The melt pressure sensor, also called the melt pressure transducer or melt pressure transmitter, which is designed for high temperature melt extrusion line or fibre industrial application, application temperature could reach up to 700 C degree. SenTec melt pressure sensor divided into standard type, ROHS environmental type, explosion-proof type.
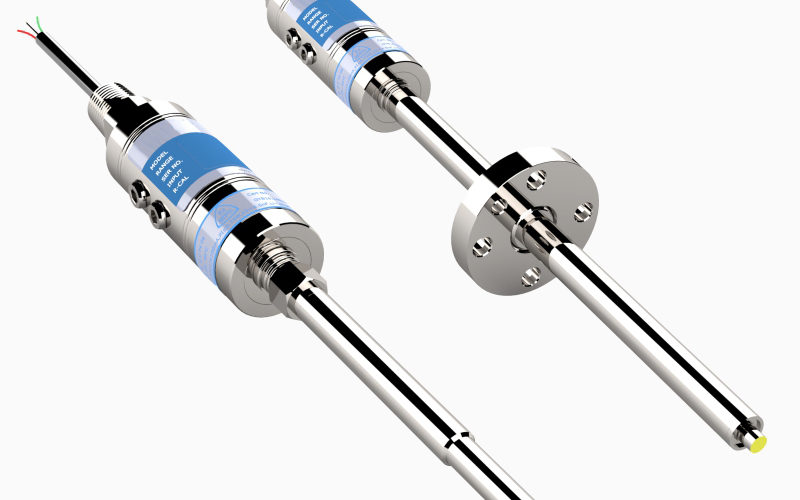
melt pressure sensor working principle
The working principle of the melt pressure sensor is that the pressure of the medium directly acts on the diaphragm of the sensor. The diaphragm produces a micro-displacement proportional to the pressure of the medium. The resistance of the sensor changes. The change is detected by electronic circuits. The conversion outputs a standard signal corresponding to this pressure.
Melt pressure transducers and transmitters employ the piezoresistive working principle: the pressure medium is converted into an electrical signal by a Wheatstone bridge built with 4 piezoresistors.
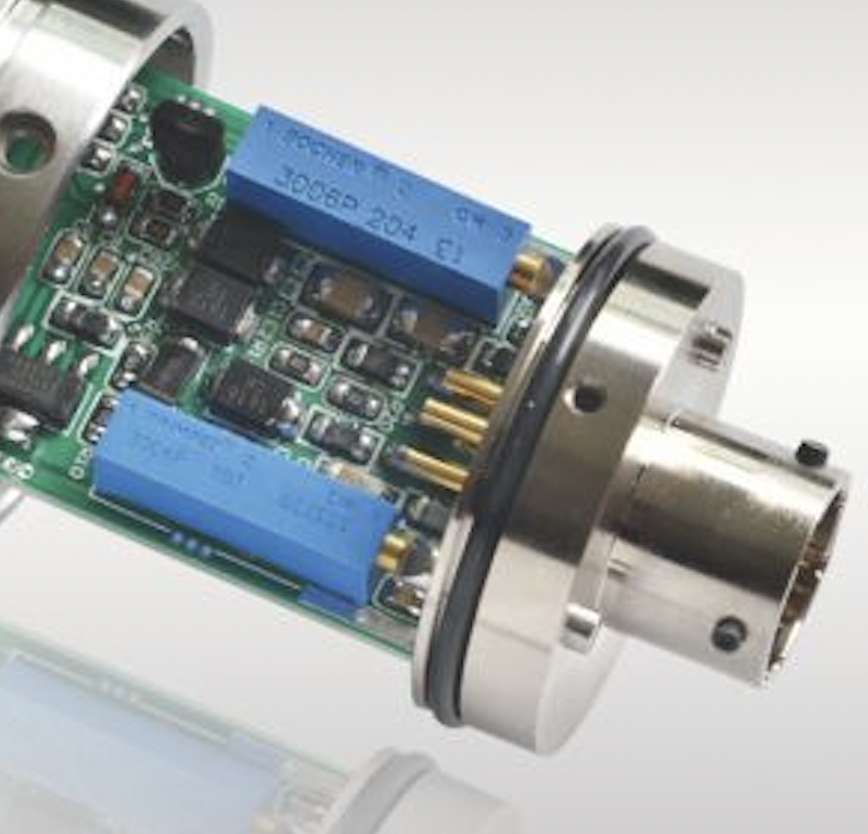
Melt pressure transmitter zero debugging:
1. During factory debugging, when the pressure is 0, press the reset button or short the D.E pin, the digital potentiometer will automatically adjust the zero point of the circuit to 4.0±0.02mA/0.01+0.01V, if the zero point exceeds the standard, enter the signal fine-tuning mode.
