During the installation of the pressure transmitter and differential pressure transmitter, we usually do know know the pressure transmitter failure modes and how to solve them. In this article, you may get some ideas for them.
Pressure transmitter failure modes: display value is abnormal
Abnormal pressure value display is a common fault of pressure transmitters. In addition to common zero drift and range migration problems, the causes include damage to components, sensor faults, line faults, electromagnetic interference, pressure tube/ Capillary problems, etc., need to be checked item by item.
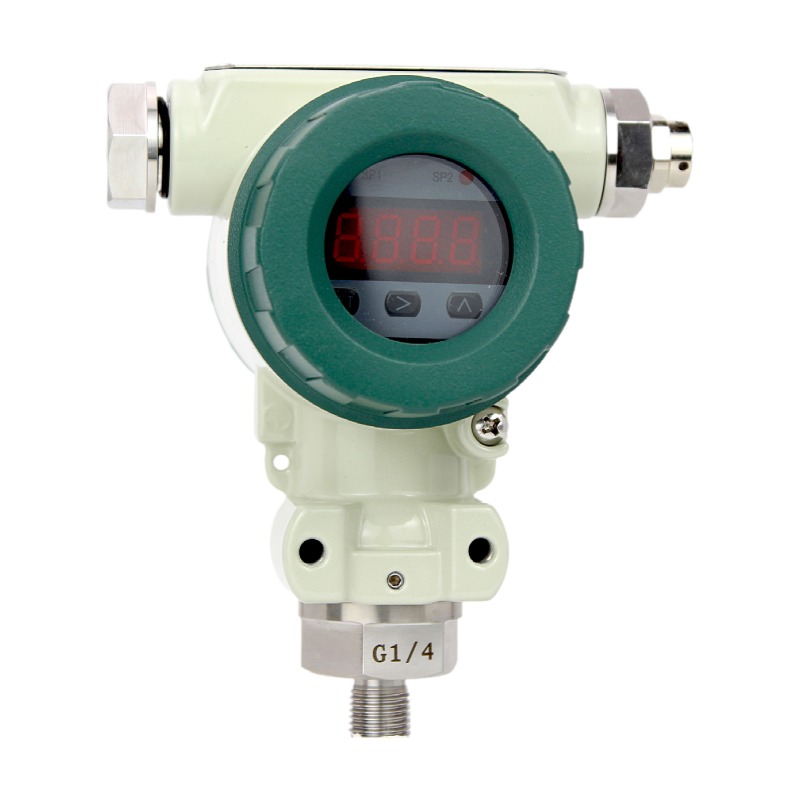
1. When the pressure of the pressure transmitter is zero, it can be handled from the following aspects:
- First check whether the pipeline is under pressure.
- Check whether the power supply of the transmitter is reversed; connect the polarity of the power supply correctly;
- Measure whether the transmitter power supply has 24V DC voltage. If there is no power supply, check whether the circuit is disconnected and whether the instrument is selected incorrectly (input impedance should be ≤ 250 Ω); if the instrument is equipped with a meter, check whether the meter is damaged (you can short-circuit the two wires of the meter first, If the short circuit is normal, it indicates that the meter is damaged); if the meter head is damaged, the meter head should be replaced; connect the ammeter in series with the 24V power circuit to check whether the current is normal; if it is normal, the transmitter is normal. At this point, check whether other meters in the circuit are normal.
- Whether the power supply is connected to the power input terminal of the transmitter; connect the power cord to the power supply terminal.
2. When the pressure indication is incorrect
- First check whether the power supply of the transmitter is normal; whether the reference pressure value is correct. If the accuracy of the reference pressure gauge is low, it is necessary to replace it with a pressure gauge with a higher accuracy.
- Whether the range of the pressure indicating instrument is consistent with the range of the pressure transmitter, the range of the pressure indicating instrument must be consistent with the range of the pressure transmitter;Whether the input of the pressure indicating instrument and the corresponding wiring are correct. If the input of the pressure indicating instrument is 4 ~ 20ma, the output signal of the transmitter can be directly connected;
- If the input of the pressure indicating instrument is 1~5v, a resistor with an accuracy of 1/1000 or above and a resistance value of 250Ω must be connected to the input end of the pressure indicating instrument, and then connected to the input end of the transmitter.
