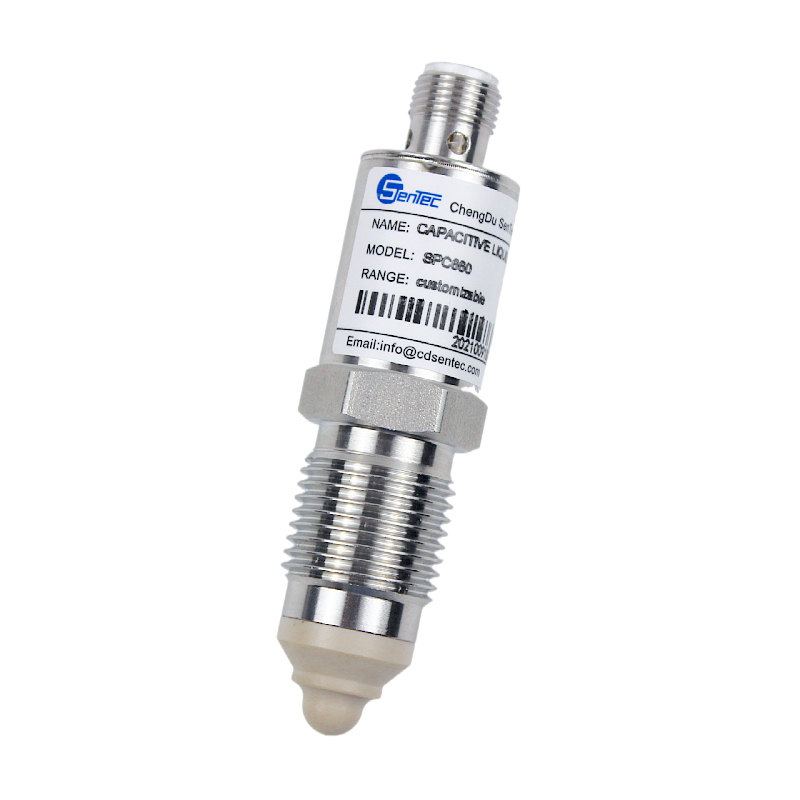
- Tel: +86 28 87436908
- Email: info@cdsentec.com
Process instruments for pharmaceutical processing play a crucial role in ensuring the quality and efficiency of the process. SenTec sensors ensure reliable level, pressure, temperature, and flow measurements during the pharmaceutical production process.
In pharmaceutical industry, pharmaceutical downstream refers to the later stages of the pharmaceutical production process, which involve activities such as formulation, filling, packaging, and distribution of the finished pharmaceutical products.
Often, in the manufacture of pharmaceuticals, substances need to be separated from one another or perhaps some cell components precipitated. One method of doing this is using special filtration systems. When the filter is working properly, the quality and yield of the products are at their optimum. So continuous differential pressure monitoring of the filters ensures the filters are running at their most efficient at all times.
One method for producing and drying granulates is the fluidized bed process. A uniform stream of air is fed up through a distributor plate at the bottom of the fluidized bed reactor. A liquid granule suspension is sprayed in from above, in the air stream it turns into solid granulate and collects on the top of distributor plate and the exhaust air flows through a filter for cleaning. To ensure a high-quality process, both the granulate quantity on the distributor plate and the condition of the filter must be permanently monitored. The measurement technology must also fulfil the most stringent hygienic requirements in order to guarantee a consistently high granulate quality.
Solvents are used in the pharmaceutical industry for extracting active ingredients. They are then recovered via evaporation in a high-vacuum distillation vessel. After the solvent has been removed from the pharmaceutical product by evaporation, it is further processed. Reliable level measurement is required in the distillation vessel for process control.
Pharmaceutical downstream process instruments give ideal solutions for filter system, fluidized bed reactor, vacuum evaporator, drum coater storage tank etc.. They play a crucial role in maintaining the safety, efficacy, and quality of the pharmaceutical downstream processing.
Yogurt production is a complex process that involves several steps to ensure the desired quality, consistency, and safety of the final product. Process instruments play a vital role in monitoring and controlling various parameters throughout the production process.
Pharmaceutical products such as drugs and vaccines are held in batch filling holding tanks ready to be filled into injection vials under absolutely sterile conditions. After each batch, the holding tank has to be totally sterilized using an autoclaving procedure. During this process, the sensor is exposed to a pressure of 2.5 bar and a temperature of 130 °C for at least half an hour. The rapidly changing levels of the aqueous liquids are continuously monitored. The rapidly changing levels of the aqueous liquids require continuous and precise monitoring.
