The 4-20mA standard has long been the backbone of industrial signal transmission, providing a reliable method for conveying crucial data in industrial settings. This article aims to demystify the 4-20mA standard, exploring its advantages, components, working principles, applications, troubleshooting, and future trends. By the end, you will have a comprehensive understanding of 4-20mA and its significance in industrial environments.
4-20mA is a commonly used analog current signal, which is a standard signal. Refers to the minimum current of 4mA and the current of 20mA. When transmitting a signal, because there is also resistance on the wire, if the voltage is transmitted, a certain voltage drop will be generated in the wire, and the signal at the receiving end will have a certain error, so the current signal is generally used as the standard transmission of the sensor.
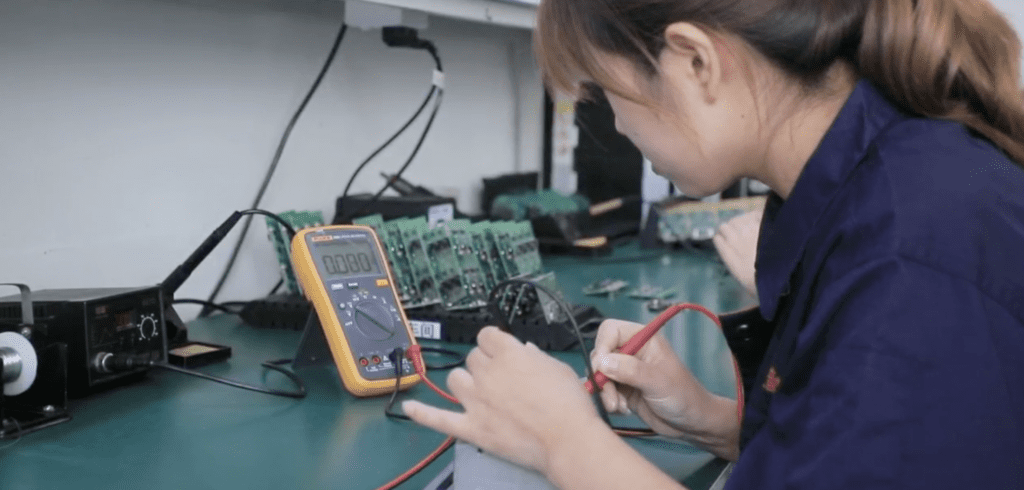
Because the current signal has strong anti-interference ability, is not easily interfered by external factors, and can be transmitted remotely, it is widely used in industrial sensors. In order to adapt to different situations in the industrial control industry, 4-20mA current sensors generally have four-wire, three-wire and two-wire systems.
Understanding the 4-20mA Standard
The 4-20mA standard is a widely used current loop signal for transmitting analog information in industrial automation and process control. Unlike voltage-based systems, the 4-20mA signal is less susceptible to voltage drops over long distances, making it ideal for extended wiring runs in industrial settings. This standard utilizes a 4-20mA current to represent a range of values, with 4mA typically indicating a low or zero reading, and 20mA representing the highest value within the defined range.
The 4-20mA standard offers several advantages over other signaling techniques. One of the key benefits is its ability to provide a robust and noise-immune signal, ensuring reliable data transmission even in electrically noisy environments. Additionally, the use of current rather than voltage for signal transmission allows for greater accuracy and precision, as current signals are less affected by resistance variations in the wiring.
In industrial applications, the 4-20mA standard has become the preferred choice for transmitting sensor data due to its resilience to electrical interference and suitability for long-distance transmission. This standard is commonly employed in industries such as manufacturing, oil and gas, water treatment, and chemical processing, where the accurate and reliable transmission of sensor data is critical for operational efficiency and safety.
The reason why the current source for remote signal is better than the voltage source
Because the distance between the field and the control room is far, and the resistance of the connecting wire is large, if the voltage source signal is used for remote transmission, a large error will occur due to the voltage division between the wire resistance and the input resistance of the receiving instrument, and the constant The current source signal is used as a remote transmission. As long as there is no branch in the transmission loop, the current in the loop will not change with the length of the wire, thus ensuring the transmission accuracy.
The reason for choosing 20mA for the acquisition signal current
The safety spark meter can only use low voltage and low current. The spark energy caused by the on-off of 20mA current is not enough to ignite the gas, so it is very safe; the choice of current 20mA is based on the consideration of safety, practicality, power consumption and cost.
