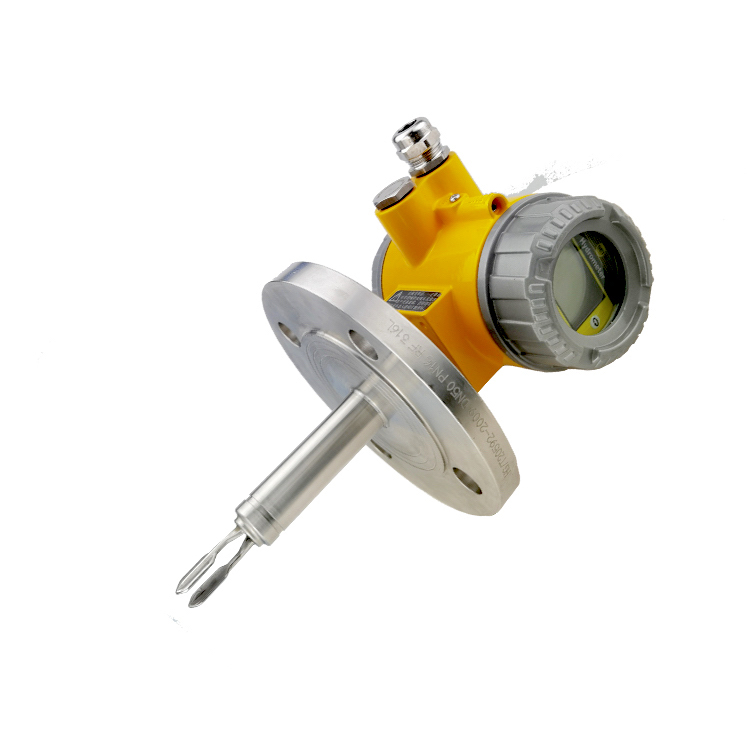
- Tel: +86 28 87436908
- Email: info@cdsentec.com
In the oil refining process, various instruments are used to monitor and control different parameters. SenTec provides a wide range of instrument sensors for the typical applications in the oil refining process: from the delivery of crude oil via pipeline or ship to the storage of finished products.
Crude oil distillation, also known as fractionation, is the first step in the oil refining process in petrochemical industry. It involves separating crude oil into different fractions or "cuts" based on their boiling points.
The precise liquid level control of each tray of the rectification column can ensure the product quality of each stage of hydrocarbons, but the flashing of superheated liquid, adhesion and high temperature all pose challenges to the measurement. Levels and limits must be measured reliably even as process conditions change.
Heavy, high-viscosity residues are concentrated at the bottom of the distillation column. To measure the liquid level of these high-viscosity residues under extreme process conditions, non-contact measuring methods will play a decisive role in the reliability of the measurement. Pressure monitoring at the top of the distillation column is also important to ensure that the process is operating under stable and ideal conditions.
In the petroleum refining process, the delayed coking unit is a very important part, and it is necessary to avoid downtime, loss of production rate or occurrence of overflow as much as possible. The coke drum is tall and reaches extremely high temperatures during operation. By monitoring the density of the gaseous product in the upper layer, the amount of defoamer can be reduced. Accurate level measurement can improve equipment utilization.
In each process section, the reusable pure condensate will be recycled to the condensate tank. The condensed water is formed by the condensation of steam in the steam pipe network, and the purpose of the steam is to provide heat energy in various refining processes. Process temperatures in condensate tanks are generally high, so a level and limit measurement technology must be selected for the conditions.
In the crude oil distillation process, various instruments are used to monitor and control the different parameters. These instruments play a vital role in ensuring the efficiency, accuracy, and safety of the crude oil distillation process in oil refineries.
FCCU, Alkylation, and Reformer are three important processes in the oil refining industry.These processes are crucial for producing high-quality gasoline and other valuable products from crude oil.
The measurement environment for alkylation spent acid is very aggressive, so a robust and stable level measuring instrument is essential for this harsh process condition. Reliable liquid level data can ensure that there is enough acid liquid for use to ensure the stable operation of the alkylation process.
