieving accuracy. The presence of impurities or contaminants in the fluid can affect the measurements and lead to inaccuracies. Flow disturbances, such as swirl or turbulence, can also impact the accuracy of the measurements. Furthermore, the selection and installation of the mass flow meter in the system need to be carefully considered to minimize errors.
Best Practices for Maintaining Accuracy in Mass Flow Meter Measurements
To ensure accurate mass flow meter measurements, several best practices can be followed. Regular calibration and verification of the mass flow meter against a traceable standard are essential. Proper installation, including adequate straight pipe lengths, correct orientation, and minimal flow disturbances, should be ensured. Regular maintenance, including cleaning and inspection, is also crucial for accurate measurements. Additionally, keeping the mass flow meter within its specified operating conditions, such as temperature and pressure ranges, is essential for maintaining accuracy.
Conclusion: Importance of Accuracy in Mass Flow Meter Measurements
Achieving accuracy in mass flow meter measurements is vital for efficient operations, quality control, and regulatory compliance. Understanding the working principle of mass flow meters, particularly coriolis mass flow meters, helps in selecting the appropriate technology for accurate measurements. By considering the factors affecting accuracy, employing correction techniques, and following best practices, accurate measurements can be achieved and maintained. Accurate mass flow meter measurements provide valuable insights into processes, enable optimization, and contribute to overall operational excellence.