Turbine flowmeters play a crucial role in achieving accurate quantitative control systems in various industrial processes. These devices are designed to measure the flow rate of liquids and gases, providing precise data that enables efficient control and monitoring. With their robust construction and reliable performance, turbine flowmeters have become a popular choice for industries that require accurate measurements for optimal operations.
How do turbine flowmeters work?
Turbine flowmeters operate based on the principle of fluid dynamics. As the fluid flows through the meter, it causes the rotor, consisting of multiple blades, to rotate. The rotational speed of the rotor is directly proportional to the flow rate of the fluid. Sensors within the flowmeter detect the rotation and convert it into electrical signals, which are then processed to determine the flow rate.
The design of turbine flowmeters ensures minimal pressure drop, making them suitable for applications where energy conservation is a priority. The accuracy of these flowmeters is highly dependent on the number of blades on the rotor, the size of the blades, and the precision of the sensors. By carefully selecting the appropriate turbine flowmeter, industries can achieve the level of accuracy required for their quantitative control systems.
Advantages of using turbine flowmeters in quantitative control systems
Turbine flowmeters offer several advantages that make them an ideal choice for quantitative control systems. Firstly, they provide excellent accuracy, with some models capable of achieving accuracy levels as high as ±0.1%. This level of precision is crucial for industries that rely on accurate measurements for quality control, process optimization, and regulatory compliance.
Secondly, turbine flowmeters have a wide operating range, allowing them to handle both low and high flow rates. This versatility makes them suitable for a variety of applications, from small-scale processes to large-scale industrial operations. Additionally, turbine flowmeters can measure fluids with varying viscosities, making them adaptable to different types of liquids and gases.
Another advantage of turbine flowmeters is their fast response time. These devices can quickly detect changes in flow rates, enabling real-time adjustments in the control system. This responsiveness is essential for maintaining stability and efficiency in industrial processes where flow rates can fluctuate rapidly.
Components and design of turbine flowmeters
Turbine flowmeters consist of several essential components that contribute to their accurate measurement capabilities. The main components include the rotor, the housing, the sensors, and the electronics.
The rotor, typically made of a lightweight material such as stainless steel or plastic, is designed with precision blades. The number and size of the blades determine the sensitivity and accuracy of the flowmeter. The housing encloses the rotor and directs the flow of the fluid to ensure optimal performance.
Sensors within the flowmeter detect the rotational speed of the rotor and convert it into electrical signals. These sensors can be magnetic or optical, depending on the specific design of the flowmeter. The electronics of the flowmeter process the signals received from the sensors and calculate the flow rate based on the predetermined calibration curve.
The design of turbine flowmeters can vary depending on the specific application and fluid characteristics. Some flowmeters are equipped with additional features, such as temperature and pressure sensors, to provide more comprehensive data for quantitative control systems.
What is quantitative control system ?
The quantitative control system consists of a flow meter, a quantitative controller, a solenoid valve and a quantitative control box. You can control the process of quantitative measurement, quantitative filling and quantitative composition of fluids. The structure is shown below.
Importance of accurate quantitative control in industrial processes
Accurate quantitative control plays a vital role in ensuring the efficiency, safety, and quality of industrial processes. Industries rely on precise measurements to monitor and regulate various parameters, including flow rates, volumes, and concentrations. By maintaining tight control over these variables, companies can optimize their operations, reduce waste, and minimize the risk of errors or inconsistencies.
In industries such as manufacturing, chemical processing, and pharmaceuticals, accurate quantitative control is critical to achieving product consistency and meeting regulatory requirements. Any deviation from the desired specifications can result in compromised product quality, leading to customer dissatisfaction and potential financial losses.
Furthermore, accurate quantitative control enables industries to identify and address issues promptly. By closely monitoring flow rates and other parameters, companies can detect anomalies or deviations from the normal operating conditions. This early detection allows for timely intervention, preventing potential equipment failures, process disruptions, or safety hazards.