In the production of medical consumables, autoclaves are commonly used for sterilization. Every autoclave has 4 chambers where medical products are sterilized. They work with dry, saturated steam at 2.7 bar pressure and 130 °C. To regulate the water level in the condensate sump, a reliable level measurement is required. The overpressure is also measured to ensure an optimal and safe autoclaving process.
The empty raw capsules and the active ingredient pellets are stored above the filling machine. Reliable level measurement is required here to ensure a continuous supply to the process. The capsules are only lightly stuck together and can be easily sucked apart by a vacuum, so that the upper part separates from the lower part. The pellets are then filled into the lower part of the capsule. After filling, the capsules are transported to the collecting vessels via a hose system. A level detection system serves as overfill protection in these containers.
Pharmaceutical logistics process instruments give solutions for level and pressure measurement in the autoclave, capsule filling process and in the holding tank of a filling system. They contribute to the efficient and secure management of pharmaceutical logistics, ensuring the delivery of safe and effective medications to patients.
Cheese production involves several key steps in the chemical engineering process. Firstly, raw milk is pasteurized to eliminate harmful bacteria. Then, the milk fat content is adjusted through standardization using membrane filtration.
Many different liquids with widely varying properties are required in pharmaceutical production. Products, at all stages have to be stored and held ready for subsequent processing. These are used as catalysts for the decomposition of compounds and stored in a wide variety of concentrations, some of these products are acids. For smooth production and optimal storage, reliable level measurement and point level detection are absolutely necessary.
In preparation for proper disposal, liquid wastes that arise in the production of pharmaceuticals are temporarily stored in buffer tanks. These potentially hazardous mixtures consist of diverse media with very different properties including dielectric conductivity (dielectric constant) and density. For optimal storage, reliable and accurate level measurement is required. Point level detection ensures overfill and dry run protection.
Mixing vessels are applied for preparation, storage and transfer of a wide range of pharmaceutical products. These vessels are used for the manufacture of antibiotics, blood plasma products, and injection and infusion solutions. Following preparation, substances are transferred to a filling station. To ensure a reliable process, the liquid level in the mixing vessel must be reliably and continuously monitored.
Pharmaceutical storage disposal process instruments are tools and technologies used in the management and execution of activities related to the proper disposal of pharmaceutical products. These instruments are crucial in ensuring the safe and environmentally friendly disposal of expired or unused medications.
CIP (Clean-in-Place) cleaning is a vital process in the milk industry that ensures the cleanliness and hygiene of milk dairy equipment without the need for disassembly.
Condense the pipeline water evaporated in the steam separator in the condenser to pure water. A cooling system is installed in the condenser to cool and condense the steam. The supply of coolant will be monitored in the pipeline. By limiting the measurement, it is ensured that there is sufficient condensate water so that no steam directly enters the circulation of the reserve tank.
In the production process of purified water, tap water is first fed into the steam separator. The tap water evaporates there and is then sent to the condenser. Evaporation is achieved by a heat exchanger that supplies saturated steam. To ensure that the heat exchanger is always flooded with pipeline water, it is necessary to reliably monitor the limit. In order to achieve maximum efficiency, the pressure inside the steam separator must be kept constant.
Purified water is used for CIP cleaning of production equipment. This water is produced through filtration and distillation, and then temporarily stored in a water tank. Absolute sterility and cleaning ability are the main requirements for all instrument components that come into direct contact with the medium. This also applies to measuring instruments for measuring liquid level and pressure in storage tanks.
The process technology equipment in the food processing industry adopts validated “in place cleaning (CIP) The process of cleaning ensures that the production container is in a sterile state. Here, sodium hydroxide solution or concentrated acid is usually used as the cleaning agent, which is stored in the storage tank of the on-site cleaning equipment and diluted in the production container. The storage of the cleaning agent can be best controlled through liquid level measurement. Limit measuring instruments are used to prevent overflow and dry operation.
During the CIP process, various process instruments can be used to monitor and control factors such as temperature, flow rate, and chemical concentration. This ensures that the cleaning solution is effective and that the equipment is thoroughly cleaned.
SenTec online resource library is a place you can know more knowledge from video, cases study, e-book etc.