- Whether the corresponding equipment casing is grounded, whether the grounding of the equipment casing is separated from the AC power supply and other power sources, and whether it is separated from the AC power source and other power sources;
- Whether the pressure sensor is damaged. Severe overloading can sometimes damage the isolating diaphragm. It needs to be returned to the manufacturer for repair.
- Whether there is sand, impurities, etc. in the pipeline blocking the pipeline. If there are impurities, it will affect the measurement accuracy; to remove the impurities, add a filter screen before the pressure interface.
- Whether the temperature of the pipeline is too high. The operating temperature of the pressure sensor is -25°C to 85°C, but it is best to be between -20°C to 70°C in actual use. Add buffer tubes to dissipate heat. Before use, it is best to add some cold water to the buffer tube to prevent the superheated steam from directly impacting the sensor, thereby damaging the sensor or shortening its service life.
Possible problems and solutions during installation and debugging. If the pressure does not respond, check whether the pressure pipe valve is normal, whether the jumper switch of the transmitter protection function is normal, whether the pressure pipe is blocked, check the zero point and span of the transmitter, and replace the sensing membrane head.
Pressure transmitter failure modes: components are damaged
It is necessary to consider whether there is a short circuit or open circuit caused by lightning strike, excessive voltage, wrong wiring or cable damage. If it is verified that the electronic components are indeed burned or physically damaged, the damaged components or cables should be replaced in time, and the instrument grounding system should be checked for problems and repaired and maintained in time. It is necessary to pay attention to whether there is water entering the instrument and causing corrosion of the internal electronic components. When the cable interface is not tightly sealed and the sealing ring of the transmitter is aging, it is easy to cause water to accumulate in the meter, resulting in damage to the internal components. At this time, the damaged components should be replaced, and the sealing treatment and inspection of the transmitter should be done well. In a certain project, due to the limited space on site, the cable entry position of the transmitter is installed upwards, resulting in the accumulation of water in the transmitter, which should be taken as a warning.
Pressure transmitter failure modes: Pressure Sensor failure
The diaphragm of the diaphragm pressure transmitter will condense on the diaphragm due to the crystallization of the medium, or the medium contains block solids that impact the diaphragm for a long time, causing the diaphragm to deform and damage and affect the measurement. At this time, the diaphragm should be replaced in time, and according to the actual working conditions, consider adding purging or adding a filter screen at the front end.
Pressure transmitter failure modes: Line failure
Line faults are generally internal wiring, which can be checked by measuring resistance and voltage with a multimeter. Perform wiring operations according to the transmitter instructions to ensure the correct connection of the lines.
Pressure transmitter failure modes: Electromagnetic interference
This kind of fault is generally more difficult to troubleshoot, but the frequency of occurrence is very high. The signal cable of the instrument should not be placed in parallel with the electrical high-voltage signal cable, otherwise it is easy to cause signal interference, resulting in communication errors and inaccurate measurement values. Be sure to follow the standard requirements for distance control and shielding measures. The transmitter installation should also avoid locations with strong magnetic/electric fields or strong vibration sources.
Pressure transmitter failure modes: Impulse tube, capillary problem
The pressure pipe problem usually occurs due to the characteristics of the medium, non-clean medium, or medium with high viscosity, which causes the blockage of the pressure pipe and cannot feedback accurate pressure values. Or the pressure tube may leak due to long-term use, resulting in measurement inaccuracy. If this happens, replace the pressure tube in time, and do regular cleaning and maintenance work. The capillary will have problems due to the inaccurate selection of the pressure oil temperature resistance. In low temperature conditions, it is necessary to select the appropriate pressure guiding oil to avoid the phenomenon that the pressure guiding oil solidifies due to the low temperature. Similarly, when it is necessary to pay attention to the high temperature, the pressure guiding oil should be avoided to vaporize.
In addition, the influence of the actual use environment of the pressure transmitter on the product needs to be considered in the fault analysis. For example, when measuring the steam medium, the method of connecting the condensing ring to the transmitter is adopted, but it is ignored that the ambient temperature will reach -30 in winter. Below ℃, this causes that although the medium is steam, in winter, the liquid in the condensing circle is still frozen into ice, which makes the pressure transmitter unable to sense pressure.