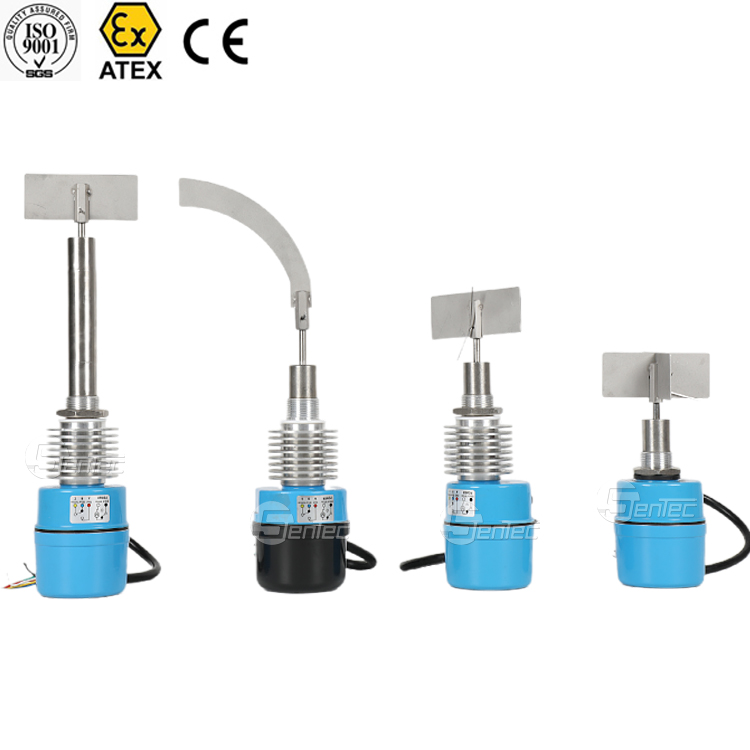
- Tel: +86 28 87436908
- Email: info@cdsentec.com
In the cement industry, various types of sensors are applied for different purposes. Cement temperature sensors, typically thermocouples, are used for monitoring purposes within the cement manufacturing process. Additionally, Level, pressure, flow sensors are employed to easy-to-measure online process variables. These sensors play a crucial role in ensuring optimal operations and quality control in the cement industry.
Cement manufacture is a complex process that involves the mixing of raw materials, grinding, and heating to high temperatures in a kiln to produce clinker. To ensure optimal operations and quality control, various types of sensors are employed in the building construction cement industry.
To produce cement, the raw meal is burned to clinker in a long rotary kiln. After leaving the rotary kiln, the clinker has a temperature of up to +1300 °C and must be cooled down to a temperature of about +200 °C for further storage. To achieve this, the clinker bed is cooled with a continuous stream of air. Pressure monitoring is required in the lower part of the clinker cooler to make the cooling as effective as possible. The material height of the hot clinker, at over 1000 °C on the conveyor belt, also has to be reliably measured.
To attain high quality and uniform material consistency in the finished cement, the raw material is homogenized in a so-called blending bed. The rock is distributed evenly over the blending bed with a stacker. Material is removed with a scraper. To ensure that the incoming material is distributed as evenly as possible, the level must be continuously measured.
In the cement manufacturing industry, various types of temperature, pressure and level sensors are employed for monitoring and quality control purposes. These sensors are used to gather data and provide real-time information on parameters, enabling effective quality control and process optimization.
Proper storage of cement is crucial for maintaining its quality and ensuring its fitness for use in construction projects. By following these guidelines, construction professionals can ensure that cement is stored properly, preserving its quality and ensuring optimal performance in construction projects.
Before further processing, the cement is stored in tall silos. The cement is transported both in and out of the silo via pneumatic conveying. Efficient storage and transport of the product is ensured by accurate level measurement and point level detection, as well as also monitoring the pneumatic conveying system pressure and flow.
To maintain a high quality and uniform material consistency in the finished cement, the raw materials are homogenized in a blending bed. To achieve this the rock is distributed evenly over the blending bed with a stacker. Material is reclaimed in reverse order with the help of a scraper. In order to optimally control the conveyor systems, their positions must be determined as precisely as possible.
In bulk material measurements in cement plants, before being burned in the rotary kiln, the material from the blending bed and the aggregates are ground to a fine raw meal in large mills. The powdery material is then transported to the silo by a pneumatic conveyor system. Reliable monitoring of the level is essential for optimal raw material storage.
Large amounts of energy are needed to burn clinker in rotary kilns. Substitute liquid fuels such as spent oils or recovered solvents are often used for this purpose. The fuel storage tanks often contain a mixture of solvents, which can produce fumes and vapours in the air space. Due to the large amount of energy needed in cement production, the fuel inputs represent a significant cost factor, so accurate level measurement is essential.
There are several types of cement sensors used for monitoring cement storage. These sensors are designed to measure and monitor the level, temperature, and pressure and flow of cement in storage facilities. These cement sensors can be employed to analyze data from various sensors and provide insights into the overall storage conditions and the quality of the cement.
Cement transportation involves the movement of cement from manufacturing plants to construction sites or storage facilities. This process requires careful monitoring to ensure the quality and integrity of the cement during transit.
The air compressor system generates the necessary compressed air to transport the material from the silos via the network of feed pipes. To ensure a smooth, steady flow of material, reliable pressure monitoring in the compressors and conveying channels is required.
The transport of coarse and fine bulk solids within a stone processing facility takes place in most cases via conveyor belts. To achieve an even throughput and compensate for volume fluctuations during transport, belt transfer points are integrated in the conveyor line. The incoming bulk material is briefly stored in a buffer silo to prevent belt overfilling. This is the point where the level and the point level must be monitored.
Dust-free, closed loading systems are needed for fine aggregates and finished products such as cement. Automated loading of trucks is preferred in the industry and, while the load quantity is determined with a weighing system, it must be ensured that the truck is in the correct place and not overfilled. Reliable point level detection and vehicle positioning shortens loading times, increases throughput and improves the efficiency of the entire syste
In cement transportation pipelines, flow measurement is crucial to ensure the accurate and efficient movement of cement from manufacturing plants to construction sites or storage facilities. SenTec FMT700 target flow meter provides a reliable and cost-effective solution for monitoring the flow of cement during transportation.
Various types of pressure, level, flow sensors are used in cement transportation to ensure efficiency, safety, and optimal conditions.These sensors enable precise control, automation, and monitoring of the transportation process, ensuring optimal conditions and compliance with standards in cement industry.
SenTec online resource library is a place you can know more knowledge from video, cases study, e-book etc.