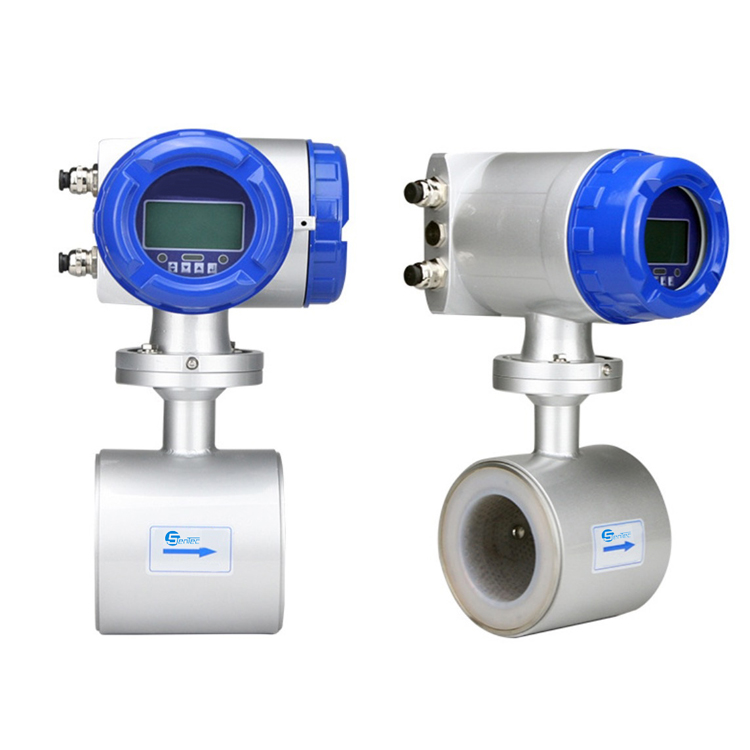
- Tel: +86 28 87436908
- Email: info@cdsentec.com
Process instrumentation plays a crucial role in the power industry by enabling the analysis, measurement, and control of various industrial process parameters. As power technology suppliers, both SenTec and Siemens, offer a wide range of process instrumentation and analytics solutions tailored for the power industry.
SenTec is an experienced supplier of process instrumentation for coal power industry. The process instrumentation and analytics sensors for level, flow, pressure, temperature measurement are optimized and certified for use in the energy sector.
In coal-fired power plants, lignite and anthracite are temporarily stored in bunkers up to 30 meters high. In order to ensure uninterrupted transportation of coal conveyor belts, safe and reliable level measurement is indispensable here. The additionally installed limit detection instrument is used to prevent the coal bunker from overflowing.
In a steam cycle, pressure flow and temperature must be monitored at different points in the process. Especially reliable measured values are required at the turbine inlets of different pressure classes.
Turbines are highly complex systems in which lubricants play an important role. Lubricating oil keeps the turbine running properly, keeps maintenance costs to a minimum and prevents turbine downtime. Turbine oils are derived from the highest quality mineral oils, which have special properties in terms of anti-emulsification (separation of water) and degassing. The oil level in the oil reservoir must be monitored to ensure there is always enough lubricating oil.
In coal-fired power plants, anthracite or lignite is burned as the main fuel. The coal is conveyed to the combustion furnace by different conveyor belts. Level measurement is necessary to prevent back-blocking or overflows at transfer stations on conveyor belts. Uninterrupted feeding of the furnace is only possible if the level is reliably measured at the conveyor belt transfer station. Additional installed limit detection instrument to prevent overflow in transfer station
Coal power process instrumentation are crucial for ensuring safe and efficient plant operation. They provide real-time data monitoring on temperature, pressure, flow rate, level, and other critical parameters with durable, reduce running costs and absolutely guarantee process safety.
Hydroelectric power refers to the generation of electricity using the force of flowing water. It involves damming up a river or creating a reservoir to store water, which is then released through penstocks to drive a turbine.
Pumped storage power plants store a large amount of energy and feed it into the grid very quickly when necessary. One important parameter is the height of the water level in the reservoir. It allows calculations to be made about the amount of energy available and the existing storage volume in pump operation mode. High reliability is required from the measurement technology deployed, because the sensors are often mounted at very remote locations.
A large number of sensors are deployed to ensure reliable operation of the generators and turbines in the hydroelectric power plant. They monitor the pressure in the hydraulic lines, the lubricant supply for turbine bearings, vibration, temperatures and many other parameters. At the lowest point of the plant, cooling water from the generators and any leakage water from the Kaplan or Francis turbines is collected in a seepage water shaft, pit or sump. To prevent a flooding of the shaft and thus of the turbine building, with disastrous results for equipment, the sensors are often installed redundantly. As additional protection, the maximum water level is monitored with a point level switch.
In a hydroelectric power plant, water is conveyed from the dam to the turbines through penstocks. A partial or complete rupture of a pressure line can increase the flow in the line beyond the maximum flow. If the leak goes undetected, it can cause floods and destroy power plants, resulting in lost production. Therefore, it is important to measure the flow reliably in order to detect if there is a rupture in the pipeline and then take the necessary action, such as closing the pressure valve.
Hydroelectric power process instrumentation refers to the measurement and control systems used in hydroelectric power plants to monitor and regulate various parameters during the power generation process. These instruments play a crucial role in evaluating performance, ensuring efficiency, and maintaining safe operation.
Wind power is a clean and renewable energy source that harnesses energy from the wind to create electricity. It is one of the fastest-growing energy sources globally, offering numerous advantages.
Efficiency is also crucial in wind power generation: the higher the plant utilization, the more economical it is and the faster the return on investment. The conversion of wind energy to power generation is realized through the gearbox in the nacelle. Whether all parts are fully lubricated has a great impact on the life and utilization of the fan. Therefore, the oil level of the nacelle gearbox must be permanently monitored.
The operating environment of wind turbines in offshore wind farms is very harsh. Not only do they need to face the continuous washing of waves and severe winds, but they also need to be able to withstand the corrosion of sea water. The structure and location of the wind turbine determine that seawater will inevitably enter the tower. The water level inside the tower needs to be continuously monitored to detect leaks early and avoid increased corrosion. In addition, it is also necessary to monitor the tidal water level and wave height to grasp the wave load and the surrounding environment.
Wind power systems require monitoring of wind speed and direction to optimize their performance and reliability. Monitoring wind speed over an extended period of time is crucial for assessing the wind energy potential at a specific location.
Wind power process instrumentation sensors are essential for monitoring and controlling various parameters in wind power generation. They enable operators to optimize performance, ensure safety, and maximize energy production from wind turbines.
SenTec online resource library is a place you can know more knowledge from video, cases study, e-book etc.