The petrochemical industry is a complex and critical sector that relies heavily on precise temperature management for efficient and safe operations. Mastering temperature management in petrochemical operations is pivotal to ensuring product quality, process efficiency, and most importantly, the safety of personnel and equipment. In this comprehensive guide, we will delve into the importance of temperature management in petrochemical operations, the role of industrial temperature sensors in petrochemical engineering, guidelines for temperature mapping in petrochemical plants, industrial temperature monitoring systems, specialized thermocouples and thermal resistance, wireless temperature sensors, achieving precise temperature control, field services for petrochemical temperature management, and the types of industrial temperature sensors for petrochemical applications.
Importance of Temperature Management in Petrochemical Operations
Temperature management is a critical aspect of petrochemical operations, as it directly impacts the quality of the products, the efficiency of the processes, and the safety of the plant and personnel. In the petrochemical industry, various chemical reactions and processes are highly sensitive to temperature variations. Even a slight deviation from the optimal temperature range can lead to product quality issues, reduced efficiency, and in extreme cases, safety hazards. Therefore, maintaining precise control and monitoring of temperatures throughout the production processes is imperative. Additionally, compliance with industry regulations and standards pertaining to temperature control is essential for ensuring the overall integrity of the operations.
The significance of temperature management in the petrochemical industry extends beyond the production processes to storage and transportation of the products. Proper temperature control is crucial for preserving the stability and quality of the chemical products during storage and transit. Any fluctuations in temperature can lead to degradation of the products, compromising their usability and safety. Moreover, in the case of hazardous chemicals, temperature control becomes even more critical to prevent accidents and environmental contamination. Therefore, investing in robust temperature management systems and technologies is a key priority for petrochemical companies to uphold their operational excellence and reputation.
In conclusion, the importance of temperature management in petrochemical operations cannot be overstated. It is a fundamental aspect that influences product quality, process efficiency, safety, and regulatory compliance. By prioritizing temperature management and leveraging advanced industrial temperature sensors and monitoring systems, petrochemical companies can optimize their operations, mitigate risks, and uphold their commitment to safety and quality.
Understanding Industrial Temperature Sensors and Their Role in Petrochemical Engineering
Industrial temperature sensors play a pivotal role in petrochemical engineering by providing accurate and real-time data on the temperature conditions within various processes, equipment, and environments. These sensors are designed to withstand the harsh and demanding conditions prevalent in petrochemical plants, including high temperatures, corrosive substances, and potentially hazardous atmospheres. The data collected by industrial temperature sensors is instrumental in enabling precise control of the production processes, identifying potential issues or anomalies, and ensuring compliance with regulatory standards.
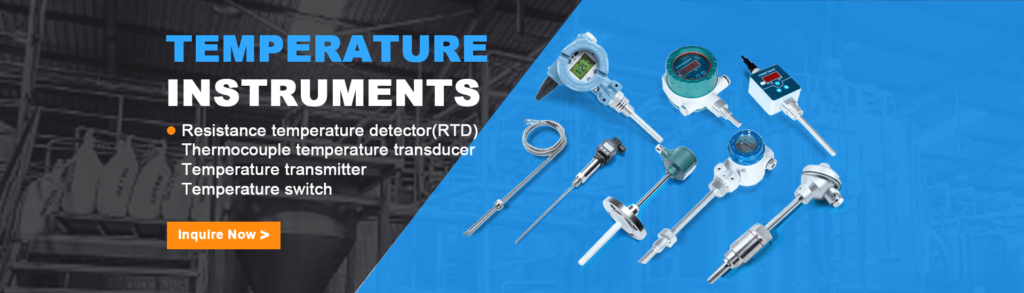
There are several types of industrial temperature sensors commonly utilized in petrochemical operations, each with its unique capabilities and suitability for specific applications. Thermocouples, resistance temperature detectors (RTDs), thermistors, and infrared sensors are among the most prevalent types used in the petrochemical industry. Thermocouples are particularly favored for their ruggedness, wide temperature range, and cost-effectiveness, making them well-suited for the demanding conditions of petrochemical processes. RTDs offer higher accuracy and stability, making them suitable for applications requiring precise temperature measurements. Thermistors excel in sensitivity and responsiveness, while infrared sensors provide non-contact temperature measurement capabilities, ideal for monitoring inaccessible or hazardous environments.