Why is the starting point of 4-20mA not 0mA
When the sensor is wired, it may cause poor contact or disconnection for some reasons. After the disconnection, the receiving device cannot collect the current signal, which will cause the real 0mA and the disconnection to be confused together and cannot be judged. If the starting point is set For 4mA, it is easy to judge the disconnection. At the same time, setting to 4 mA has many advantages for two-wire signal transmission.
Advantages of current signal 4~20mA signal
1. The current signal is suitable for long-distance transmission, because the current signal is not affected by the resistance of the wire, while the voltage signal will divide the voltage when the wire itself has resistance, resulting in inaccurate measurement. Generally, the maximum transmission distance of 4~20mA is controlled within 100m, and it is recommended to use digital signals (485 communication) for further distances.
2. The current signal generally adopts a two-wire system, and the voltage signal generally adopts a three-wire system. In contrast, the two-wire system saves materials and reduces costs compared with the three-wire system.
3. Compared with the more complex on-site working conditions, the anti-interference ability of the current signal is stronger than that of the voltage signal. In the case of interference, it is recommended that the user select a 4~20mA signal.
4. The current signal can appropriately exceed the range of the range, and no signal is output. For example, a pressure transmitter with a range of 1MPa and an output of 4~20mA can output 24mA when the range is exceeded.
The voltage signal is slightly different depending on the power supply. For example, a pressure transmitter with a range of 1MPa and an output of 0~10V cannot output a signal above 9V when the power supply is 9V.
5. When the wire material is different (such as copper, nickel), a magnetic field will generally be generated, and there will be errors in the voltage signal and no current signal in the case of high precision requirements.
Components of a 4-20mA System
A typical 4-20mA system consists of several key components that work together to ensure the accurate transmission of analog data. The primary components include the sensor or transmitter, the signal conditioning circuitry, the current loop, and the receiving or control device.
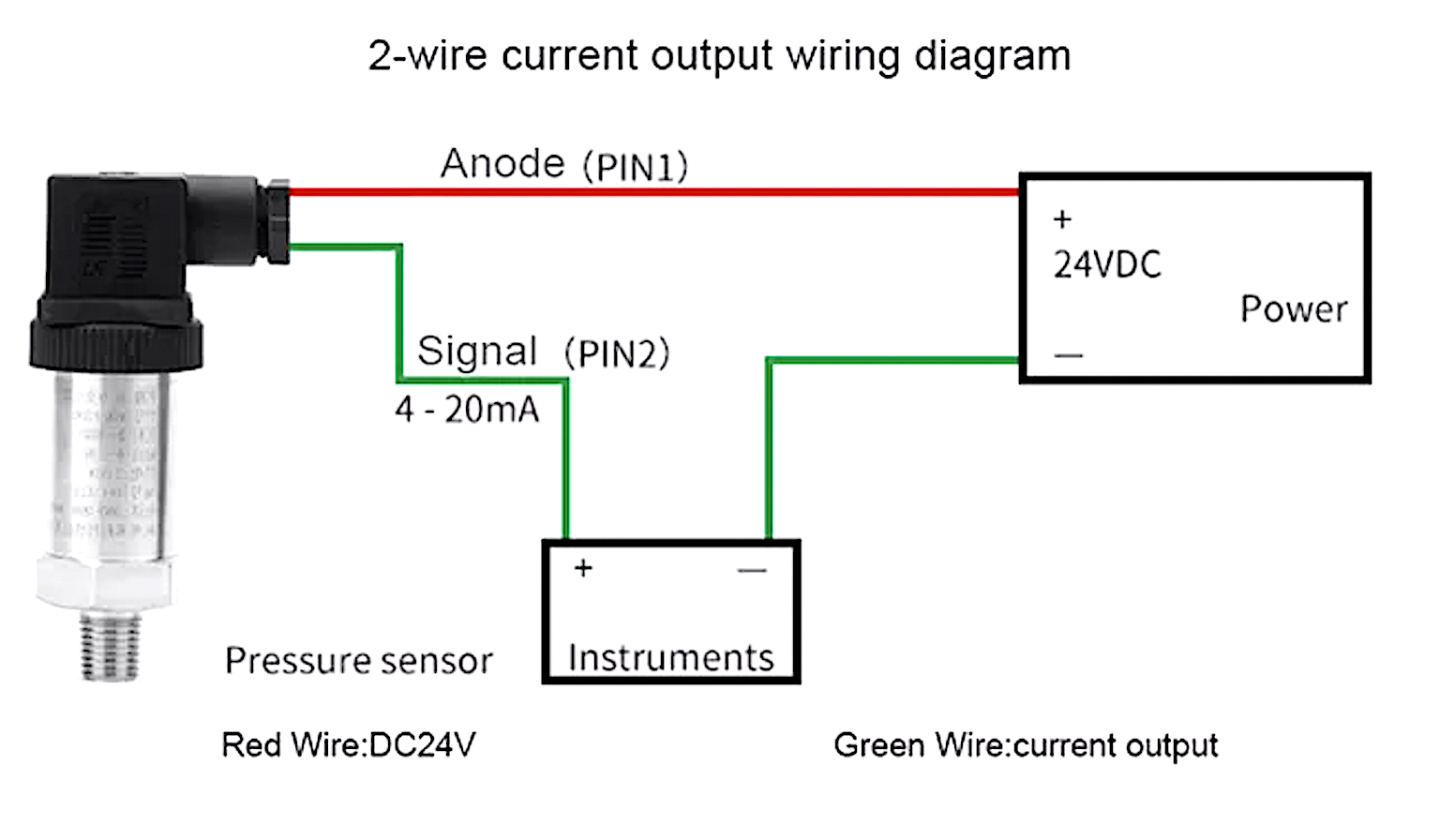
The sensor or transmitter is responsible for converting the physical parameter, such as pressure, temperature, flow, or level, into a corresponding 4-20mA current signal. This signal is then passed to the signal conditioning circuitry, which may include amplifiers, filters, and isolation devices to ensure the integrity of the transmitted data and protect the system from external disturbances.
The current loop forms the backbone of the 4-20mA system, carrying the analog signal from the sensor to the receiving device. It typically consists of a two-wire connection, with the current flowing from the power supply, through the sensor, and back to the receiving device. The receiving or control device interprets the 4-20mA signal and converts it into a readable format for monitoring, control, or further processing.
How 4-20mA Signals Work