Whether the liquid level control of the debutanizer is accurate determines the quality of the fractionated hydrocarbon products. However, rapid vaporization (flashing), sticking, and extremely high temperatures of feed liquids pose measurement challenges. In order to guarantee the stable operation of the equipment, it is necessary to be able to measure the liquid level and limit safely and reliably under changing process conditions.
Fluid catalytic cracking (FCC) is the most important conversion process in the petroleum refining industry. Like most other refining processes, when the reactor system is running, the vessels in it need to control the liquid level at an optimal position, which plays a decisive role in the production efficiency of the process. By correctly measuring the level, it can also ensure that the expensive catalyst will not be wasted when it is put into use, and the use efficiency can be maximized.
To guarantee the quality of the separation process, boundary level measurement in the separator is very important. By continuously controlling the oil-water interface, it is ensured that the oil does not mix with the water and is discharged, thereby saving costs and improving equipment efficiency. Additionally, vibrating limit switches are available as additional overfill protection.
The FCCU, Alkylation, and Reformer processes in the oil refining industry utilize various instruments to ensure efficient and safe operations.These instruments play a vital role in maintaining process efficiency, accuracy, and safety throughout these refining processes.
Hydroprocessing and sulfur recovery are essential processes in the oil refining industry to remove impurities, particularly sulfur, from crude oil and petroleum products. Hydroprocessing includes hydrotreating and hydrocracking processes
In the alcohol amine deacidification process, the amine liquid is in countercurrent contact with the natural gas from the imported separator in the absorption tower to remove harmful gases such as H2S and CO2 in the process. In order to ensure the efficient operation of the process, the amount of amine liquid accumulated at the bottom of the absorber needs to be accurately monitored.
Whether the liquid level control of the fractionation tower is accurate or not determines the quality of the hydrocarbon products from the fractionation. However, rapid vaporization (flashing), sticking, and extremely high temperatures of feed liquids pose measurement challenges. In order to guarantee the stable operation of the equipment, it is necessary to be able to measure the liquid level and limit safely and reliably under changing process conditions.
When the elemental sulfur is gradually deposited underwater, the operator needs to manually check the boundary in the sulfur precipitation tank. With the instrumentation, the measurement process can be automated to achieve continuous operation of the process and ensure the availability of subsequent containers.
To ensure the quality of the separation process, the boundary level measurement in the high temperature separator is very important. By continuously controlling the oil-water interface, it is ensured that the oil does not mix with the water and is discharged, thereby saving costs and improving equipment efficiency. Additionally, vibrating limit switches are available as additional overfill protection.
Hydroprocessing and sulfur recovery processes in the oil refining industry rely on a variety of instruments to ensure efficient and safe operations. These instruments play vital roles in monitoring and controlling key parameters during the processes.
A tank farm is a facility in the oil refining industry that is used for the storage and distribution of various petroleum products. It consists of a cluster of storage tanks where crude oil and other refined products such as gasoline, diesel, and jet fuel are stored before they are transported to their respective destinations.
In refineries, tanks for crude oil and liquid petroleum products require reliable level measurement for two reasons: one is to allow the tanks to be automatically connected to the product management system and the other is for overflow protection. Multiple instruments may need to be combined on a single process connection to a storage tank.
Liquefied gas storage tanks are generally only accessible during outages every few years and are largely or entirely buried underground, so here the measurement system solution must be independent of process conditions and able to operate at low dielectric constants. As well as transmitting correct and reliable measured values at low temperatures.
In the flare system liquid trap, precise continuous level monitoring must be implemented to prevent liquid from rising up to the flare where it would risk a fire. The level measurement here must guarantee the safety of the process, so it is very important that the measurement range must be able to cover the entire height of the container and continuously report the level to the operator to achieve control of the process. In addition, the accurate interface position can be obtained by measuring the dirty oil area at the bottom of the liquid separation tank.
The liquid level in waste oil pumping stations must be reliably monitored in order to prevent overflow, contamination of subsequent processes or overloading of the pumps. The controller has a built-in pump switching function, which can realize the balanced load of the pump.
In tank farms, various process instruments are used to monitor and control key parameters. These process instruments in tank farms and flares are essential for maintaining safe operations, preventing accidents, and ensuring compliance with environmental regulations in the oil refining industry.
SenTec online resource library is a place you can know more knowledge from video, cases study, e-book etc.