Principle of quantitative control
At the beginning of the quantitative measurement, after receiving the signal from the flow meter, the quantitative controller completes the accumulation and visualization inside, and establishes the quantitative control value required within the control box. When the accumulated value shown by the quantitative controller reaches the value When the quantitative control value is set, the quantitative controller emits a switching signal indicating that the solenoid valve is open and the fluid enters the flow sensor. The flow sensor transmits the flow signal to the quantitative controller and begins to measure. When the flow reaches the set value, the quantitative controller issues a command to disconnect the solenoid valve, the water pump, etc., thus achieving the effect of the quantitative control.
Advantages of quantitative control
1. You only need flow measurement sensor, controller and current interruption device, which has a simple structure and low cost;
2. Each quantitative value can be changed arbitrarily as necessary, and should only be completed in the quantitative controller;
3. The display parameters of the quantitative controller include the current accumulation, the total accumulation, the instantaneous flow, the time, the value of the input signal of the flow meter, etc.
4. with control of large and small valves, control the large flow and the small flow respectively, to achieve precise quantitative control.
Applications of turbine flowmeters in quantitative control systems
The combination of turbine flowmeter and quantitative control of PLC can be applied to the filling of community buckets. After the user places the coin, it operates directly on the touch screen and the PLC issues commands. The turbine flow meter controls the valve to open, controlling the passage of a certain amount of water and filling the bucket for precise control of the amount of water per barrel without human intervention. Monitoring rather than wasting purified water only doubles productivity.
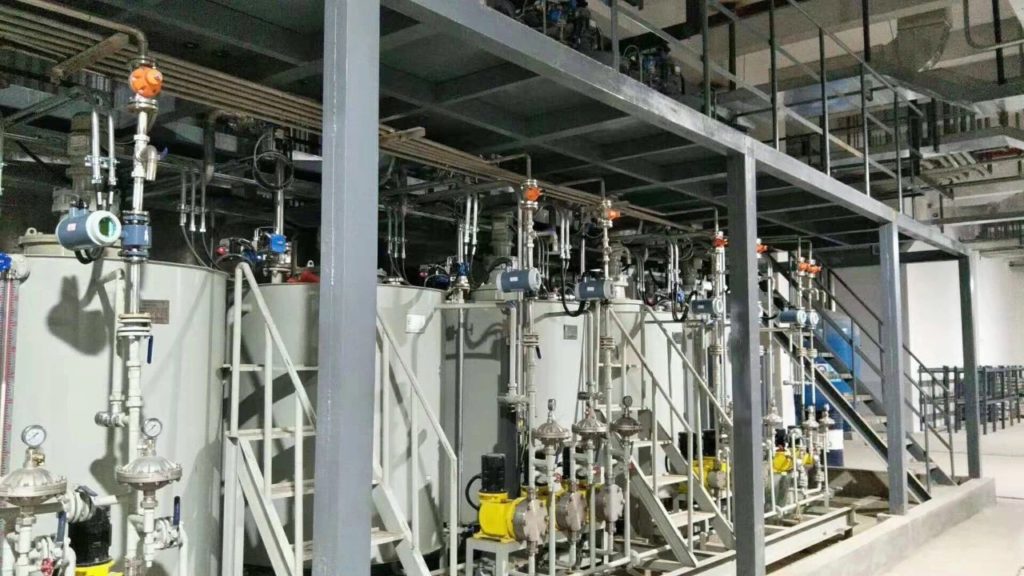
Factors to consider when selecting a turbine flowmeter for your quantitative control system
When selecting a turbine flowmeter for a quantitative control system, several factors should be taken into consideration:
- Flow rate range: Choose a flowmeter that can accurately measure the expected flow rates in your application. Consider both the minimum and maximum flow rates to ensure the flowmeter operates within its specified range.
- Fluid compatibility: Ensure that the flowmeter is compatible with the fluid being measured. Consider factors such as fluid viscosity, corrosiveness, and temperature to select a flowmeter that can handle the specific fluid characteristics.
