Liquid on-line density transmitter is a continuous on-line measurement of liquid density equipment, which can be directly used in industrial production process.
What is differential pressure online density meter?
Differential pressure online density meter (also known as online density transmitter) is a device for continuous online measurement of liquid concentration and density, which can be directly used in industrial production processes. SenTec intelligent online density meter adopts the principle of differential pressure density meter to calculate the density value according to the differential pressure value of the medium at a certain vertical distance.
Differential pressure density meter measurement principleI
The working principle of differential pressure on-line densitometer is based on the principle of balance of gravity and buoyancy. No matter what liquid it is placed in, the gravity g of densitometer remains unchanged. When it floats on the liquid, the buoyancy f equals to the gravity g, that is, the buoyancy F of densitometer remains unchanged. When the density of the liquid that the densitometer sinks is greater, according to Archimedes principle f = ρ GV, the buoyancy F and G remain the same, the greater the density ρ of the liquid, the smaller the volume V of the liquid discharged by the object, that is to say, the smaller the volume that the densitometer submerges in the liquid, the lower the scale of the liquid corresponding to the densitometer. If the density of the liquid that the densitometer sinks is smaller, the opposite situation will occur.
What are the advantages of On-line densitometer?
Online density transmitter advantages:
1. Select the appropriate measuring pipe diameter according to the working conditions and flow to reduce the flow rate and ensure the high precision of the measurement;
2. The shape between the measuring tube and the diaphragm seat is a bell mouth, which can avoid the retention of medium or gas, and at the same time prevent the fluid from directly impacting the diaphragm, thereby prolonging the service life of the diaphragm.
3. For the medium with high temperature temperature, we use temperature compensation to ensure the accuracy of measurement.
4. The density meter is equipped with a level, which can ensure the vertical installation of the density meter.
5. With an online cleaning port, the differential pressure diaphragm can be cleaned online when the machine is stopped.
Where is a online density meter used for?
*Sugar industry and wine making industry: squeezing juice, syrup, grape juice, etc., alcohol GL degree, ethane ethanol; interface, etc
*Dairy products industry: condensed milk, lactose, cheese, cheese, lactic acid, etc
*Mining: coal, potash, brine, phosphate, the compound, limestone, copper, etc
*Oil refining: lubricating oil, aromatics, fuel oil, vegetable oil, etc
*Food processing: tomato juice, juice, vegetable oil, starch milk, jam, etc
*Pulp and paper industry: black pulp, green pulp, pulp cleaning, evaporator, white pulp, caustic soda, etc
*Chemical industry: acid, caustic soda, urea, detergent, polymer density, ethylene glycol, sodium chloride, sodium hydroxide, etc
*Petrochemical: natural gas, oil and gas washing, kerosene, lubricating oil, oil / water interface
How to install the density meter?
SPX510 series differential pressure desulfurization slurry supply density meter is used for on-line measurement of the density of limestone slurry, gypsum slurry and ammonia desulfurization ammonium sulfate solution in flue gas wet desulfurization. There are a variety of installation main types, which can be installed on the pipeline, the top or side of the slurry tank, and the process connection can be quickly installed with flanges, threads or clamps.
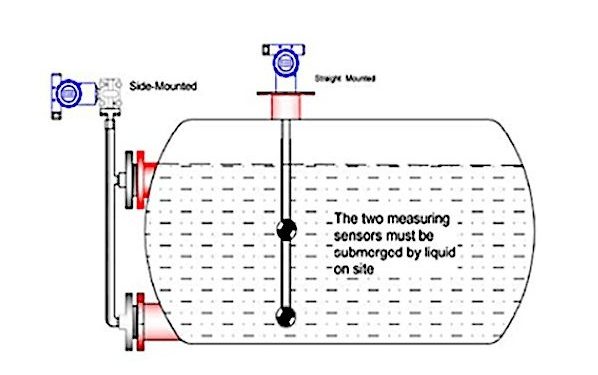
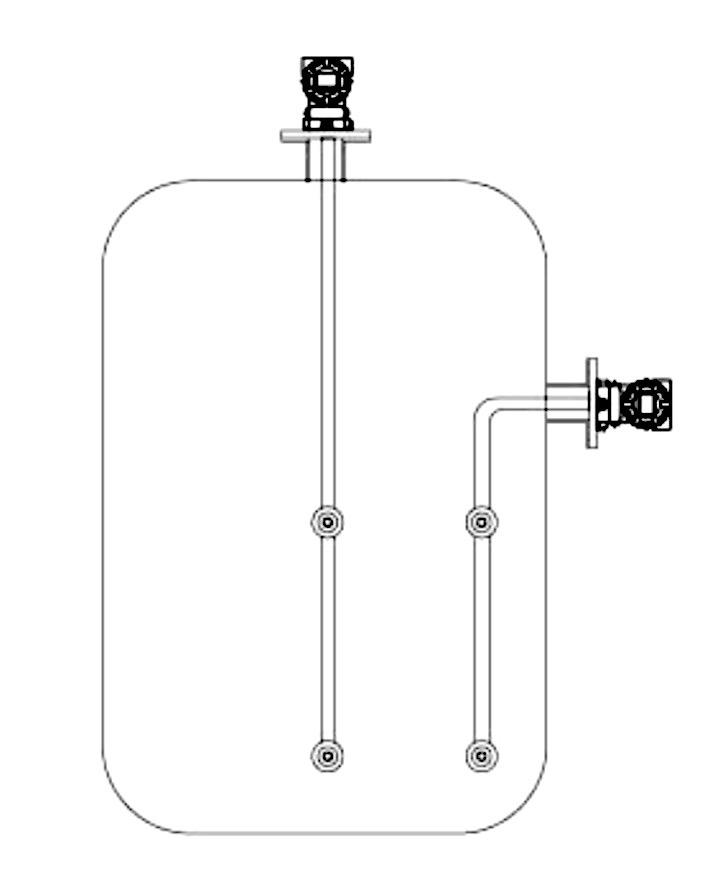
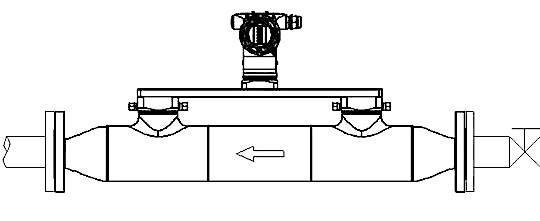
The specific installation drawing shall be designed and determined by the technical personnel on site according to the size of the purchased equipment.
When testing the flowing liquid or the liquid with large vibration, it is necessary to add an auxiliary measuring tank, so as to make the measurement reading stable. When adjusting the flow rate of liquid in the measuring tank, the field operator should consider two requirements: dynamic and reading stability.
The field installation of the densitometer must ensure that two pressure repeaters are on the same vertical plane, otherwise measurement error will occur.