In the realm of industrial process measurement, radar level gauge has become a staple for accurate and reliable liquid and solid level measurement. A radar level gauge, also known as a radar level transmitter, operates on the principle of microwave radar to determine the level of various substances within a container or tank. This sophisticated instrument emits microwave signals towards the substance being measured and receives the reflected signals, allowing for precise determination of the level. The technology has advanced significantly over the years, enabling radar level gauges to be utilized in a wide range of industries, from oil and gas to chemical processing and beyond.
Understanding Radar Level Measurement
Radar level measurement is founded on the principle of time-of-flight (ToF) technology, where the radar pulse is emitted and the time taken for the pulse to return after being reflected by the surface of the substance is measured. This ToF principle enables radar level gauges to provide accurate measurements independent of factors such as temperature, pressure, or chemical properties of the substance being measured. With the ability to penetrate vapor, dust, and foam, radar level measurement offers unparalleled reliability in a wide array of industrial applications.
The radar level measurement process involves the emission of a microwave signal, which travels at the speed of light and reflects off the surface of the substance being measured. By precisely measuring the time it takes for the signal to return, the radar level gauge calculates the distance to the substance’s surface, providing an accurate level measurement. Additionally, modern radar level gauges are equipped with advanced signal processing algorithms to filter out unwanted noise and interference, further enhancing the reliability and precision of the measurement.
Radar level measurement technology has evolved to incorporate advanced features such as frequency-modulated continuous wave (FMCW) radar and pulse radar, enabling even higher accuracy and performance in challenging measurement environments. These advancements have expanded the capabilities of radar level measurement, making it an indispensable tool for industries requiring precise and reliable level measurement.
Factors influencing Radar Level Gauge Distance Measurement
Radar level gauge is a common liquid level gauge. What are the main factors affecting the measuring distance of radar level gauge?
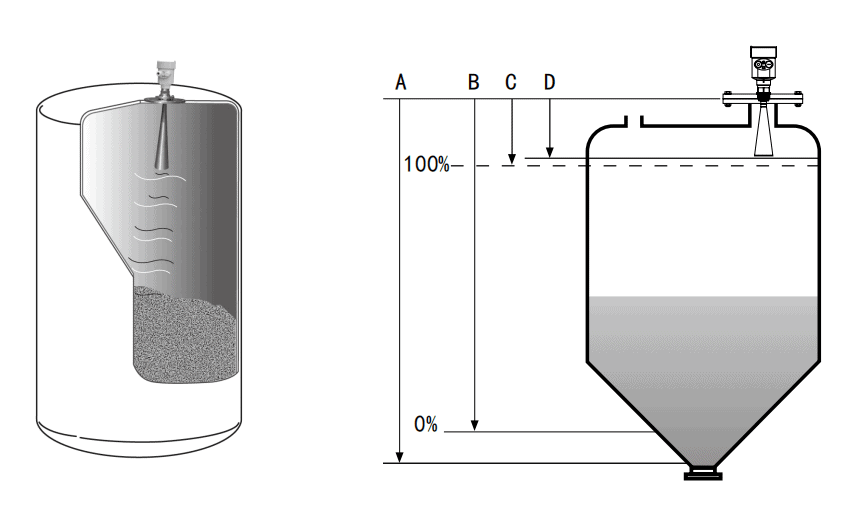
(1) The liquid medium also affects the measurement range. The physical properties of the measured medium are still very large for the measurement range: if the dielectric constant of the liquid is small, the measurement distance of the radar level gauge will be greatly affected, reducing the measurement range. Range; if the dielectric constant of the liquid is large, the measurement distance of the radar level gauge is less affected, which increases the measurement range. In order to ensure high measurement accuracy, liquids can be divided into four categories: A, B, C, and D.
Class A: Non-conductive liquids, such as propane, etc., the dielectric constant is generally less than 1.4, which has a great influence on the measurement distance and makes the measurement range small;
Class B: Non-conductive liquids, such as petroleum, etc., the dielectric constant is generally between 1.9 and 4, which has a great influence on the measurement distance, and the measurement range is only medium;
Class C: such as concentrated acid, organic solvent vinegar, oil-water mixture, etc., the dielectric constant is generally between 4 and 10, which has little effect on the measurement distance and has a large measurement range;
Class D: Conductive liquid, such as aqueous solution, diluted acid and alkali, etc., the dielectric constant has exceeded 10, which has little effect on the measurement distance and has the largest measurement range.
(2) If the measuring liquid is canned, the measurement accuracy of the radar level gauge will not be affected. If the liquid level has ripples, it will affect the measurement.
Best practices for accurate radar level measurement
To ensure accurate and reliable radar level measurement, adherence to best practices is essential. Proper installation of the radar level gauge in accordance with manufacturer guidelines is the first critical step. This includes ensuring unobstructed signal paths, correct mounting angles, and adequate grounding to minimize signal interference and reflections. Additionally, regular inspection and maintenance of the radar level gauge and associated components are vital to ensure optimal performance and longevity.