In the context of petrochemical engineering, industrial temperature sensors serve as the frontline defense in ensuring the integrity and efficiency of the production processes. By continuously monitoring and relaying temperature data, these sensors enable proactive maintenance, early detection of potential issues, and optimization of the operational parameters. As a result, petrochemical engineers and operators can make informed decisions, implement timely interventions, and uphold the safety and performance standards of the plant.
Petrochemical Plant Temperature Mapping Guidelines
Temperature mapping in petrochemical plants is a systematic and essential practice that involves the comprehensive assessment and documentation of temperature distribution within various areas and equipment. By conducting thorough temperature mapping, petrochemical plants can identify temperature variations, hotspots, and potential areas of concern that may impact the quality, safety, and efficiency of the operations. The guidelines for temperature mapping in petrochemical plants encompass a series of steps and considerations aimed at ensuring comprehensive coverage, accuracy, and relevance of the collected data.
The first step in temperature mapping involves identifying the critical areas and processes within the petrochemical plant that require detailed temperature assessment. This includes storage areas, reaction vessels, distillation columns, pipelines, and other equipment where temperature variations can significantly impact the production and safety. Once the critical areas are identified, the placement of temperature sensors or data loggers is carefully determined to capture representative and reliable temperature data.
The next phase of temperature mapping entails the collection of temperature data over a defined period, considering various operating conditions, load variations, and seasonal influences. This data is then analyzed to identify temperature patterns, deviations, and potential areas of improvement. Through this process, petrochemical plants can gain valuable insights into the thermal dynamics of their operations, enabling them to optimize their processes, address potential issues, and ensure compliance with temperature-related regulations.
In conclusion, temperature mapping guidelines for petrochemical plants are instrumental in providing a comprehensive understanding of the thermal conditions within the facility. By adhering to these guidelines and leveraging advanced temperature mapping technologies, petrochemical plants can enhance their operational efficiency, mitigate risks, and maintain the integrity of their processes.
Industrial Temperature Monitoring Systems for Petrochemical Operations
Industrial temperature monitoring systems form the backbone of temperature management in petrochemical operations, providing real-time data acquisition, analysis, and control capabilities essential for maintaining optimal temperature conditions. These systems are designed to cater to the diverse and challenging requirements of petrochemical processes, offering robustness, reliability, and accuracy in temperature monitoring. The integration of industrial temperature monitoring systems enables petrochemical companies to proactively manage temperature-related risks, optimize their processes, and uphold the highest standards of safety and quality.
The core components of industrial temperature monitoring systems typically include temperature sensors, data acquisition units, control interfaces, and software applications for data analysis and visualization. These systems are engineered to withstand the harsh environmental conditions, chemical exposure, and potential hazards prevalent in petrochemical plants. The data collected by the temperature monitoring systems is transmitted to control rooms, where operators and engineers can monitor the temperature conditions in real time, detect anomalies, and initiate corrective actions as needed.
One of the key advantages of industrial temperature monitoring systems is their ability to provide historical data logging and trend analysis, allowing petrochemical companies to identify long-term temperature patterns, assess the impact of process changes, and optimize their operational parameters. Additionally, these systems can be integrated with advanced control algorithms and safety interlocks to ensure automatic responses to temperature deviations, thereby mitigating potential risks and preventing safety incidents.
In conclusion, industrial temperature monitoring systems are indispensable tools for petrochemical operations, enabling proactive temperature management, process optimization, and adherence to regulatory standards. By investing in state-of-the-art temperature monitoring systems, petrochemical companies can elevate their operational efficiency, enhance safety, and uphold their commitment to producing high-quality products.
