Introduction to Pressure Sensor Hydraulic
A pressure sensor hydraulic is a device that measures the pressure in hydraulics system and converts the data into an electrical signal. This sensor plays a crucial role in monitoring and controlling hydraulic pressure, ensuring efficient operation of the system. The device is used extensively in various industries, such as automotive, industrial machinery, and aerospace, where reliable and accurate pressure monitoring is vital. This article provides a comprehensive guide to understanding and utilizing pressure sensor hydraulic for monitoring hydraulic pressure, thereby maximizing system efficiency.
The pressure sensor hydraulic is a key component in hydraulic systems. It provides real-time data on the system’s pressure, enabling operators to make informed decisions about system operation and maintenance. Without accurate pressure readings, the risk of system failure increases, potentially leading to costly downtime and repairs.
Understanding how a pressure sensor hydraulic works, the different types available, their importance in monitoring hydraulic pressure, and how to choose and maintain the right one for your needs are all vital aspects of effectively utilizing these devices. This guide aims to provide a comprehensive understanding of these aspects, enabling readers to leverage the benefits of pressure sensor hydraulic effectively.
How does a Hydraulic Pressure Sensor Work?
Hydraulic pressure transducer working principle: Hydraulic pressure sensors work by measuring the force exerted by the hydraulic fluid against a surface and converting this force into an electrical signal. This signal is then translated into a pressure reading which can be displayed or recorded for further analysis.
In a hydraulic pressure sensor, the pressure of the hydraulic fluid acts against a diaphragm or piston linked to a transducer. The transducer converts the physical force into an electrical signal proportional to the pressure. The signal is then amplified and conditioned to produce an output that can be read by an instrument or control system.
Different types of hydraulic pressure sensors use different methods to measure pressure, but they all essentially work on this basic principle. The choice of sensor type depends on factors such as the range of pressure to be measured, the required accuracy, the environmental conditions, and the specific application requirements.
Types of Hydraulic Pressure Sensors
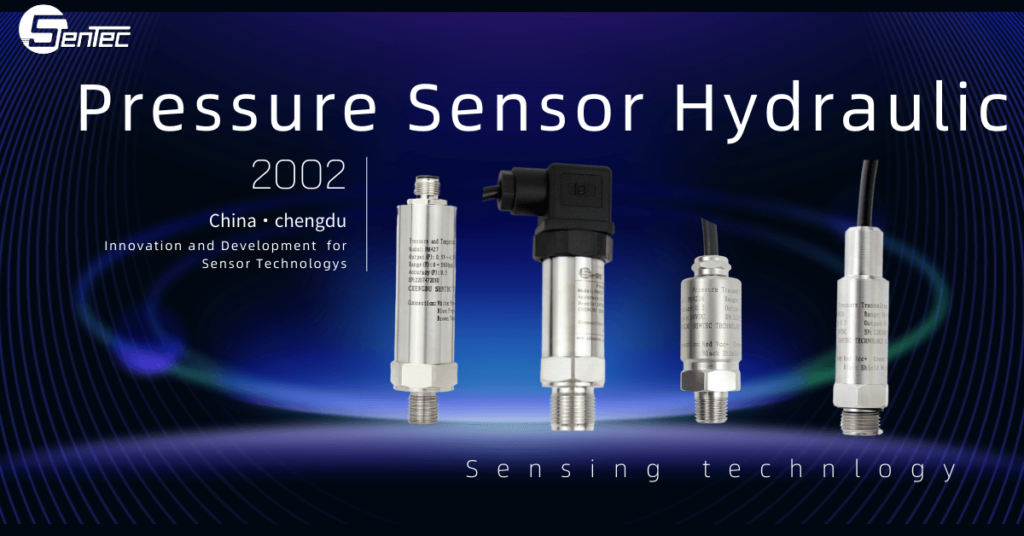
There are several hydraulic sensors types, each with its own unique features and benefits. The most common types include strain gauge sensors, capacitance sensors, and piezoelectric sensors.
Strain gauge sensors are widely used in hydraulic systems due to their high accuracy and reliability. These sensors measure pressure by detecting changes in the electrical resistance of a strain gauge as it deforms under pressure.
