Metallurgical processes are integral components of many industries, especially in the mining and manufacturing sectors. They involve the extraction of valuable metals from their ores and their subsequent refinement to achieve the desired properties. This vast field encompasses various techniques and methods, from physical separation to chemical reactions. Understanding these processes is crucial for professionals in the field, as it enables them to make informed decisions and implement effective strategies.
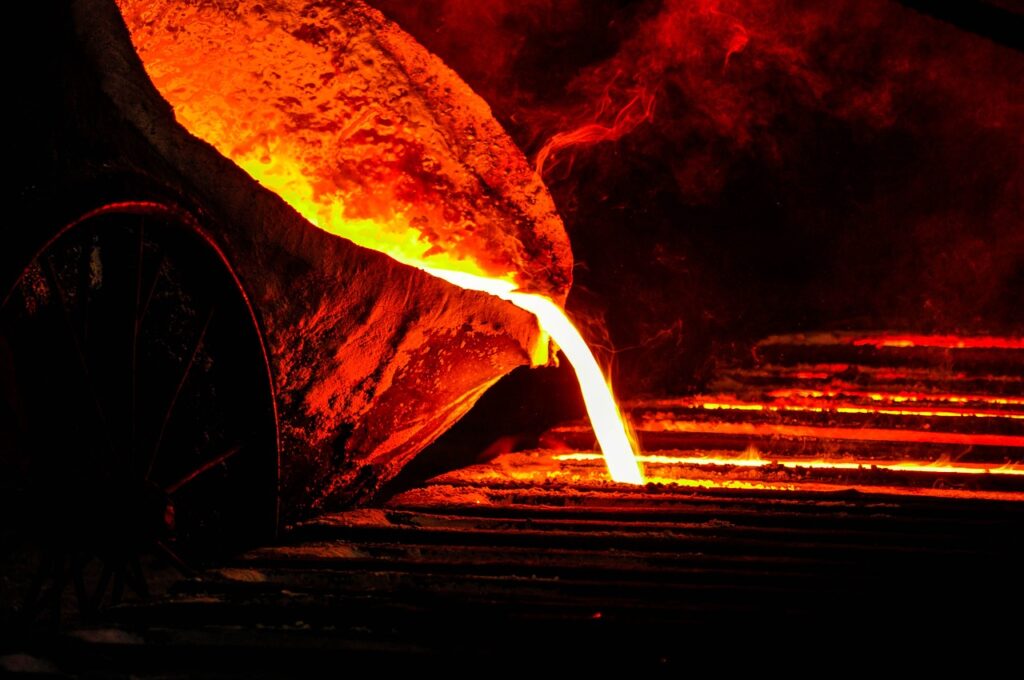
Metallurgical processes are diverse, reflecting the range of metals and minerals available in nature. Each type of ore requires a specific approach to extract its valuable components effectively. As such, metallurgists must have a deep understanding of the properties of different ores and the best methods for their extraction and refinement. This knowledge is not only theoretical but also practical, as it influences the choice of equipment and procedures used in metallurgical plants.
The complexity of metallurgical processes calls for advanced measuring instruments that can accurately determine the composition and properties of ores, as well as monitor the efficiency of the extraction and refinement processes. These instruments play a crucial role in ensuring the quality and consistency of the end products, as well as in optimizing the overall efficiency of metallurgical plants. This article will delve into the intricacies of metallurgical processes and the essential measuring instruments used in them.
What are Metallurgical Processes?
Metallurgical processes are a series of operations that extract metals from their ores and modify them to achieve desirable properties. They involve a combination of physical and chemical methods, ranging from crushing and grinding to smelting and refining. The specific processes used depend on the type of metal being extracted, its ore, and the desired end product.
These processes can be broadly classified into three categories: mineral processing, hydrometallurgy, and pyrometallurgy. Mineral processing, also known as ore dressing, involves the physical separation of valuable minerals from the gangue, or waste rock. Hydrometallurgy uses chemical reactions in aqueous solutions to extract metals from ores, while pyrometallurgy involves high-temperature operations such as roasting and smelting to separate metals from their ores.
Metallurgical processes are not only about extraction but also about modification. After extraction, metals often undergo various treatments to enhance their properties, such as hardness, ductility, corrosion resistance, and electrical conductivity. These treatments may involve alloying, tempering, annealing, and other processes, depending on the type of metal and its intended application.
What is the Metallurgy Process of Mining?
The metallurgy process of mining refers to the sequence of operations involved in extracting valuable metals from mined ores and refining them for use. It begins with the mining of the ore, which involves its extraction from the earth using various methods such as open-pit mining or underground mining. The mined ore is then transported to a processing plant, where it undergoes a series of metallurgical processes to extract the metal.
The first step in the processing plant is usually mineral processing, where the ore is crushed and ground to liberate the valuable minerals from the waste rock. This is followed by concentration methods such as flotation, gravity separation, or magnetic separation to enrich the ore in the valuable mineral.