Specialized Thermocouples and Thermal Resistance in the Petrochemical Industry
Specialized thermocouples and thermal resistance play a pivotal role in the petrochemical industry, offering precise and reliable temperature measurement capabilities in the most demanding and hazardous environments. These specialized temperature sensors are designed to withstand extreme temperatures, corrosive substances, and challenging operating conditions prevalent in petrochemical processes, making them indispensable for ensuring accurate temperature monitoring and control.
Thermocouples are widely utilized in the petrochemical industry due to their ruggedness, versatility, and wide temperature range capabilities. They consist of two dissimilar metal wires joined at one end, generating a voltage proportional to the temperature difference between the hot and cold junctions. This voltage is then accurately translated into temperature readings, providing real-time data on the thermal conditions within the petrochemical processes. The adaptability of thermocouples to various chemical compositions and temperature ranges makes them an ideal choice for diverse applications in the petrochemical industry.
Thermal resistance sensors, commonly referred to as resistance temperature detectors (RTDs), offer higher accuracy and stability in temperature measurements, making them suitable for critical and precise applications within the petrochemical plants. RTDs are constructed using a platinum, nickel, or copper wire, whose electrical resistance changes with temperature variations. This characteristic enables RTDs to deliver highly accurate and stable temperature readings, particularly in environments with stringent temperature control requirements.
In conclusion, specialized thermocouples and thermal resistance sensors are indispensable assets in the petrochemical industry, providing accurate, reliable, and durable temperature measurement capabilities essential for optimizing processes, ensuring safety, and upholding the quality standards of the products.
Wireless Temperature Sensors for Petrochemical Operations
Wireless temperature sensors have revolutionized temperature monitoring in petrochemical operations, offering enhanced flexibility, scalability, and cost-effectiveness compared to traditional wired sensors. These advanced sensors leverage wireless communication technologies to transmit temperature data to central monitoring systems, enabling real-time monitoring and control of temperature conditions across the petrochemical plant. The deployment of wireless temperature sensors in petrochemical operations provides numerous advantages, including simplified installation, reduced maintenance costs, and the ability to monitor previously inaccessible or challenging environments.
The wireless nature of these sensors eliminates the need for extensive wiring infrastructure, thereby reducing installation time and costs, as well as minimizing the potential for wiring-related hazards. This makes wireless temperature sensors particularly well-suited for retrofitting existing petrochemical facilities with advanced temperature monitoring capabilities. Additionally, the scalability of wireless sensor networks allows petrochemical companies to expand their temperature monitoring coverage without the constraints of physical wiring, providing the flexibility to adapt to evolving operational requirements.
Furthermore, wireless temperature sensors offer the advantage of remote accessibility, enabling plant operators and engineers to monitor temperature data from any location with network connectivity. This remote access capability enhances the responsiveness to temperature deviations, facilitates proactive maintenance, and enables timely interventions to ensure the integrity and safety of the petrochemical processes.
In conclusion, wireless temperature sensors are a game-changer in petrochemical operations, offering unparalleled flexibility, cost-effectiveness, and real-time monitoring capabilities. By adopting wireless temperature sensors, petrochemical companies can elevate their temperature management practices, enhance safety, and optimize their operational efficiency.
Achieving Precise Temperature Control in Petrochemical Operations
Achieving precise temperature control is a fundamental requirement in petrochemical operations, as it directly impacts the quality, yield, and safety of the products, as well as the efficiency of the processes. The implementation of advanced temperature control strategies and technologies is essential for maintaining optimal temperature conditions throughout the diverse operations within a petrochemical plant. Precise temperature control not only ensures compliance with regulatory standards but also facilitates process optimization, energy efficiency, and overall operational excellence.