Understanding the working principles of 4-20mA signals is essential for grasping their significance in industrial applications. The 4-20mA standard operates on the basis of current regulation, where the magnitude of the current flowing through the loop corresponds to the value of the measured parameter. A 4mA current typically represents the lowest or zero value of the parameter being measured, while a 20mA current indicates the highest value within the specified range.
The relationship between the measured parameter and the 4-20mA current signal is typically linear, allowing for straightforward interpretation and conversion of the transmitted data. This linearity simplifies the calibration and scaling of the sensor output, making it easier to map the current values to the corresponding physical quantities being measured. Additionally, the use of current rather than voltage for signal transmission minimizes the impact of resistance variations in the wiring, contributing to the accuracy and reliability of the transmitted data.
The working principles of 4-20mA signals also involve the concept of loop-powered devices, where the current loop not only carries the analog signal but also provides the necessary power for the sensor or transmitter. This feature eliminates the need for a separate power supply at the sensor location, simplifying the wiring and reducing installation costs in industrial environments.
Applications of 4-20mA Signals in Industrial Settings
The versatility and reliability of the 4-20mA standard have led to its widespread adoption across various industrial sectors. In manufacturing environments, 4-20mA signals are commonly used to transmit data from pressure, temperature, and flow sensors, providing crucial information for process monitoring and control. The ability of 4-20mA signals to withstand electrical noise and travel long distances makes them well-suited for such applications, ensuring that the transmitted data remains accurate and timely.
In the oil and gas industry, 4-20mA signals play a vital role in monitoring and controlling various parameters, including level, pressure, and flow in pipelines, storage tanks, and processing facilities. The robustness of the 4-20mA standard makes it an ideal choice for these applications, where environmental factors and operational safety are of utmost importance.
Water treatment facilities rely on 4-20mA signals to convey data from level, pH, and turbidity sensors, enabling efficient management of water purification processes. The noise immunity and long-distance transmission capabilities of the 4-20mA standard make it well-suited for the demanding conditions encountered in water treatment plants, ensuring accurate and reliable data transmission for effective process control.
Troubleshooting and Maintenance of 4-20mA Signal Systems
While 4-20mA signal systems are known for their reliability, it is essential to have robust troubleshooting and maintenance practices in place to ensure continued operational integrity. One common issue encountered in 4-20mA systems is signal loss due to wiring faults, sensor failures, or improper connection. Regular inspection of the wiring, connectors, and sensor integrity is crucial for identifying and rectifying these issues in a timely manner.