Capacitance sensors, on the other hand, measure pressure by detecting changes in electrical capacitance caused by the deflection of a diaphragm under pressure.
Piezoelectric sensors measure pressure by generating an electrical charge when pressure is applied to a piezoelectric material. These sensors are highly sensitive and can measure rapid pressure changes, making them suitable for dynamic applications.
Importance of Monitoring Hydraulic Pressure
Monitoring hydraulic pressure is crucial for the efficient and safe operation of hydraulic systems. Pressure sensor hydraulic provides real-time data on the system’s pressure, allowing operators to detect any changes that could indicate a problem.
The hydraulic pressure sensor helps ensure that the system is operating within its designed pressure range. If the pressure is too high, it could cause damage to the system components. If the pressure is too low, the system may not operate efficiently.
Moreover, monitoring hydraulic pressure can help identify potential issues before they cause system failure. For instance, a sudden drop in pressure could indicate a leak in the system, while a gradual increase in pressure could suggest a blockage. By detecting these changes early, operators can take corrective action before the problem escalates.
Understanding Hydraulic Pressure Transducers and Transmitters
Hydraulic pressure transducers and transmitters are essential components in the process of pressure measurement. A hydraulic pressure transducer is a device that converts pressure into an electrical signal. On the other hand, a hydraulic pressure transmitter not only converts pressure into an electrical signal but also amplifies and conditions it for transmission over long distances.
The main difference between a transducer and a transmitter lies in their output signals. A transducer typically provides a low-level output signal that needs to be amplified for use by a control system. In contrast, a hydraulic pressure transmitter, you can also define it as a hydraulic pressure transducer and display, provides a high-level output signal that can be directly used by a control system.
Both hydraulic transducers and transmitters are used in a variety of applications where precise and reliable pressure measurement is required. They are suitable for both static and dynamic pressure measurements and can handle a wide range of pressures including negative pressure by a hydraulic vacuum transducer.
Role of Hydraulic Transducers and Sensors in Hydraulic Oil Pressure Monitoring
Hydraulic oil pressure monitoring is crucial to ensure the efficient operation of hydraulic systems. Hydraulic transducers and sensors play a vital role in this process by providing real-time data on the system’s oil pressure.
The hydraulic transducer measures the oil pressure and converts it into an electrical signal. This signal is then read by a control system which can use this information to adjust the system operation as needed.
Hydraulic sensors, on the other hand, can provide additional information about the system’s operating conditions. For example, temperature sensors can monitor the oil temperature, which can impact the oil’s viscosity and, therefore, the system’s performance.
Together, hydraulic transducers and sensors ensure that the hydraulic system operates within its designed parameters, preventing damage to the system components and ensuring optimal performance.
Applications of Hydraulic Sensors and Transducers in Various Industries
Hydraulic sensors and transducers are used in various industries to monitor and control hydraulic pressure. In the automotive industry, they are used in braking systems, power steering systems, and automatic transmissions to ensure safe and efficient operation.
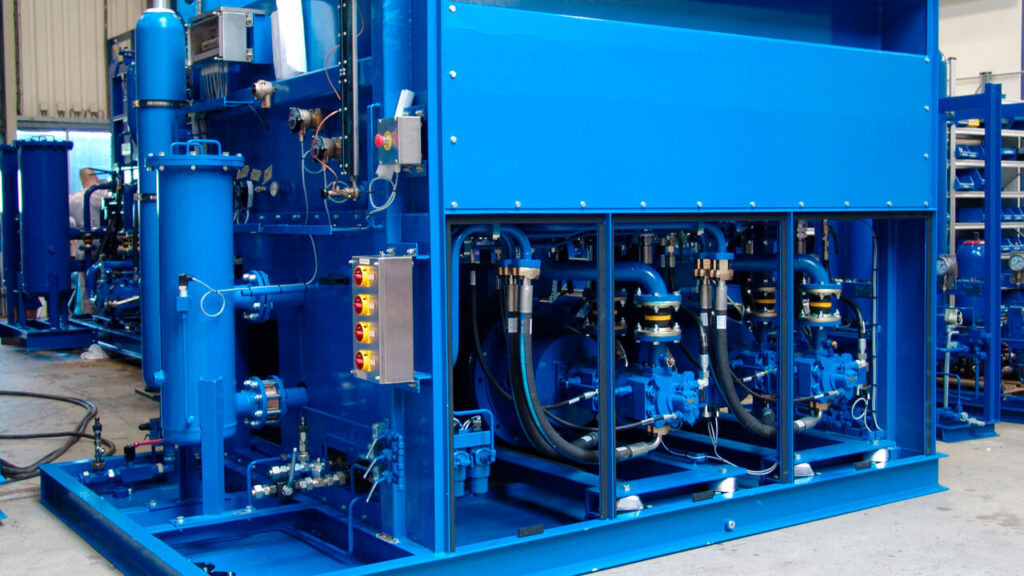
In the aerospace industry, hydraulic sensors and transducers are used in aircraft hydraulic systems to monitor and control the pressure of the hydraulic fluid used to operate various aircraft systems, such as landing gear, flaps, and brakes.