Melt pressure transducer full scale debugging:
Pressure to the full scale, adjust the potentiometer to output 20.0±0.02mA/10.00±0.02V, then release the pressure to 0, see if the zero point is within the standard range, if not, press the reset button or short the DE pin to clear Zero, then pressurize to full scale, adjust the potentiometer, until the output is 20.0±0.02mA/10.00±0.02V, repeat several times to reach the standard.
Precautions for buying high temperature melt pressure sensors
1. What kind of pressure is being measured. Generally, the maximum pressure range of the high temperature melt pressure sensor you need should reach 1.5 times the maximum pressure value of your system. All high temperature melt pressure sensors are designed to withstand the maximum pressure for 200 million cycles without degrading performance. You need to find a compromise solution between system performance and high temperature melt pressure sensor life.
2. Consider the type of media that needs to be measured. The key factor to consider when selecting a high temperature melt pressure sensor is the medium being measured. Will it be a viscous liquid or a slurry on the pressure head? Is the contact with the high temperature melt pressure sensor a soluble or corrosive medium or clean dry air? This question determines whether impact dies are needed and what materials are used to make contact with the media.
3. Consider the accuracy you need to achieve. Accuracy is a term commonly used by manufacturers to describe the output error of high temperature melt pressure sensors. The cost of having a higher accuracy high temperature melt pressure sensor will be higher. Does your system really needs such high accuracy ? A system consisting of a high-precision high-temperature melt pressure sensor and a low-resolution instrument is actually a low-efficiency solution.
4. Carefully consider the temperature resistance, interchangeability, time stability and ruggedness of the high temperature melt pressure sensor to be purchased.
5. What output method does the high temperature melt pressure sensor you want to use. The required excitation voltage, and how to connect the high temperature melt pressure sensor to your electrical system.
Installation tips for Melt pressure transducers/transmitters
➢ Correct installation
Usually, damages of pressure sensor caused by the inappropriate installation. If the sensors installed in the too small hole or irregular shape hole, it could cause damage by the vibration impact for the sensor membrane. Choosing the right mounting processing holes tools are beneficial to control the size of the installation holes. In addition, the right installation torque can help to form good seal. But, the sensors will slip away caused by the high installation of torques. To prevent this kind of phenomenon, usually, the anti-separation compounds should be painted on the thread part of the sensor before installation. After used the anti-separation compounds, even the high installation of torque, it’s different for sensors slipped away.
➢ Checking the size of the installation holes
If the size of the installation holes are not proper, in the process of installation, the thread portion is susceptible to wear. That will not only influence the sensors’ sealing performances, but also can not play sensors’ full role, and may even cause safe hidden troubles. Only the right installation holes can avoid thread wear (threaded industrial standard 1/2-20 UNF). Usually, it is necessary to test the mounting holes by using installation holes measuring instruments and to make appropriate adjustments.
➢ Keeping mounting holes clean
It is very important to keep mounting holes clean and prevent melt material blocking to ensure the its normal operation. Before the extruder is cleaned, all the sensors should be removed from the barrel to avoid damage. During the sensor demolition, melt material is likely to flow into the mounting holes and harden. If these remnants melting material is not removed, the top of the sensors may be caused damage when they are installed once again. Using Clean kit can remove these melt material residues. However, if it happened, the repeat cleaning process may deepen installation holes of sensor damage. If it was happened, it is necessary to take some measures to rise the sensors position in the installation holes.
➢ Choosing appropriate position
When sensor installation position is too close to the upstream of the production line,the non-molten material may wear the top of the sensor. If too close to the downstream, there may appear the molten material dead zone between the sensor and screw line where melting materials may produce degradation and may also cause distortion of pressure signal when transmitted. If too deep installed into barrel, damage may also caused by the touch between the sensor top and screw in its process of rotating. Generally speaking, the sensor can be located in the machine barrel in front of the strainer, or before or after the melt pump, or in the mould.
➢ Careful cleaning
You’d better dismantle all sensors before cleaning by using steel wire brush or special compounds. Because these two cleaning ways may cause the vibration of the sensors’ membranes. When the barrel was heated, sensors also should be dismantled and be wiped with soft cloth. At the same time, the sensor installation holes also need to clean using clean drilling machine and guide sleeve.
