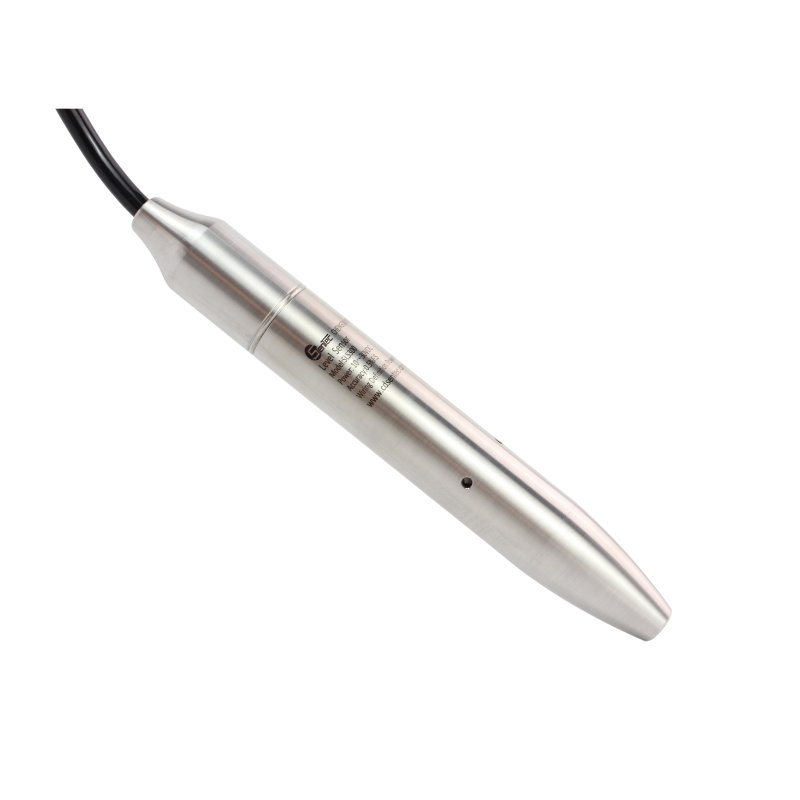
- Tel: +86 28 87436908
- Email: info@cdsentec.com
Vessel sensors play a crucial role in shipbuilding, providing essential data for vessel maneuvering and performance monitoring. SenTec offer shipbuilding vessel level and pressure sensor solutions with accuracy and dependability.
In ships industry, shipbuilding ballast tanks are an integral part of a ship's design and construction. These tanks are used to maintain the ship's stability by adjusting its buoyancy.
Among the most important measurements on board ships are those for determining draught, trim and list. In general, one measuring point is placed on the bow and another is used in the aft. On larger ships, two additional measuring points are installed on both the port and on the starboard. Accurate level measurements are required to determine the exact values of ship position and draught.
The ballast water measurements in the wing and double bottom tanks go directly into the control system for the ship trim, draught and list. Since these measuring points are virtually inaccessible during operation on board, reliability and stability are an absolute must. Pressure shocks, abrasive sand particles and seawater place additional heavy demands on the instrumentation.
When the ship encounters wind and waves, asymmetry in cargo loading and unloading, or centrifugal force generated by rapid turns, the anti-heel system can correct the ship’s inclination. It consists of ballast water tanks connected by a piping system, which can resist the heeling of the ship caused by various reasons. Depending on the tilt of the ship, pumps or blowers (compressors) in the ballast tanks fill or empty the tanks with air. In order to achieve control of this anti-rolling system, reliable level measurement is necessary.
A semi-submersible ship is characterized by having many ballast water tanks, which allow the ship to sink its deck into the water to carry large floating cargo. By pumping water out or moving air into ballast tanks, ships can lift their cargo and maintain balance. In order to prevent damage to ballast tanks due to overpressure or underpressure, it is necessary to continuously monitor the pressure and liquid level in the tank.
Ballast tank water level and pressure sensors are essential components in shipbuilding for monitoring and controlling the ballast water treatment process. These sensors play a crucial role in ensuring the safe and efficient operation of shipping vessels.
Cargo tanks for shipbuilding are specifically designed to store and transport various types of cargo, particularly oil. These tanks are equipped with inert gas systems and crude oil washing systems to ensure the safety and efficiency of oil storage.
According to strict safety and environmental regulations, it is imperative to monitor the liquid levels in cargo tanks on board chemical tankers, especially during loading and unloading operations. This is because if a tank full of cargo leaks, the medium may flow onto the deck or into the seawater, causing devastating consequences to the human body and the environment. In addition, in order to prevent damage to the cargo hold due to overpressure or underpressure, the pressure inside the cargo hold also needs to be monitored.
When LNG ships transport liquefied natural gas, they store it in insulated containers at -162°C. The measuring instruments used must be specially designed for this extremely low temperature environment. When transporting LNG, it is necessary to reliably measure the pressure, liquid level and limit of the cargo tank.
On a tanker, a manifold joint or Manifold is a part used to connect hard pipes or hoses when loading and unloading cargo. Monitoring of pipeline pressure at the Manifold secures installations both ashore and on board and controls the operation of pumps. For safe cargo handling, reliable pressure transmitters are indispensable.
The extracted crude oil will be pumped directly into the cargo oil tank on the ship, and then the oil, gas and water will be separated by gravity to form layers. In order to maximize the capacity utilization of the oil storage ship and effectively control the operation of the oil pump, it is necessary to continuously measure the liquid level and monitor the limit.
Cargo tanks on ships require level and pressure sensors for efficient and safe transportation of various types of cargo. These sensors play a crucial role in maintaining a stable environment within the tanks and preventing accidents or damage caused by overfilling, temperature fluctuations, and pressure changes.
Cargo tanks for shipbuilding are specifically designed to store and transport various types of cargo, particularly oil. They are equipped with inert gas systems and crude oil washing systems to ensure safety and efficiency.
In order to ensure the fuel supply of the main engine, the separated heavy oil (HFO) is first pumped to the sedimentation tank (clarification tank), and then enters the daily use tank (daily use tank) through continuous high overflow. The daily use tank is directly connected to the main engine. . The heating coil heats the oil to 75°C to 90°C. Reliable liquid level measurement ensures ship maneuverability.
The fresh water on the ship is stored in the fresh water tank. Depending on the type and size of the ship, a certain amount of fresh water is required for drinking and daily sanitation and cleaning. It is stipulated here that an electronic liquid level gauge must be used for liquid level measurement.
Sewage on large ships, also known as gray water or black water, can be treated by the ship’s sewage treatment system or stored in gray water tanks/black water tanks to await discharge. It is stipulated here that an electronic liquid level gauge must be used for liquid level measurement.
The hydraulic oil used to transmit power circulates in a closed system. There is also loss of hydraulic oil as the power unit needs to be lubricated and leaks can occur. In order to ensure the normal operation of the hydraulic system, it is necessary to monitor the oil level of all hydraulic oil tanks.
Shipbuilding service tanks require pressure and level sensors for accurate measurement and control. These sensors play a crucial role in ensuring the efficient functioning of various systems on ships. These sensors are designed to be durable, reliable, and resistant to corrosion to withstand the harsh marine environment.
SenTec online resource library is a place you can know more knowledge from video, cases study, e-book etc.