In the industrial machinery sector, these devices are used in hydraulic presses, lifts, and other machinery to monitor and control hydraulic pressure, ensuring safe operation and preventing damage to the machinery.
In the energy industry, hydraulic sensors and transducers are used in hydraulic fracturing (or fracking) operations to monitor and control the pressure of the fracturing fluid, ensuring efficient extraction of oil
Choosing the Right Hydraulic Sensor for Your Needs
Choosing the right hydraulic sensor for your needs is crucial to ensure accurate and reliable pressure measurement. Several factors should be considered when selecting a hydraulic sensor.
Firstly, consider the pressure range that the sensor needs to measure. The sensor should be capable of measuring the maximum pressure that the system is expected to reach, with some margin for safety.
Secondly, consider the accuracy required. While high-accuracy sensors may be more costly, they can provide more precise measurements, which can be crucial in certain applications.
Thirdly, consider the environmental conditions that the sensor will be exposed to. The sensor should be robust enough to withstand the operating temperature, humidity, and any potential exposure to corrosive substances.
Lastly, consider the specific application requirements. For instance, if the sensor needs to measure dynamic pressure changes, a sensor with a high response rate would be suitable.
Contact us to know the hydraulic pressure sensor price
Maintenance and Troubleshooting of Hydraulic Pressure Sensors
Regular maintenance of hydraulic pressure sensors is essential to ensure their reliable operation. This includes regular cleaning of the sensor, checking for any signs of wear or damage, and calibration to ensure accurate pressure readings.
Troubleshooting hydraulic pressure sensors involves identifying and resolving any issues that may affect their performance. Common issues include incorrect pressure readings, no output signal, or a fluctuating output signal.
Incorrect pressure readings can be caused by several factors, such as a damaged sensor, incorrect calibration, or a blockage in the hydraulic system. In such cases, it may be necessary to replace or recalibrate the sensor, or to clear the blockage.
If the sensor does not provide an output signal, it may be due to a power supply issue, a faulty connection, or a failure in the sensor itself. In such cases, check the power supply, check the connections, and if necessary, replace the sensor.
A fluctuating output signal can be caused by changes in the hydraulic system, such as pressure fluctuations or temperature changes. In such cases, it may be necessary to stabilize the system conditions or to use a sensor with a higher response rate.
Conclusion: Maximizing Efficiency with Pressure Sensor Hydraulic
In conclusion, pressure sensor hydraulic plays a crucial role in monitoring and controlling hydraulic pressure. By understanding how these sensors work, the different types available, their importance in hydraulic pressure monitoring, and how to choose and maintain the right one, one can effectively utilize these devices to maximize system efficiency.
Hydraulic pressure sensors, transducers, and transmitters provide valuable data that can be used to optimize system operation, prevent system failure, and reduce maintenance costs. By integrating these devices into your hydraulic systems, you can ensure reliable and efficient operation, ultimately improving your bottom line.
In this rapidly evolving technological landscape, the capabilities of pressure sensor hydraulic continue to expand, offering even greater opportunities for efficiency and performance optimization. By staying informed and proactive, you can leverage these advancements to drive your operations forward and maintain a competitive edge.