Mass flow meters play a vital role in industrial processes by accurately measuring the flow rate of gases or liquids. These meters are relied upon to ensure the efficiency, safety, and reliability of various industrial applications. However, for a mass flow meter to provide accurate measurements, it must undergo regular calibration. Calibration is the process of comparing the readings of a meter to a known standard to determine its accuracy. This article explores the importance of accurate mass flow meter calibration in industrial processes, the methods involved, common challenges, and the benefits of outsourcing calibration to a professional service provider.
Why Accurate Calibration is Essential in Industrial Processes
Accurate calibration of mass flow meters is crucial in industrial processes for several reasons. Firstly, it ensures the reliability and accuracy of the measurements obtained. In industries such as oil and gas, pharmaceuticals, and chemical manufacturing, even the slightest miscalculation can have significant consequences. Accurate calibration provides confidence in the measurements, enabling operators to make informed decisions based on reliable data.
Secondly, accurate calibration helps maintain the efficiency of industrial processes. Calibration ensures that the mass flow meter operates within its specified range, allowing for precise control of flow rates. This, in turn, optimizes the performance of equipment and systems, reducing energy waste and improving overall productivity.
Lastly, accurate calibration is essential for complying with industry regulations and standards. Many industries have strict requirements for measurement accuracy, especially in sectors where safety is a primary concern. Calibration provides the necessary documentation to demonstrate compliance, avoiding potential legal issues and ensuring the reputation of the company.
Understanding the Basics of Mass Flow Meter Calibration
Before diving into the calibration process, it is important to understand the basics of mass flow meters. Mass flow meters measure the mass or weight of a substance passing through a specific point per unit of time. They differ from volumetric flow meters, which measure the volume of the substance. Mass flow meters offer more accurate measurements since the mass of a substance is not affected by changes in temperature, pressure, or composition.
The calibration process involves comparing the readings of a mass flow meter to a known standard. This standard is typically a traceable reference meter or a calibration device with a known flow rate. The readings obtained from the meter under calibration are then adjusted to match the readings of the standard, ensuring accuracy.
Common problems during field calibration of mass flow meters
In the gas mass flow meters, there are many factors that affect the accuracy of the measurement results of the gas flowmeter, which can be summed up in the following aspects:
①The measurement accuracy of the flowmeter itself;
②The accuracy of the supporting data acquisition and display system;
③Flow rate Measure the environmental impact of the site (including gas medium density, temperature, flowmeter inlet and outlet pressure, gas source fluctuation, airtightness of pipeline system, etc.);
④Whether the flowmeter installation meets the requirements. The practice of removing the flowmeter separately and sending it to the laboratory for verification can only ensure the accuracy of the flowmeter itself, but cannot guarantee the accurate and reliable flow measurement results in actual use. Therefore, on-site calibration of gas flow has gradually become an imperative development trend.
At present, many domestic measuring stations generally encounter problems such as inconvenient on-site installation of the standard, many uncertain factors in on-site calibration, and difficulty in improving the accuracy when performing on-site calibration of gas flow meters. This paper takes the most common calibration method of gas mass flow for sonic nozzles as an example to discuss the accuracy of gas flow calibration in the field.
The principle of on-site calibration of gas mass flow by sonic nozzle method
The sonic nozzle method gas mass flow meter standard device is widely used in the field calibration of gas flow due to its convenient carrying, quick installation and high standard accuracy. The on-site calibration principle is shown in Figure. The standard device is connected in series to the downstream of the system under test, and the principle of sonic nozzle calibration is used—when the ratio of the nozzle outlet pressure to the inlet stagnation pressure is less than or equal to the critical pressure ratio r* (r* value Referring to the relevant technical documents, the air is 0.528), and the gas velocity flowing through the throat of the sonic nozzle is constant. At this time, the gas mass flow is only proportional to the density of the gas medium flowing through the nozzle inlet. By collecting the nozzle inlet pressure p, gas temperature T, and humidity φ, the standard mass flow rate Q flowing through the nozzle is calculated, and compared with the displayed flow rate Q of the system under test at this time, it is concluded that the display value error of the system under test ΔQ=Q is -Q mark.
