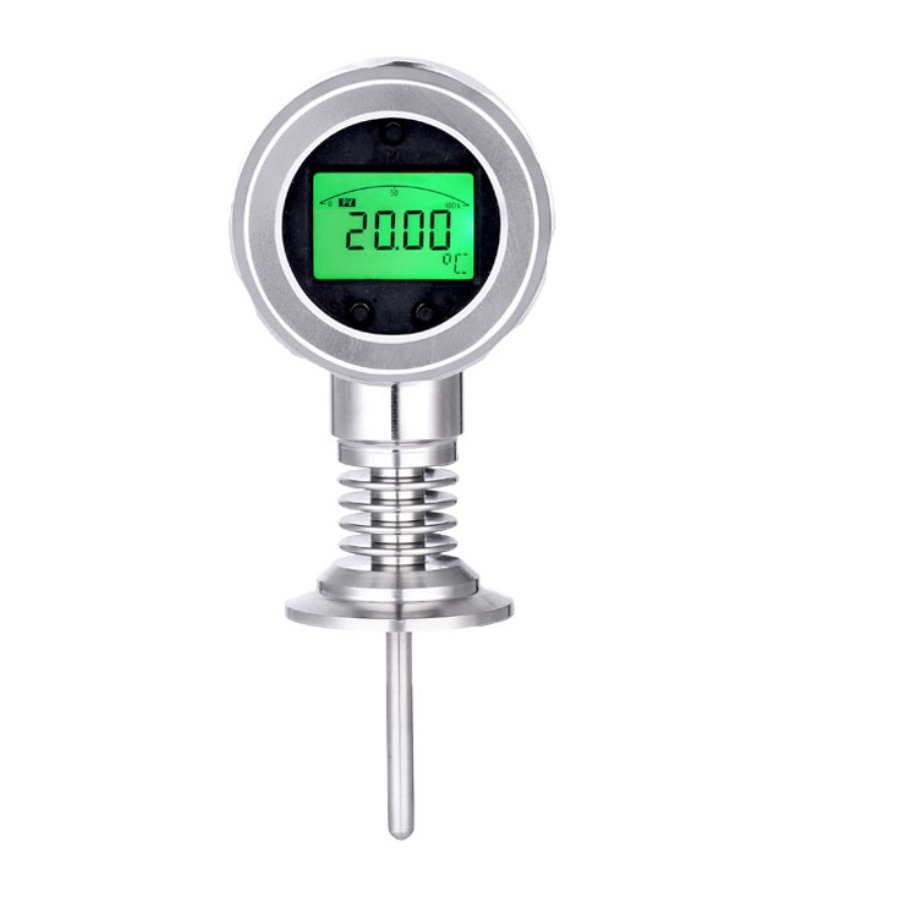
- Tel: +86 28 87436908
- Email: info@cdsentec.com
Process instruments for food processing are essential tools used in the food industry to monitor and control various aspects of the production process including production, warehousing, transportation, etc. These instruments ensure compliance with quality and safety standards while optimizing production efficiency.
In food industry, the food production process instruments require hygiene standards in process production for sugar tank, chocolate vessel, ice cream mixer etc.
The ingredients for making ice cream are accurately weighed and fed into a mixing tank, where the “premix” is made. Afterwards, the premix is passed through the homogenizer at a pressure of about 140 bar and then pasteurized at 80 °C. The level in the premix vessel and the pressure in the pipeline leading to the homogenizer need to be continuously monitored to ensure continuous ice cream production.
The thin juice extracted from sugar beet is thickened by the reduction of excess water in multiple stages at the evaporator station. This evaporation process is carried out under vacuum and heat. The liquid in the evaporator boils so violently that great amounts of vapour are formed. A level sensor is needed to monitor and control the thickening process.
After the “conching” process the liquid chocolate is kept in large tanks for further processing. An agitator stirs the chocolate “mass” to maintain a uniform consistency and temperature in the vessel. A reliable level measurement is required in both the chocolate tank and the downstream filler hoppers to control the production process.
In the production of spices, the spices are first mixed with water and oil to form a slurry. This is fed into an evaporator, where water is removed to turn it into a kind of syrup. The thickened spice syrup must have exactly the right density – so that it can be spread thinly onto metal sheets for oven drying, ready to be ground into powder. To ensure the optimal density of the spice syrup, it requires a continuous measurement during manufacture. The pressure in the feed pipe leading to the evaporator also requires careful monitoring to ensure a smooth-running production process.
SenTec manufactured process instruments ensure compliance with quality and safety standards while optimizing production efficiency. They help maintain consistency, control, and accurate measurements for efficient batch processing, preventing overflow or underfill situations.
Proper food storage is crucial for maintaining food safety and preventing the growth of harmful bacteria.
Barley is stored in malt houses in silos up to 20 metres high before it is processed into malt for production of beer. Filling the silos generates a lot of dust and the material cone geometry constantly changes during the filling and emptying process. A reliable indication of the level ensures the smooth operation by sending signals corresponding to the level or possible limit levels of the grain.
The small batch filler vessels around 1 m high and 60 cm diameter alongside the production facility supply the filler heads of the tank. The products vary from conserve to peanut butter to chocolate spread, with varying viscosity and temperatures. The product density is also changing from each batch. The level system is required to enable an optimal filling of jars.
Flour and sugar are the basic ingredients for many food products and stored in silos up to 20 metres high. The filling and emptying is often performed by pneumatic systems that transport the media from the large external silos and deposit them in smaller holding vessels for further processing. The filling and emptying processes are controlled by reliable level measurement. Pressure monitoring is also needed in the pneumatic conveying pipelines.
Alcohol storage tanks are considered potentially explosive and are therefore kept in special rooms. When the alcohol is needed, it is pumped directly to the appropriate production vessel through a ”ring main” supply system. Reliable measuring instruments are required for dependable measurement of the level in the tank and for monitoring the feed pressure in the pipeline.
During food storage, the storage process temperature, pressure, level sensors, are important factors to make ensure safety and quality standards. They help maintain consistency, control, and accurate measurements for efficient batch processing, preventing overflow or underfill situations.
Proper food storage is crucial for maintaining food safety and preventing the growth of harmful bacteria.
The delivered sugar beets are poured from trucks onto conveyor belts that transfer it to the washing and shredding facility. Multiple level sensors are required to monitor the loading of the beet as it goes on the conveyor belt to optimise the feed rate and energy usage.
The finished meat pellets and kibbles are fed onto a conveyor belt ready for packaging to be sold as pet foods. In order to ensure a continuous supply of meatballs, the conveyor belt requires careful monitoring.
Food transportation monitoring instrument helps optimize the inspection process during food production, allowing operators to thoroughly assess products as they move along the conveyor belts.
SenTec online resource library is a place you can know more knowledge from video, cases study, e-book etc.