Once the valuable minerals have been concentrated, they undergo either hydrometallurgical or pyrometallurgical processes to extract the metal. In hydrometallurgy, the concentrated ore is leached with suitable chemicals to dissolve the metal, which is then recovered from the solution by methods such as precipitation or electrolysis. In pyrometallurgy, the concentrated ore is heated in a furnace to separate the metal from the remaining impurities.
The extracted metal is then refined to remove any remaining impurities and to adjust its composition to meet the desired specifications. The refined metal is finally cast into ingots or other forms for further processing or sale.
What are the Metallurgical Process for the Extraction of Metal?
The metallurgical process for the extraction of metal refers to the specific steps involved in separating a specific metal from its ore and refining it. As mentioned earlier, these processes can be broadly classified into mineral processing, hydrometallurgy, and pyrometallurgy, each of which involves a series of specific operations.
In mineral processing, the ore is first crushed and ground to liberate the valuable minerals from the gangue. This is followed by concentration methods such as flotation, gravity separation, or magnetic separation to enrich the ore in the valuable mineral.
In hydrometallurgy, the concentrated ore is leached with suitable chemicals to dissolve the metal. The resulting solution, known as a pregnant leach solution, is then subjected to various processes to recover the dissolved metal. These may include precipitation, where a reagent is added to the solution to cause the metal to precipitate out, or solvent extraction, where a solvent is used to selectively extract the metal from the solution. The metal is then further purified by methods such as electrolysis or cementation.
In pyrometallurgy, the concentrated ore is heated in a furnace to separate the metal from the remaining impurities. This may involve roasting, where the ore is heated in the presence of air to oxidize the impurities, or smelting, where the ore is heated at high temperatures to melt the metal and separate it from the slag. The extracted metal is then refined by methods such as electrolytic refining or fire refining.
Different Process used in Metallurgical Processing
Metallurgical processing involves various processes, each catering to a specific type of ore or metal. These include mineral processing, hydrometallurgy, and pyrometallurgy, as well as various refining processes. Each of these processes involves a series of specific operations designed to extract and refine the metal effectively.
In mineral processing, the ore is first crushed and ground to liberate the valuable minerals from the gangue. This is followed by concentration methods such as flotation, where the ore is mixed with water and chemicals to create a frothy solution that separates the valuable minerals from the waste rock. Other concentration methods include gravity separation, where the ore is processed to exploit differences in specific gravity between the valuable minerals and the gangue, and magnetic separation, where magnetic minerals are separated from non-magnetic ones.
Hydrometallurgy involves the use of chemical reactions in aqueous solutions to extract metals from ores. This process usually begins with leaching, where the ore is treated with a suitable lixiviant to dissolve the metal. The pregnant leach solution is then processed to recover the dissolved metal, either by precipitation, solvent extraction, or ion exchange. The metal is then further purified and refined by methods such as electrolysis or cementation.
Pyrometallurgy includes high-temperature processes such as roasting and smelting to separate metals from their ores. Roasting involves heating the ore in the presence of air to oxidize the impurities, while smelting involves melting the ore to separate the metal from the slag. The extracted metal is then refined by methods such as fire refining or electrolytic refining.
Key Metallurgical Process Plants
Metallurgical process plants are industrial facilities where metallurgical processes are carried out to extract and refine metals. These plants are designed and operated to handle various types of ores and to produce a wide range of metals. Some plants specialize in specific metals, while others handle a variety of metals.
Key metallurgical process plants include mineral processing plants, hydrometallurgical plants, and pyrometallurgical plants. Mineral processing plants carry out physical separation operations such as crushing, grinding, and concentration to prepare the ore for further processing. Hydrometallurgical plants use chemical reactions in aqueous solutions to extract metals from ores, while pyrometallurgical plants involve high-temperature operations to separate metals from their ores.
In addition to these, there are also refining plants where the extracted metals are further purified and adjusted to meet the desired specifications. These plants use various refining processes, such as electrolytic refining, fire refining, and other methods, depending on the type of metal and its intended application.
Essential Instruments in Metallurgical Processes
Metallurgical processes require various instruments to monitor and control the operations effectively. These instruments measure various parameters, such as temperature, pressure, flow rate, and chemical composition, among others. They provide critical information that enables metallurgists to optimize the efficiency of the processes and ensure the quality of the end products.
Essential instruments in metallurgical processes include thermometers, pressure gauges, flow meters, and chemical analyzers. Thermometers are used to monitor the temperature of various operations, especially in pyrometallurgical processes where high temperatures are involved. Pressure gauges measure the pressure in various parts of the plant, such as in leaching tanks or smelting furnaces.