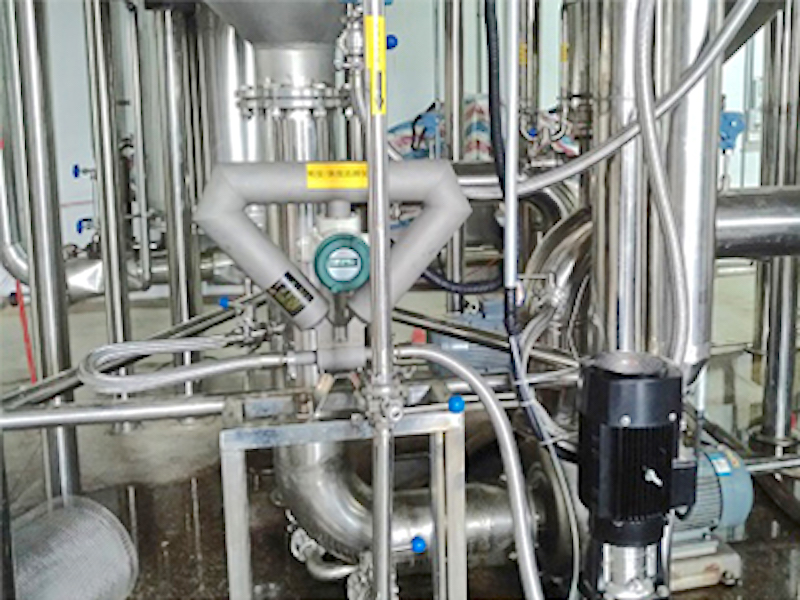
Factors affecting the accuracy of on-site calibration and solutions of Mass Flow Meters
1. Air source fluctuation
1.1 Reasons for influence
Most of the gas source during on-site calibration simulates the actual working conditions of the product, and the fluctuation degree of the gas source is generally large (usually greater than 0.5%), and it is impossible to be as stable as the calibration laboratory (usually not greater than 0.05%). Therefore, there is a common problem of large fluctuations in the gas source when performing on-site calibration of the flow. According to the principle of flow continuity, flow transfer takes time. If the fluctuation of the gas source is large, the flow through the calibrated flowmeter and the flow through the standard device at the same time will be unequal (the difference between the two is calculated as Δq).
If the conventional synchronous instantaneous reading method is used to read the measured flow rate and the standard flow rate, the system error Δq caused by the fluctuation of the gas source will be added to the indication error of the measured system obtained by the final calculation, and the greater the fluctuation range is. is larger, the introduced Δq may be larger. Taking the gas source fluctuation degree of 0.5% as an example, the percentage of systematic errors introduced may also reach 0.5%. Therefore, the large fluctuation of the air source will seriously reduce the accuracy of the field calibration.
1.2 Solution
The influence of air source fluctuation on the flow calibration results can be attributed to the delay in the flow transfer time, causing the flow through the calibrated flowmeter to be unequal to the flow through the standard, thus introducing a systematic error. Therefore, to reduce the influence of air source fluctuation on the flow calibration results, we can start from two aspects: the delay of transfer time and the reduction of the proportion of system error.
Specific solutions:
① Measure the actual distance between the calibrated flowmeter and the sonic nozzle and the gas flow rate, calculate the time Δt required for flow transfer, and delay the start and end time of the standard signal collection by Δt during acquisition to ensure the standard and the calibrated as much as possible. Synchronization of measured traffic between devices.
②Increase the flow accumulation time T of each calibration point, and obtain the indication error of the system under test by calculating the comparison between the calibrated cumulative flow and the standard cumulative flow during this period. As shown in Figure 2, due to the increase of the accumulation time T, the cumulative flow value Qc is increased, thereby reducing the percentage Δq/Qc of the system error, and the purpose of improving the calibration accuracy is achieved.
2. Gas humidity
In many calibration occasions, since the gas without dehumidification is used, in order to improve the calibration efficiency, two methods are usually adopted:
① Do not consider the influence of humidity, and do not measure and correct the humidity;
② Do not measure the gas humidity and estimate it based on experience A humidity value is substituted into the formula to calculate the standard flow. In order to verify the feasibility of the two methods, we analyze the influence of the gas humidity on the flow measurement results and the influence of the gas humidity change on the flow measurement results.
Importance of Regular Calibration and Maintenance
Regular calibration and maintenance of mass flow meters are crucial to ensure their continued accuracy and reliability. Over time, factors such as mechanical wear, contamination, and drift can affect the performance of the meter. Regular calibration helps identify and correct these issues, maintaining the meter’s accuracy within acceptable limits.
Additionally, regular calibration provides a historical record of the meter’s performance. This record can be used to detect any trends or deviations in measurement accuracy, enabling proactive maintenance and preventing unexpected failures.
Conclusion: Ensuring Accuracy and Reliability in Industrial Processes through Proper Mass Flow Meter Calibration
Accurate mass flow meter calibration is an essential component of industrial processes. It ensures reliable measurements, maintains process efficiency, and ensures compliance with industry regulations. By following proper calibration procedures can achieve accurate and traceable measurements and optimize their operations. Regular calibration and maintenance of mass flow meters will help ensure accuracy and reliability, providing the foundation for successful industrial processes.