- Accuracy requirements: Determine the level of accuracy required for your quantitative control system. Consider the specifications provided by the flowmeter manufacturer and select a model that meets your accuracy requirements.
- Installation requirements: Consider the installation conditions and requirements of the flowmeter. Determine whether the flowmeter needs to be installed horizontally or vertically, and whether any additional accessories or piping modifications are necessary.
Installation and maintenance of turbine flowmeters
Proper installation and maintenance are essential to ensure the accurate and reliable performance of turbine flowmeters. When installing a flowmeter, follow the manufacturer’s guidelines and consider the following:
- Positioning: Install the flowmeter in a location that allows for proper flow profile and eliminates any disturbances or obstructions that may affect the accuracy of the measurements.
- Piping considerations: Ensure the flowmeter is installed in a section of the piping system that provides a straight run of pipe before and after the flowmeter. This straight run helps to stabilize the flow and improve the accuracy of the measurements.
- Calibration: Calibrate the flowmeter according to the manufacturer’s instructions and recommended intervals. Regular calibration ensures the accuracy of the measurements over time and allows for any necessary adjustments or corrections.
Maintenance of turbine flowmeters typically involves routine inspections, cleaning, and calibration checks. Regularly inspect the flowmeter for any signs of damage, build-up, or wear. Clean the flowmeter as recommended by the manufacturer to remove any debris or contaminants that may affect its performance. Additionally, periodically check the calibration of the flowmeter to ensure its accuracy.
Common challenges and troubleshooting tips for turbine flowmeters
While turbine flowmeters are generally reliable, they can encounter certain challenges that may affect their performance. Some common challenges include:
- Build-up or clogging: Flowmeters can experience build-up or clogging due to the presence of contaminants or debris in the fluid. Regular cleaning and maintenance can help prevent these issues. If build-up or clogging occurs, follow the manufacturer’s recommendations for cleaning or consider using a filtration system to remove contaminants from the fluid.
- Inaccurate measurements: Inaccurate measurements can be caused by factors such as improper installation, calibration drift, or mechanical issues. Ensure that the flowmeter is installed correctly and follow the recommended calibration procedures. If inaccurate measurements persist, consult the manufacturer or a qualified technician for troubleshooting and repairs.
- Vibrations or mechanical stress: Vibrations or mechanical stress can affect the performance and accuracy of turbine flowmeters. Ensure that the flowmeter is properly secured and supported to minimize vibrations. If excessive vibrations are present in the system, consider installing vibration dampening devices or isolators.
- Fluid compatibility issues: Incompatibility between the flowmeter materials and the fluid being measured can cause degradation or damage to the flowmeter. Ensure that the flowmeter is constructed with materials suitable for the specific fluid characteristics. If compatibility issues arise, consult the manufacturer for alternative materials or coatings.
Conclusion: The role of turbine flowmeters in achieving accurate quantitative control systems
Turbine flowmeters play a crucial role in achieving accurate quantitative control systems in various industrial processes. With their precise measurement capabilities, versatility, and reliability, these flowmeters enable industries to monitor and regulate flow rates, volumes, and concentrations with confidence. By selecting the appropriate turbine flowmeter, considering factors such as flow rate range, fluid compatibility, and accuracy requirements, industries can optimize their operations, ensure product quality, and meet regulatory standards.
When installing and maintaining turbine flowmeters, proper positioning, calibration, and routine inspections are essential for their accurate and reliable performance. By addressing common challenges and troubleshooting issues promptly, industries can maximize the lifespan and efficiency of their turbine flowmeters.
In conclusion, turbine flowmeters are indispensable tools for achieving accurate quantitative control in industrial processes. With their advanced technology and robust design, these flowmeters provide the precise measurements necessary for optimal operations, quality control, and compliance. By leveraging the capabilities of turbine flowmeters, industries can enhance their productivity, reduce costs, and maintain a competitive edge in today’s demanding market.
Call to Action: To learn more about the applications and benefits of turbine flowmeters in quantitative control systems, contact our experts today.