The utilization of advanced temperature control systems, such as PID controllers, programmable logic controllers (PLCs), and distributed control systems (DCS), enables petrochemical companies to regulate temperature parameters with precision and responsiveness. These control systems are equipped with advanced algorithms, feedback mechanisms, and safety interlocks to maintain the desired temperature setpoints, accommodate process variations, and respond to temperature deviations in real time.
In addition to control systems, the selection of appropriate heating and cooling equipment is pivotal in achieving precise temperature control in petrochemical operations. Heat exchangers, steam traps, refrigeration units, and insulation materials play a crucial role in maintaining the temperature conditions within the desired range, optimizing energy consumption, and ensuring the safety of the processes.
Furthermore, the integration of advanced temperature monitoring and control technologies, such as predictive analytics, machine learning algorithms, and real-time optimization tools, empowers petrochemical companies to anticipate temperature trends, identify potential issues, and implement proactive measures to optimize their processes and maximize product quality.
In conclusion, achieving precise temperature control in petrochemical operations requires a holistic approach encompassing advanced control systems, optimized equipment, and cutting-edge technologies. By prioritizing precise temperature control, petrochemical companies can enhance their operational efficiency, ensure product quality, and uphold the highest standards of safety and regulatory compliance.
Field Services for Petrochemical Temperature Management
Field services for petrochemical temperature management encompass a diverse range of specialized solutions and support offerings aimed at optimizing temperature control, monitoring, and maintenance within the petrochemical facilities. These field services are provided by experienced and qualified professionals who possess in-depth knowledge of petrochemical processes, regulatory requirements, and best practices in temperature management. The scope of field services for petrochemical temperature management includes calibration of temperature sensors, troubleshooting of temperature control systems, thermal mapping assessments, and preventive maintenance of temperature-related equipment.
Calibration of temperature sensors is a critical aspect of ensuring the accuracy and reliability of temperature measurements within the petrochemical plant. Field service technicians utilize advanced calibration equipment and methodologies to verify the performance of temperature sensors, ensuring their conformity to industry standards and specifications. Regular calibration of temperature sensors is essential for maintaining the integrity of temperature data and upholding the accuracy of the temperature monitoring systems.
Troubleshooting and maintenance of temperature control systems are essential elements of field services for petrochemical temperature management, aimed at addressing potential issues, optimizing the performance of control systems, and ensuring the continuity of temperature control. Qualified field service technicians conduct thorough assessments of the control systems, identify any anomalies or inefficiencies, and implement corrective measures to restore the optimal functionality of the temperature control infrastructure.
Thermal mapping assessments are conducted by field service professionals to provide comprehensive insights into the temperature distribution and dynamics within the petrochemical plant. By leveraging advanced thermal imaging technologies and data analysis techniques, these assessments enable petrochemical companies to identify potential areas of concern, optimize their processes, and ensure compliance with temperature-related regulations.
In conclusion, field services for petrochemical temperature management are instrumental in providing specialized expertise and support to optimize temperature control, monitoring, and maintenance within petrochemical facilities. By engaging experienced field service providers, petrochemical companies can ensure the reliability, accuracy, and compliance of their temperature management practices.
Types of Industrial Temperature Sensors for Petrochemical Applications
The petrochemical industry relies on a diverse array of industrial temperature sensors to meet the stringent demands of temperature monitoring and control across its operations. Each type of industrial temperature sensor offers unique capabilities, advantages, and suitability for specific applications within the petrochemical plants, catering to the varying temperature ranges, environmental conditions, and process requirements.
Thermocouples are one of the most widely used types of industrial temperature sensors in the petrochemical industry, known for their ruggedness, versatility, and wide temperature range capabilities
Multi-point armored thermocouple, thermal resistance
•Multi-point armored thermocouple, thermal resistance
Uses and features: Suitable for temperature measurement at various heights in chemical reactors.