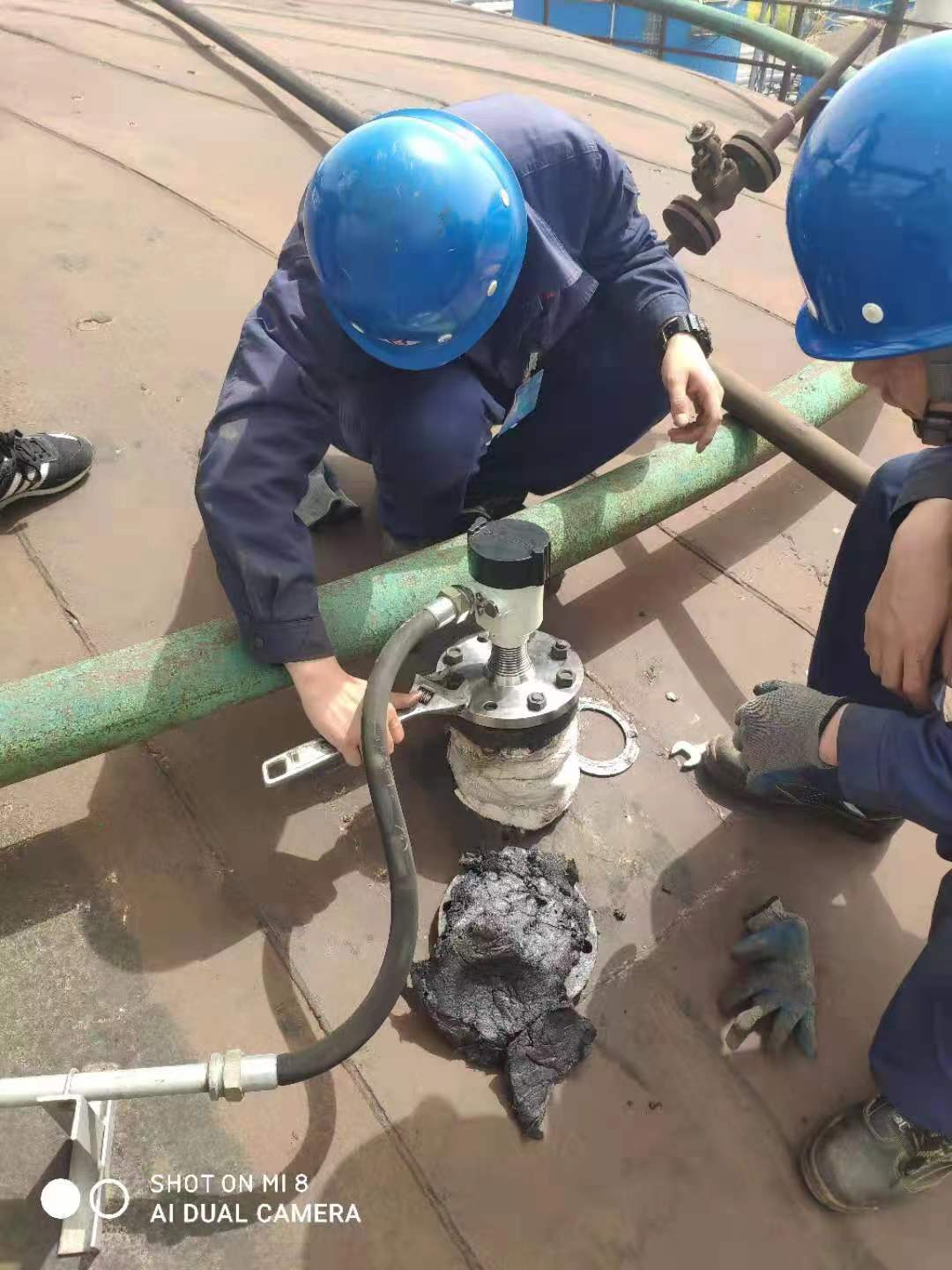
Calibration of radar level gauges is another crucial aspect of achieving accurate measurement. Calibration procedures should be conducted periodically in line with industry standards and regulatory requirements to verify the accuracy of the level measurement. Furthermore, the calibration process should account for variations in dielectric constants, substance properties, and environmental conditions to maintain the gauge’s accuracy across a range of operating scenarios.
Employing advanced signal processing features such as echo mapping and false-echo suppression can significantly enhance the accuracy and reliability of radar level measurement. These features enable the radar level gauge to differentiate between true level reflections and spurious echoes caused by tank obstructions or environmental factors, ensuring precise distance measurement. Additionally, leveraging adaptive algorithms that continuously optimize signal processing parameters based on changing tank conditions can further improve measurement accuracy and stability.