Flow meters are used to measure the flow rate of various fluids, such as water, air, or chemical solutions, in the plant. They ensure that the correct amount of these fluids is used in the processes and that they are distributed evenly throughout the plant. Chemical analyzers, on the other hand, determine the chemical composition of various materials, such as ores, concentrates, or solutions. They enable metallurgists to monitor the efficiency of the extraction and refining processes and to adjust the process parameters as needed.
How Metallurgical Process Instruments Impact Mining
Metallurgical process instruments play a crucial role in mining operations. They provide critical information that enables metallurgists to optimize the efficiency of the metallurgical processes and ensure the quality of the end products. This, in turn, impacts the profitability of the mining operation as a whole.
For instance, thermometers and pressure gauges used in pyrometallurgical processes enable metallurgists to control the temperature and pressure in the furnaces effectively. This ensures that the smelting or roasting operations are carried out at the optimal conditions, thus maximizing the extraction of the metal and minimizing the loss of valuable materials.
Similarly, chemical analyzers used in hydrometallurgical processes provide accurate information about the chemical composition of the leach solution. This enables metallurgists to monitor the efficiency of the leaching process and to adjust the concentration of the lixiviant as needed. This not only maximizes the extraction of the metal but also minimizes the consumption of chemicals, thus reducing the operating costs.
In mineral processing plants, flow meters are used to measure the flow rate of water and other fluids. This ensures that the right amount of these fluids is used in the processes, thus maximizing the efficiency of the separation operations and minimizing the loss of valuable minerals.
Enhancing Metallurgical Processes Through Advanced Instrumentation
Advancements in instrumentation technology have significantly enhanced the capabilities of metallurgical processes. Modern instruments are more accurate, reliable, and versatile than their predecessors, enabling metallurgists to control and optimize the processes with greater precision.
For instance, advanced temperature sensors used in pyrometallurgical processes can measure the temperature in the furnace with high accuracy and reliability. This enables metallurgists to maintain the optimal temperature for the smelting or roasting operations, thus maximizing the extraction of the metal and minimizing the loss of valuable materials.
Similarly, advanced chemical analyzers used in hydrometallurgical processes can determine the chemical composition of the leach solution with high precision. This enables metallurgists to monitor the efficiency of the leaching process accurately and to adjust the concentration of the lixiviant as needed. This not only maximizes the extraction of the metal but also minimizes the consumption of chemicals, thus reducing the operating costs.
Advanced flow meters used in mineral processing plants can measure the flow rate of water and other fluids with high accuracy and reliability. This ensures that the right amount of these fluids is used in the processes, thus maximizing the efficiency of the separation operations and minimizing the loss of valuable minerals.
Case Study: Improving Metallurgical Processing with Proper Instrumentation
To illustrate the impact of proper instrumentation on metallurgical processes, consider the case of a copper mine that implemented advanced process control and instrumentation systems in its hydrometallurgical plant. The plant uses a leaching process to extract copper from the ore, followed by solvent extraction and electrowinning to produce pure copper cathodes.
The plant initially used traditional instrumentation, such as manual thermometers and pressure gauges, to monitor the process variables. However, the metallurgists faced challenges in controlling the leaching process due to variations in the ore composition and other factors. This resulted in suboptimal extraction of copper and higher operating costs.
To address these challenges, the plant implemented an advanced process control system that uses state-of-the-art sensors and actuators to monitor and control the process variables continuously. The system uses temperature sensors to monitor the leaching temperature, pressure sensors to measure the pressure in the leaching tanks, and chemical analyzers to determine the copper concentration in the leach solution.
With the new system, the metallurgists were able to control the leaching process more effectively, resulting in a significant increase in the extraction efficiency. The system also enabled them to reduce the consumption of chemicals and energy, thus reducing the operating costs. The plant reported a 10% increase in copper production and a 15% reduction in operating costs, demonstrating the significant impact of proper instrumentation on metallurgical processes.
Conclusion: The Future of Metallurgical Processes and Instrumentation
The future of metallurgical processes and instrumentation looks promising, with continuous advancements in technology and a growing emphasis on efficiency and sustainability. Advanced sensors and actuators, coupled with sophisticated control systems, are expected to further enhance the capabilities of metallurgical processes, enabling metallurgists to extract and refine metals with greater efficiency and lower environmental impact.
Moreover, the advent of digital technologies, such as the Internet of Things (IoT) and artificial intelligence (AI), is set to revolutionize metallurgical processes. IoT devices can collect and transmit vast amounts of data from various parts of the plant, enabling metallurgists to monitor and control the processes in real-time. AI algorithms can analyze this data and make predictions or recommendations, helping metallurgists to optimize the processes and make informed decisions.
In conclusion, metallurgical processes and their associated instrumentation are essential aspects of the mining and manufacturing sectors. As technology continues to evolve, these processes are set to become more efficient, sustainable, and profitable, contributing to the growth and prosperity of these sectors and the global economy as a whole.