Thermocouple / RTD: K or Pt100
Operating temperature: 0~1050℃
Sheath material: Inconel600; GH3030; 321; 316
Multi-point flameproof thermocouple
• Multi-point flameproof thermocouple
Application: It is suitable for the presence of flammable and explosive compounds in the production site, and it is necessary to measure multiple locations or multiple locations at the same time. Widely used in petrochemical distillation column devices.
The main technical parameters
Electrical outlet: M20x1.5NPTI1/2
Thermal response time: ≤8S
Even wire diameter: Ф1. Ф2. Ф3
Protection class: IP65
Explosion-proof grade: d‖BT4.d‖CT5
Armored integral multi-point thermocouple
• Armored integral multi-point thermocouple
Uses and features: Suitable for temperature measurement at various heights in chemical reactors.
Thermocouple: K thermocouple
Operating temperature: 0~800℃
Sheath material: Inconel600; GH3030; 321; 316
High voltage thermocouple, thermal resistance
• High voltage thermocouple, thermal resistance
Thermocouple / RTD: K or Pt100
Operating temperature: 0~580℃
Sheath Material: 321; 316
Pressure: <10MPa
Anti-leakage package thermocouple
• Anti-leakage package thermocouple
Uses and features: Suitable for temperature measurement at various heights in chemical reactors.
Thermocouple: K thermocouple, S thermocouple, R thermocouple
Operating temperature: 0~1100℃
Furnace tube blade armored thermocouple
• Furnace tube blade armored thermocouple
Uses and features: It is suitable for temperature measurement in high temperature places on the heating furnace wall and furnace tube surface.
Thermocouple: K thermocouple
Operating temperature: 0~1050℃
Sheath material: Inconel600; GH3030; 321; 316
Special thermocouple for cracking furnace
• Special thermocouple for cracking furnace
Application of special thermocouple for cracking furnace: The thermocouple protection tube adopts a professional structure, which makes it close to the inner side of the cracking furnace tube without affecting the flow of materials. It is suitable for temperature measurement and control of cracking furnace in ethylene production process.
Main technical parameters of special thermocouple for cracking furnace
Electrical outlet: M20x1.5, NPT1/2
Connection size: M27x2, NPT3/4
Protection class: IP65
Explosion-proof grade: D‖CT6
Accuracy class: class I
Wear-resistant cut-off thermocouples
• Wear-resistant cut-off thermocouples
Wear-resistant cut-off thermocouple application: The hardness of the steel is increased by surfacing Ni+Wc35 on the wear-resistant head. It is suitable for the presence of high wear-resistant solid particles or fluids in the production site, and the thermocouple can be cut off when the protection tube is damaged. It is a commonly used temperature measuring device for catalytic cracking in refineries.
Main technical parameters of wear-resistant cut-off thermocouple
Electrical outlet: M20×1.5.NTP1/2
Wear-resistant head hardness: HRC62-65
Protection class: IP65
Explosion-proof grade: d‖BT4, d‖CT5
Nominal pressure: 2.5MPa
Wear resistant leakage thermocouple
• Wear resistant leakage thermocouple
Application of wear-resistant and leakage-resistant thermocouples: The stuck wire is used inside the thermocouple to prevent oil leakage or air leakage. It is suitable for the presence of high wear-resistant solid particles or fluids in the production site, and is a temperature measurement device commonly used in oil refineries.
Main technical parameters of wear resistance and leakage thermocouple
Electrical outlet: M20X1.5NPT1/2
Wear-resistant head hardness: HRC62-65
Protection class: IP65
Explosion-proof grade: d‖BT4, d‖CT5
Nominal pressure: 2.5MPa
Air Blow Thermocouple
• Air Blow Thermocouple
Blowing thermocouple application: By blowing nitrogen or other gases, the harmful gas is sent out of the protective tube, thereby prolonging the service life of the thermocouple. It is a commonly used temperature measuring device in the 300,000-ton synthetic ammonia plant.
The main technical parameters
Electrical outlet: M20X1.5, NPT1/2
Accuracy class: I II
Protection class: IP65
Nominal pressure: normal pressure