Importance of Radar Level for Tank Gauging
Radar level gauges play a pivotal role in tank gauging, providing accurate and real-time level measurements essential for inventory management, process control, and safety in industrial tanks. In the oil and gas industry, for example, radar level gauges are utilized for monitoring the level of crude oil, refined products, and various chemicals in storage tanks. The precise measurement data obtained from radar level gauges enables operators to optimize tank utilization, prevent overfilling or run-out, and ensure compliance with safety and environmental regulations.
Furthermore, radar level gauges are instrumental in detecting and monitoring interface levels within tanks where multiple substances with differing densities are present. This capability is particularly valuable in chemical processing, food and beverage production, and wastewater treatment plants, where accurate interface level measurement is essential for maintaining product quality and process efficiency. Overall, radar level gauges serve as indispensable tools for efficient and reliable tank gauging across a diverse range of industries.
Advanced Technologies in Radar Tank Gauging
The field of radar tank gauging has witnessed significant advancements in technology, leading to the development of sophisticated radar level gauges with enhanced capabilities. One notable advancement is the implementation of 80 GHz radar technology, which offers improved focusing and signal reflection characteristics, enabling precise level measurement in narrow tanks and vessels with internal obstructions. The higher frequency of 80 GHz radar also provides better measurement resolution, making it ideal for applications requiring high accuracy and sensitivity.
Another advanced technology in radar tank gauging is the integration of advanced signal processing algorithms and software, enabling radar level gauges to compensate for disturbances such as tank obstructions, foam, and agitators. These intelligent algorithms enhance the reliability and accuracy of level measurement, even in challenging tank environments. Additionally, the incorporation of digital communication protocols such as HART and Modbus in modern radar level gauges facilitates seamless integration with industrial control systems, enabling remote monitoring and control of tank levels.
Furthermore, the advent of 3D radar tank gauging systems has revolutionized the way tank levels are monitored and managed. These advanced systems provide not only level measurements but also horizontal and vertical profiling of the tank contents, offering comprehensive insights into tank utilization and substance distribution. With the integration of advanced data visualization and analysis tools, 3D radar tank gauging systems empower operators to make informed decisions and optimize tank operations with unparalleled precision.
Radar Level Gauge Calibration and Maintenance
Calibration and maintenance are vital aspects of ensuring the continued accuracy and reliability of radar level gauges. Regular calibration, typically performed annually or as per manufacturer recommendations, involves comparing the gauge’s measurement readings with a reference standard to verify its accuracy. This process helps identify any drift or deviation in the gauge’s measurement performance and enables adjustments to be made to maintain accuracy.
In addition to calibration, routine maintenance of radar level gauges is essential to address issues such as signal degradation, component wear, or environmental degradation that may affect the gauge’s performance. Maintenance activities may include cleaning the antenna, inspecting cable connections, verifying power supply stability, and checking for any physical damage or corrosion. Proper documentation and record-keeping of calibration and maintenance activities are critical for demonstrating compliance with regulatory requirements and ensuring the traceability of measurement data.
Future trends in Radar Level Measurement
The future of radar level measurement is poised for further advancements and innovation, driven by the demand for increased accuracy, reliability, and efficiency in industrial level measurement applications. One of the emerging trends is the integration of artificial intelligence (AI) and machine learning algorithms into radar level gauges, enabling predictive maintenance, adaptive signal processing, and anomaly detection. These intelligent capabilities will enhance the self-diagnostic and self-optimizing capabilities of radar level gauges, leading to improved performance and reduced maintenance requirements.
Another future trend in radar level measurement is the development of compact and wireless radar level gauges, leveraging miniaturized components and advanced communication technologies. These compact gauges will offer greater flexibility in installation and monitoring, making them suitable for applications where space constraints or remote locations pose challenges for traditional wired gauges. Furthermore, the integration of wireless connectivity will enable real-time data access and remote diagnostics, enhancing operational efficiency and reducing maintenance costs.
The evolution of radar level measurement is also expected to encompass advancements in materials and design, leading to rugged and corrosion-resistant radar level gauges capable of withstanding harsh operating conditions. Additionally, the integration of multi-frequency radar technology will enable radar level gauges to adapt to varying substance properties and tank conditions, further enhancing measurement accuracy and reliability.
Conclusion
Radar level gauges have emerged as indispensable instruments for precise and reliable level measurement across a diverse range of industrial applications. With their ability to operate in challenging environments and provide accurate measurements independent of substance properties, radar level gauges play a crucial role in process control, inventory management, and safety.
As industries continue to seek superior accuracy and efficiency in level measurement, the future of radar level measurement holds promise for further innovation. To learn the factors Affecting the Measuring Distance of Radar Level Gauge offering enhanced to even greater precision, reliability, and operational efficiency in their level measurement applications.
CTA
For more information on radar level gauges and advanced level measurement solutions, please contact us to explore how our cutting-edge technologies can enhance your industrial processes.