Another aspect of maintenance involves ensuring the proper calibration and scaling of the sensors to accurately reflect the physical parameters being measured. Periodic calibration checks and adjustments are necessary to maintain the accuracy of the transmitted data and prevent deviations that could impact process control and safety.
Additionally, proactive diagnostics and fault detection play a key role in the maintenance of 4-20mA signal systems. Monitoring the current loop for abnormalities, such as open circuits, short circuits, or sensor drift, allows for early identification of potential issues, enabling timely intervention to prevent system downtime and data inaccuracies.
Comparison of 4-20mA with Other Industrial Signal Standards
While the 4-20mA standard has established itself as a reliable and widely adopted method for industrial signal transmission, it is essential to consider its strengths and limitations in comparison to other signal standards. Voltage-based signals, such as 0-10V and 0-5V, offer simplicity and ease of use, especially in applications where the receiving devices are designed to interpret voltage signals directly.
However, voltage-based signals are more susceptible to signal degradation over long distances and are prone to interference from electrical noise, which can impact the accuracy and reliability of the transmitted data. In contrast, the 4-20mA standard excels in noise immunity and long-distance transmission, making it the preferred choice for industrial applications where these factors are critical.
Another signal standard worth considering is the digital communication protocol, such as Modbus or Profibus, which offers the advantage of transmitting digital data packets with inherent error checking and correction capabilities. While digital protocols provide robustness in data transmission, they may require more complex wiring and additional signal conditioning, making them less cost-effective and practical for certain industrial applications compared to the simplicity and efficiency of the 4-20mA standard.
Future Trends in 4-20mA Technology
As industrial automation and digitalization continue to evolve, the 4-20mA standard is not immune to advancements and innovations. One notable trend in 4-20mA technology is the integration of wireless communication for remote monitoring and control. Wireless transmitters capable of converting sensor data into 4-20mA signals and transmitting them over wireless networks offer flexibility and cost savings in industrial installations where wired connectivity may be challenging or impractical.
Another emerging trend is the incorporation of smart sensor technologies within the 4-20mA standard, enabling sensors to provide additional diagnostic information and self-monitoring capabilities. Smart sensors equipped with microprocessors and onboard diagnostics can enhance the reliability and maintainability of 4-20mA signal systems, allowing for predictive maintenance and proactive fault detection.
Furthermore, advancements in power-efficient circuitry and energy harvesting techniques are paving the way for ultra-low-power 4-20mA sensors that can operate without external power sources. These developments have the potential to expand the applicability of 4-20mA signals in remote and energy-constrained industrial environments, opening up new opportunities for sensor deployment and data acquisition.
Implementing 4-20mA Signal Systems in Industrial Environments
When implementing 4-20mA signal systems in industrial environments, several factors must be carefully considered to ensure optimal performance and reliability. Selecting the appropriate sensors and transmitters for the specific application is crucial, taking into account the environmental conditions, measurement range, accuracy requirements, and compatibility with the existing control and monitoring infrastructure.
Proper installation and wiring practices are essential to minimize signal loss and interference in 4-20mA systems. Attention should be given to proper grounding, shielding, and separation of power and signal wiring to prevent electrical noise from affecting the transmitted data. Additionally, the use of surge protection devices and isolation barriers can further safeguard the integrity of the 4-20mA signal in the presence of electrical disturbances.
Regular maintenance and periodic calibration of the 4-20mA signal systems are imperative to ensure continued accuracy and reliability of the transmitted data. Implementing a comprehensive maintenance schedule that includes inspection, testing, and calibration procedures will help mitigate potential issues and prolong the operational lifespan of the 4-20mA signal systems.
Conclusion
In conclusion, the 4-20mA standard stands as a cornerstone of industrial signal transmission, offering unparalleled reliability, noise immunity, and long-distance transmission capabilities. Its widespread adoption across diverse industrial sectors underscores its significance in enabling efficient process control, condition monitoring, and safety critical applications. As technology continues to evolve, the 4-20mA standard is poised to embrace wireless communication, smart sensor integration, and energy-efficient solutions, further enhancing its utility in the rapidly advancing landscape of industrial automation.
CTA: For more insightful articles on industrial signal transmission and automation, explore our comprehensive range of resources and stay ahead in the world of industrial technology.